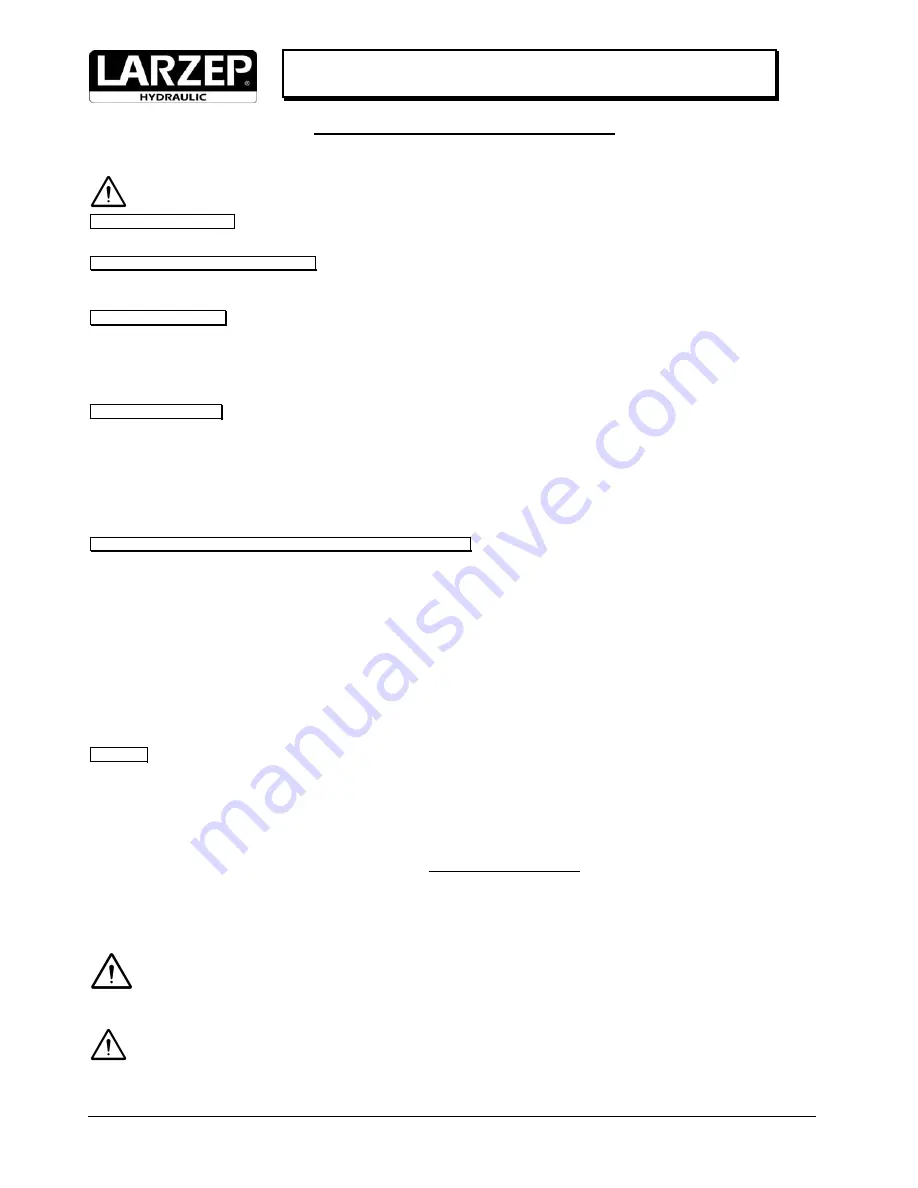
4
Instruction Manual
Bench Press with Electric Pump “ECE02015-CE”
4. TRANSPORT AND INSTALLATION.
The machine is delivered properly packed in a wooden ballet. For it’s handling, it is recommended to use a forklift truck or a crane. In the last case, it is necessary to
make the slings trespass the arc of the frame. When doing this operation, you should be cautious and prevent the flexible hoses and couplings from any damage.
The machine is stable enough to operate without fixing, but if is placed in an area commonly operated by mobile machinery (cranes, lifting equipment…)
it is strongly recommended to fix it to the desired place by drilling the supporting plates.
