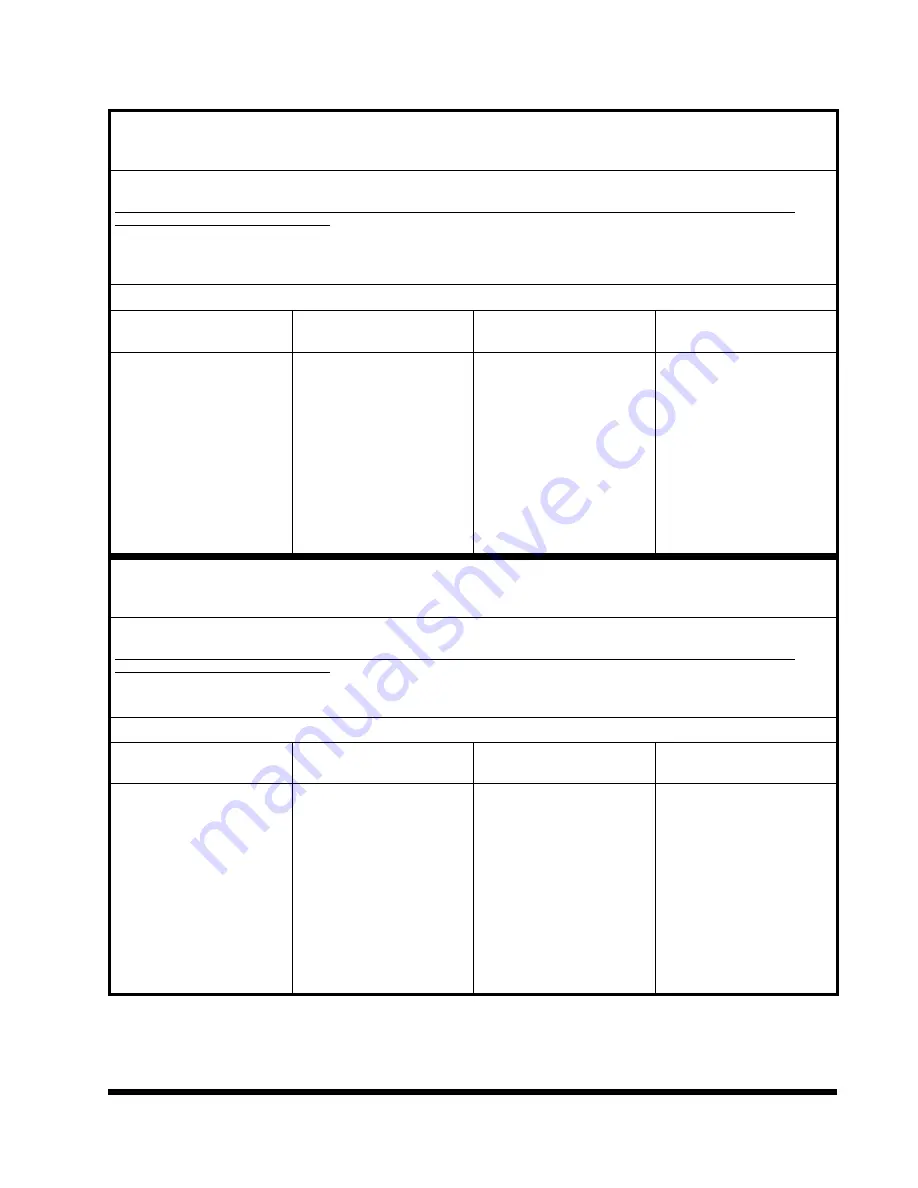
2-3
LANDOLL CORPORATION
HYDRAULIC FITTING TORQUE SPECIFICATIONS
37
o
JIC, ORS, & ORB (REV. 10/97)
THIS CHART PROVIDES TIGHTENING TORQUES FOR HYDRAULIC FITTING APPLICATIONS WHEN SPECIAL TORQUES ARE NOT SPECIFIED
ON PROCESS OR DRAWING.
ASSEMBLY TORQUES APPLY TO PLATED CARBON STEEL AND STAINLESS STEEL FITTINGS ASSEMBLED WITHOUT SUPPLEMENTAL
LUBRICATION (AS RECEIVED CONDITION)
.
THEY DO NOT APPLY IF SPECIAL GRAPHITE MOLY-DISULFIDE OR OTHER EXTREME
PRESSURE LUBRICANTS ARE USED.
