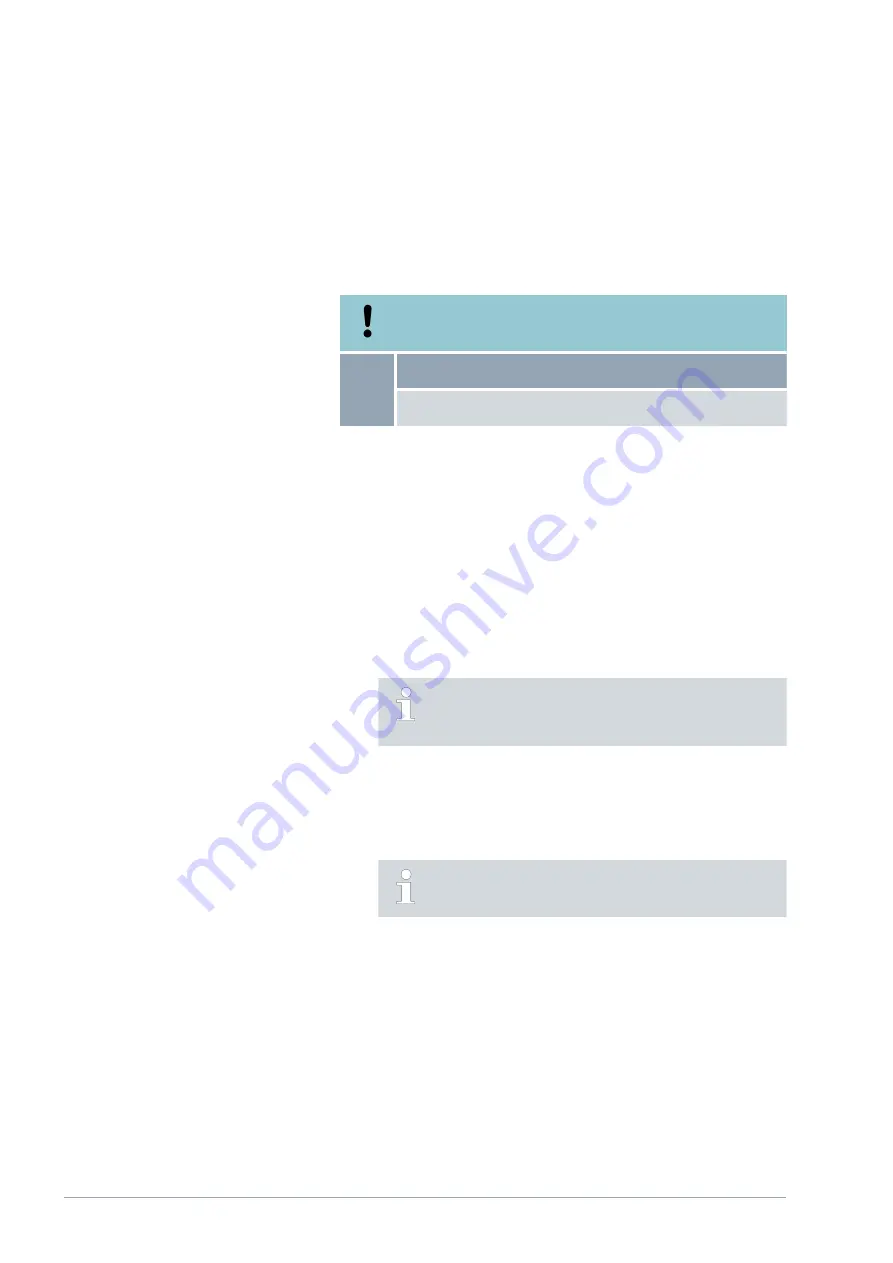
6 Operation
6.1
Switching on the device
NOTICE!
Overheating of the pump
Device damage
Never operate device without heat transfer liquid.
Personnel:
n
Operating personnel
1.
Switch on the device using the mains power switch.
A signal tone sounds. The software version is shown on the dis-
play. The actual temperature is shown on the display afterwards.
The temperature control device starts operation; the pump is
started.
Depending on the specified setpoint temperature, the refrigerant
unit is started after 2 minutes at the earliest. The blue LED lights
if the refrigerant unit is active.
2.
Depending on the size of the consumer, heat transfer liquid must be
refilled if necessary. Monitor the level indicator for this.
Further information about refilling heat transfer liquid can be
found in
Ä
Chapter 5.3 ‘Switching on the device and
filling with heat transfer liquid’ on page 30
.
6.2 Default display and menu items
1.
Press the ENTER button to reach the menu items from the default
display of the actual temperature.
If no button has been pressed for longer than 4 seconds, you
exit from the menu item or input window.
2.
Scroll from menu item to menu item using the arrow buttons.
3.
Press the ENTER button at the selected menu item.
The display flashes.
4.
The value or the setting can be changed using the arrow buttons.
V05REV08
Microcool
34 / 57
Summary of Contents for MC 250
Page 36: ...Fig 12 Menu V05REV08 Microcool 36 57...
Page 58: ......
Page 60: ......
Page 62: ......
Page 63: ......