HYDRAULIC CONNECTION
Unscrew the rapid coupler site in the cylinder, and connect the hose, screwing the rapid coupler to the limit with the hand.
SUBSTITUTION OF THE TRANSPORT PLUG
Replace the plug of the transport located in the cover of the tank by the pressurized plug given with the press. (Plastic stock marked in the handle of the distributing
valve).
INSTALLING THE GAUGE
1-Replace the threaded tap in the top of the cylinder by the gauge (supplied separately).
2-Tighten the gauge cone to the gauge adaptor seat by using a flan wrench size 22.
3-Hold the gauge screen by hand during threading process and after reaching a comfortable reading position set the gauge screen free so that it turns the last quarter
solidarily with the thread.
4- The power pack is also provided with a gauge adaptor, with thread 3/8” BSP.
ELECTRIC CONNECTION
1-
Connect the binding post to the network
2-
See the voltage, it must be 380 V
3-
Assure that the panel of push button is not pushed, and that the selector is in “manual” way (left.)
4-
Put the general selector of the lateral of the electric cabinet in (1) position.
5-
Push the green button. The motor starts.
6-
Check that the motor goes in the sense labelled with and arrow in the motor. In opposite case, change the position of two cables between themselves in the
terminal and try again. This operation must be done with the equipment disconnected.
7-
Connect again the equipment and check the function of the emergency red button located in the panel of push button.
CHECKING THE RIGHT OPERATION OF ALL DEVICES AND MECHANISM
1.
Select the working maximum pressure.
2.
Put the general selector in position (1).
3.
Push the green button to start the motor.
4.
Check that the cylinder’s piston advance.
5.
Check that the cylinder’s piston returns pushing by an internal spring. In both cases, to maintain the movement, it is necessary to keep pushed the
button.
6.
With no material in the press, repeat the movement of advance, reaching the end of the stroke of the cylinder. In this moment the pressure will go
increasing, so the gauge will read the pressure. This pressure will go increasing until reach the maximum pressure of the installation, previously
chosen. The cylinder maintains the reached pressure and the gauge the pressure reading check that there is not oil leaks.
7.
To return the piston and depressurize the installation push the panel of button. The piston returns by the internal spring. The return could be slower in
the end of the return stroke.
8.
Put the material to be treated in the press.
9.
Once the operation is finished, push the red button to stop the motor.
10.
Put the general selector in (0) position,
START UP
Connect the machine as described in the previous point.
The maximum pressure that the hydraulic equipment develops is 700 kg/cm
2
.
The machine is provided with an external limiter valve rated on factory at 700 kg/cm
2
.
In the cover of the power pack is located the pressure regulation screw.
Release the lock nut and go tightening or releasing the screw, go checking with the gauge, and once that the wished pressure is reached; tighten the lock nut to avoid
that the vibration may decontrol the system.
5. MAINTENANCE.
The hydraulic circuit of the press is closed, so in normal conditions no oil leakage should be coming up.
In case of oil leakage, after the proper repairing work, you should fill up the tank with hydraulic oil by LARZEP (
Ref. AZ8901
); the pump is equipped with an oil
level indicator to control the need quantity of oil.
As far as a non-continuous use of the press is concerned (1 hour per day), oil replacement should be done once a year.
To empty the tank, you should remove the cover and take the oil out to another container. Please, bear in mind the existing rules for waste processing
when handling the used oil.
Keep greasy and lubricated the pin bearings, the piston and in general all the parts that might be in friction.
USE ONLY LARZEP HYDRAULIC OIL
Other grades of oils or types of hydraulic fluid (such as brake fluid) may affect the performance of the equipment or cause the deterioration of the seals.
DO NO ATTEMPT TO FILL THE PUMP WITH OIL WHILE IT IS CONNECTED TO A CYLINDER WHICH IS SUSTAINING A LOAD BECAUSE
IT MAY OVERPRESSURIZE THE RESERVOIR WHEN THE PISTON RETRACS AND CAUSE DAMAGE OR INJURY
Always use the original LARZEP parts to prolong the service life of your hydraulic equipment.
LARZEP S.A
. or your authorized dealer can supply you with
original parts for simple maintenance work.