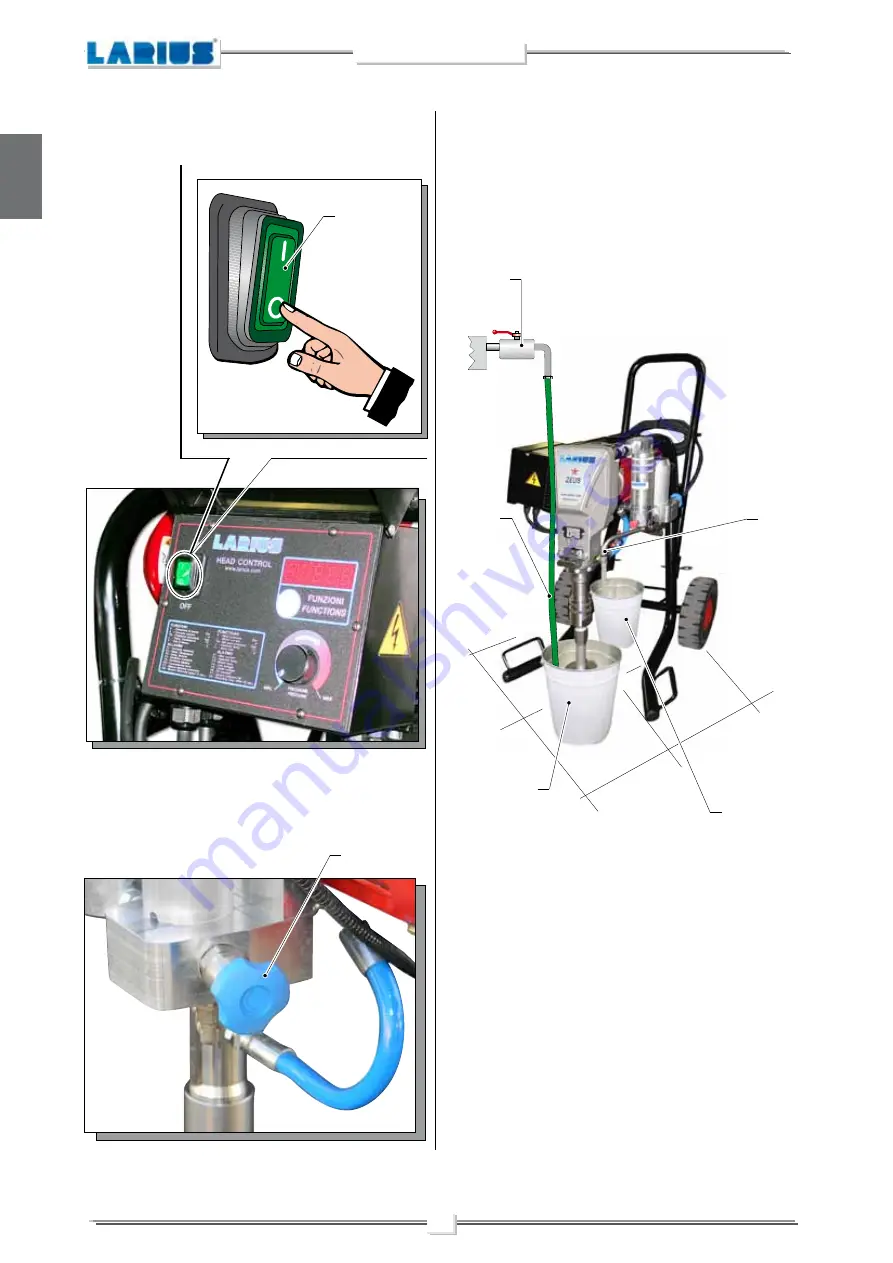
ZEUS
20
English
•
Press the switch (
H2
) “
OFF
(0)”
placed on the box of the
electric motor, to stop the equipment.
•
Hold the spray gun trigger down.
•
Open the circulation - safety valve (
H3
) to discharge the
pressure in the circuit.
•
Lift the suction hose and replace the bucket of product with
an empty bucket (
H6
).
•
Connect a rubber hose (
H7
) to a water tap (
H8
) and fill the
bucket (
H6
).
•
Position an empty bucket to collect the water (
H9
) under the
circulation hose (
H10
).
H2
OFF
H8
H7
H10
H9
H6
H3
Open