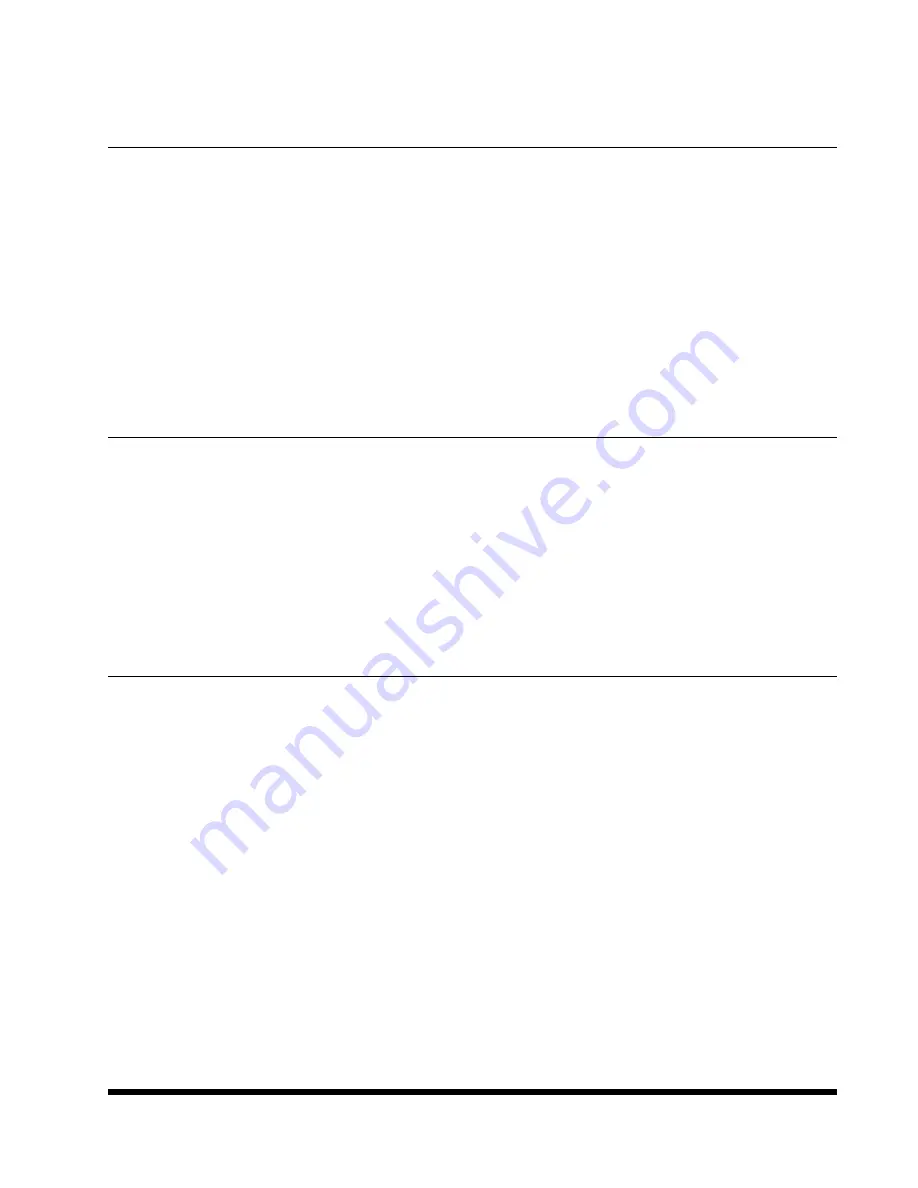
4-11 WHEEL BEARING MAINTENANCE
Wheel bearing maintenance should be per-
formed at the beginning of every season of use.
Check the wheel bearings periodically for exces-
sive end play. If needed, adjust or replace them
using the following procedure:
4-11.1
Place the frame on blocks or stands
sufficient to lift the tire clear of the ground.
4-11.2
Remove the hub cap, cotter pin, slotted
nut and washer.
4-11.3
Remove the hub. Clean and inspect the
bearings and hub cavity. Replace any worn
or defective parts.
4-11.4
Repack the bearings using a high-
quality wheel bearing grease.
4-11.5
Replace the hub with a new seal and
the inner bearing in place.
4-11.6
Install the outer bearing cone, washer
and slotted nut.
4-11.7
Tighten the slotted nut while rotating the
hub until there is a slight resistance to wheel
rotation. Then, back the slotted nut off one
notch, until the wheel rotates freely without
end play.
4-11.8
Install a new cotter pin and replace the
hub cap.
4-12 HYDRAULIC MAINTENANCE
4-12.1
Check the tractor hydraulic fluid level
per tractor owners manual and after any
leakage. Check fluid level with the cylinders
in the retracted position.
4-12.2
If a cylinder or valve leaks, disassemble
the parts to determine the cause of the leak.
Any time a cylinder is opened up, or when-
ever any seal replacement is necessary, it is
advisable to clean all parts and replace all
seals. Seal kits are available from your Lan-
doll dealer.
4-12.3
Check all hydraulic hoses weekly. Look
for binding or cracking. Replace all worn or
defective parts immediately.
4-13 LUBRICATION
4-13.1
specifies the
number and the period of lubrication points
on the
876 Wing Series Tilloll
. Proper main-
tenance of your machine will, under normal
operating conditions, help to keep it operat-
ing at or near its peak performance for an
extended period of time. Proper maintenance
is also a condition of keeping your warranty
in good status.
4-9
Summary of Contents for 876 Series
Page 4: ...ii...
Page 8: ......
Page 12: ...2 4 Figure 2 1 876 30 Shank Placement Assembly 1 of 2...
Page 13: ...2 5 Figure 2 2 876 30 Shank Placement Assembly 2 of 2...
Page 14: ...2 6 Figure 2 3 876 35 Shank Placement Assembly 1 of 2...
Page 15: ...2 7 Figure 2 4 876 35 Shank Placement Assembly 2 of 2...
Page 16: ...2 8 Figure 2 5 876 40 Shank Placement Assembly 1 of 2...
Page 17: ...2 9 Figure 2 6 876 40 Shank Placement Assembly 2 of 2...
Page 18: ...NOTES 2 10...
Page 20: ...3 2 Figure 3 1 Frame Wing and Extension Assembly...
Page 21: ...3 3 Figure 3 2 Frame Wing and Extension Assembly...
Page 22: ...3 4 Figure 3 3 Frame Wing and Extension Assembly...
Page 24: ...3 6 Figure 3 4 Shank Clamp and Sweep Assembly...
Page 26: ...3 8 Figure 3 5 Hydraulic Lift Assembly...
Page 28: ...3 10 Figure 3 6 Hydraulic Fold Assembly...
Page 30: ...3 12 Figure 3 7 Disc Gang and Spray Shield Installation...
Page 32: ...3 14 Figure 3 8 Reel Assembly Installation...
Page 34: ...3 16 Figure 3 9 Harrow Assembly Installation...
Page 36: ...3 18 Figure 3 10 Pull Hitch Installation...
Page 38: ...3 20 Figure 3 11 Electrical Installation...
Page 40: ...3 22 Figure 3 12 Decal Installation...
Page 42: ...NOTES 3 24...
Page 53: ...NOTES 4 11...
Page 54: ......
Page 58: ...NOTES 5 4...