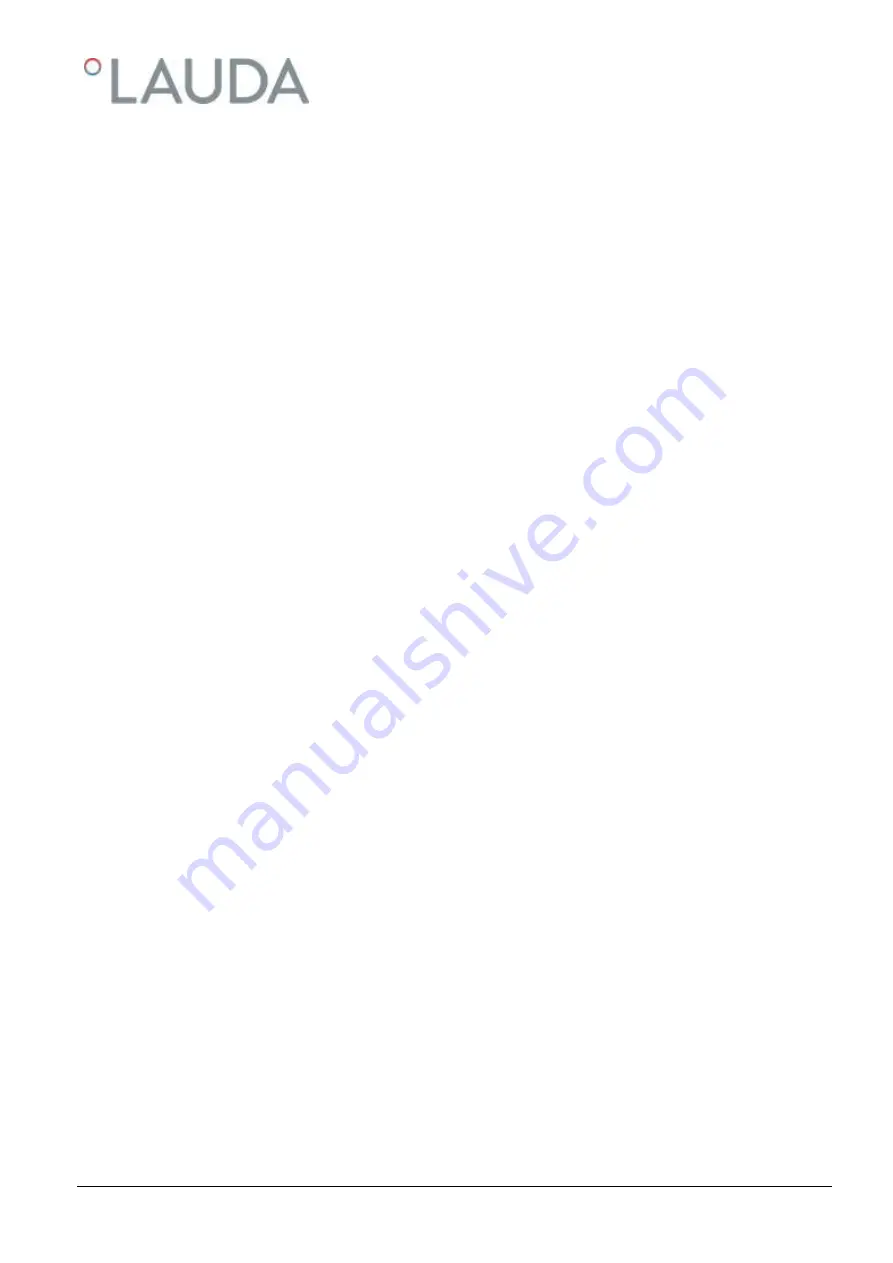
ECO Gold
5 / 137
Table of contents
1
Safety ............................................................................................................................................................................................... 9
1.1
Safety information ................................................................................................................................................................. 9
1.2
General safety ..................................................................................................................................................................... 10
1.3
Special safety information .................................................................................................................................................. 11
2
General remarks ........................................................................................................................................................................... 13
2.1
Description of the device ................................................................................................................................................... 13
2.2
Intended application............................................................................................................................................................ 13
2.3
Use other than that intended ............................................................................................................................................. 13
2.4
Responsibility of the operating body - safety information .............................................................................................. 13
2.5
Materials .............................................................................................................................................................................. 14
2.6
EU conformity..................................................................................................................................................................... 14
3
Device description ....................................................................................................................................................................... 15
3.1
Device types ........................................................................................................................................................................ 15
3.2
Pump .................................................................................................................................................................................... 15
3.3
Programmer ........................................................................................................................................................................ 15
3.4
Interfaces ............................................................................................................................................................................. 15
3.5
Interface modules (Accessories) ....................................................................................................................................... 16
3.6
Chiller ................................................................................................................................................................................... 16
4
Operating and functional controls ............................................................................................................................................. 17
5
Transport and unpacking ............................................................................................................................................................. 24
6
Before putting the device into operation .................................................................................................................................. 26
6.1
Assembly and siting ............................................................................................................................................................. 26
6.2
Connection of external consumers ................................................................................................................................... 32
6.3
Filling and emptying ............................................................................................................................................................ 35
6.4
Heat transfer liquids, cooling water and hoses ................................................................................................................. 37
6.5
Cooling of heating thermostats ......................................................................................................................................... 41
6.6
First switch-on .................................................................................................................................................................... 41
6.7
Installation of modules ........................................................................................................................................................ 42
7
Operation ..................................................................................................................................................................................... 44
7.1
Switching on ........................................................................................................................................................................ 46
7.2
Menu structure ................................................................................................................................................................... 47
7.3
Display representation ........................................................................................................................................................ 49
7.3.1
Basic window ............................................................................................................................................................... 49
7.3.2
Menu window .............................................................................................................................................................. 49
7.3.3
Entry window .............................................................................................................................................................. 50
7.3.4
Graphics window ........................................................................................................................................................ 51
Summary of Contents for ECO GOLD
Page 1: ...Operation manual ECO Gold ...
Page 2: ......
Page 4: ......
Page 81: ...10 2019 i ECO Gold 81 137 W Warnings 55 92 X Xp 106 Xpf 108 ...
Page 82: ...82 137 ECO Gold 10 2019 i ...
Page 83: ...10 2019 i ECO Gold 83 137 ...
Page 84: ...84 137 ECO Gold 10 2019 i ...
Page 85: ...10 2019 i ECO Gold 85 137 Appendix with settings ...
Page 121: ...10 2019 i ECO Gold 121 137 Click on the tab with the mouse and then on the Device manager ...
Page 130: ......
Page 132: ......
Page 133: ......
Page 134: ......
Page 135: ......