BRASS FITTINGS AND ADAPTERS - 65% OF THE TORQUE VALUE FOR STEEL. STAINLESS STEEL, ALUMINUM AND MONEL - THREADS ARE
TO BE LUBRICATED.
TORQUE IS SPECIFIED IN FOOT POUNDS
PARKER BRAND FITTINGS
Dash
Size
37 Degree
JIC
O-Ring
(ORS)
O-Ring Boss
(ORB)
-4
11-13
15-17
13-15
-5
14-16
21-23
-6
20-22
34-36
25-29
-8
43-47
58-62
40-44
-10
55-65
100-110
57.5-62.5
-12
80-90
134-146
75-85
-16
115-125
202-218
109-121
-20
160-180
248-272
213-237
-24
185-215
303-327
238-262
-32
250-290
310-340
LANDOLL CORPORATION
HYDRAULIC FITTING TORQUE SPECIFICATIONS
37
o
JIC, ORS & ORB (REV. 10/97)
THIS CHART PROVIDES TIGHTENING TORQUES FOR HYDRAULIC FITTING APPLICATIONS WHEN SPECIAL TORQUES ARE NOT SPECIFIED
ON PROCESS OR DRAWING.
ASSEMBLY TORQUES APPLY TO PLATED CARBON STEEL AND STAINLESS STEEL FITTINGS ASSEMBLED WITHOUT SUPPLEMENTAL
LUBRICATION (AS RECEIVED CONDITION)
.
THEY DO NOT APPLY IF SPECIAL GRAPHITE MOLY-DISULFIDE OR OTHER EXTREME
PRESSURE LUBRICANTS ARE USED.
BRASS FITTINGS AND ADAPTERS - 65% OF THE TORQUE VALUE FOR STEEL.
TORQUE IS SPECIFIED IN FOOT POUNDS.
AEROQUIP BRAND FITTINGS
Dash
Size
37 Degree
JIC
O-Ring
(ORS)
O-Ring Boss
(ORB)
-4
11-12
10-12
14-16
-5
15-16
18-20
-6
18-20
18-20
24-26
-8
38-42
32-35
50-60
-10
57-62
46-50
72-80
-12
79-87
65-70
125-135
-14
160-180
-16
108-113
92-100
200-220
-20
127-133
125-140
210-280
-24
158-167
150-165
270-360
-32
245-258
Table 2-2 Hydraulic Fitting Torque Specifications
Summary of Contents for 876 Series
Page 4: ...ii...
Page 8: ......
Page 12: ...2 4 Figure 2 1 876 30 Shank Placement Assembly 1 of 2...
Page 13: ...2 5 Figure 2 2 876 30 Shank Placement Assembly 2 of 2...
Page 14: ...2 6 Figure 2 3 876 35 Shank Placement Assembly 1 of 2...
Page 15: ...2 7 Figure 2 4 876 35 Shank Placement Assembly 2 of 2...
Page 16: ...2 8 Figure 2 5 876 40 Shank Placement Assembly 1 of 2...
Page 17: ...2 9 Figure 2 6 876 40 Shank Placement Assembly 2 of 2...
Page 18: ...NOTES 2 10...
Page 20: ...3 2 Figure 3 1 Frame Wing and Extension Assembly...
Page 21: ...3 3 Figure 3 2 Frame Wing and Extension Assembly...
Page 22: ...3 4 Figure 3 3 Frame Wing and Extension Assembly...
Page 24: ...3 6 Figure 3 4 Shank Clamp and Sweep Assembly...
Page 26: ...3 8 Figure 3 5 Hydraulic Lift Assembly...
Page 28: ...3 10 Figure 3 6 Hydraulic Fold Assembly...
Page 30: ...3 12 Figure 3 7 Disc Gang and Spray Shield Installation...
Page 32: ...3 14 Figure 3 8 Reel Assembly Installation...
Page 34: ...3 16 Figure 3 9 Harrow Assembly Installation...
Page 36: ...3 18 Figure 3 10 Pull Hitch Installation...
Page 38: ...3 20 Figure 3 11 Electrical Installation...
Page 40: ...3 22 Figure 3 12 Decal Installation...
Page 42: ...NOTES 3 24...
Page 53: ...NOTES 4 11...
Page 54: ......
Page 58: ...NOTES 5 4...