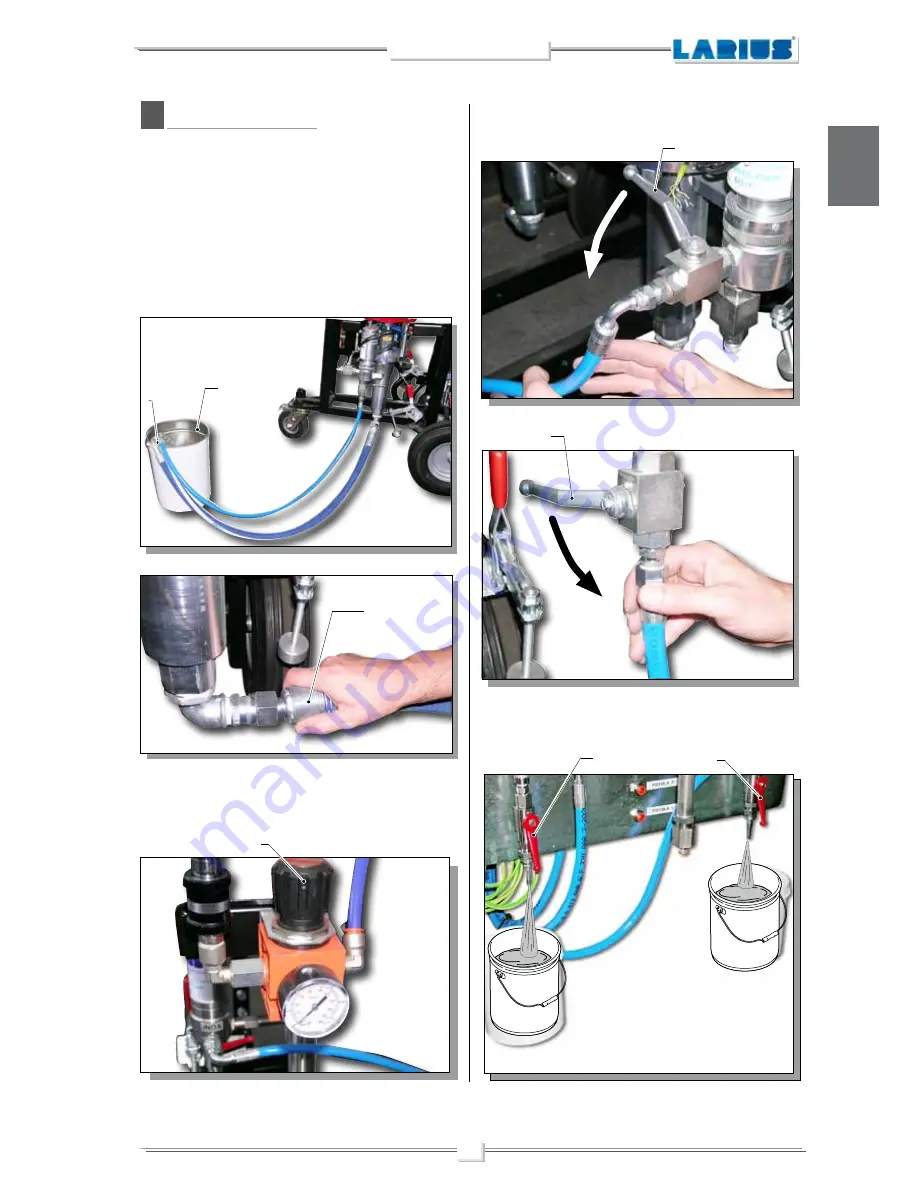
21
NOVA MIX 2K
English
H7
H7
H4
H
WASHING
Empty any product present inside the machine.
For example, after complete washing (the machine has sucked
up solvent).
• Remove the floaters (
H1
) from the drums (
H2
) or unscrew and
detach the supply tube (
H3
) from the pumps, to be sure that the
pumps can no longer suck up the products.
H2
H1
• Set the pressure of the pumps (
H4
) to the minimum for them to
work, using the regulators on the pumps themselves.
• Leave the delivery valves open (
H5
) and open the recirculation
valves as well (
H6
).
H5
H6
• Open the two relief valves located under the digital pressure
gauges (
H7
).
H3
MAINTENANCE