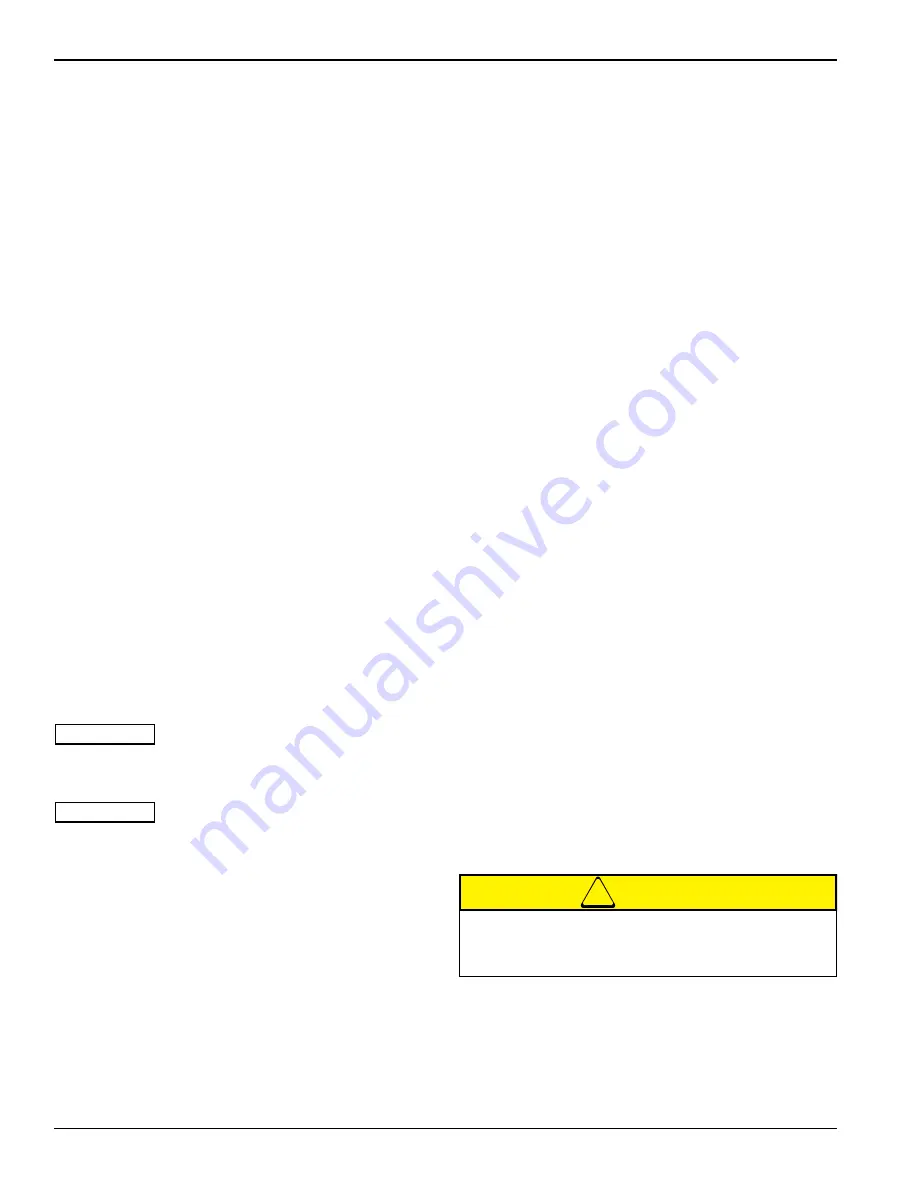
4-6
F-143-0211 Edition
OPERATION AND MAINTENANCE
5.
Set the unit working depth (1 - 5 inches) by adjusting
the stroke control on the master cylinder. For stability,
it is important that the gauge wheels always apply
slight pressure against the soil.
6.
Select proper speed (from 5 - 8 miles per hour) for
best results.
7.
Always lift the Tilloll completely out of the ground
before turning or backing. This prevents shank, disc,
or harrow damage or damage to their respective
mounting brackets.
8.
It is important to keep all bolts tight at all times,
especially during the first few hours of operation. Be
sure to check the shank U-bolts and pivot bolts.
Tighten wheel lug bolts to 90 ft-lbs of torque. After
break-in period, check them periodically. Loose bolts
can result in lost, broken, or prematurely worn parts
and unnecessary down time. Refer to torque
specifications in
when
retightening loose bolts.
9.
Reduce speed at field ends, and lift the Tilloll
completely out of the ground before turning.
10. When operating in the field, run the implement with a
minimum overlap of one foot to insure an even mixing
and leveling of the soil.
Disc Gang Scraper Adjustment
1.
To adjust the pressure of the disc gang scrapers,
loosen the U-bolts that hold the scraper assembly in
place. Slide the scraper assembly toward the disc
blades until there is enough pressure on the scrapers
to clean the discs.
IMPORTANT
The scraper blades are reversible to allow extended
use before replacement is required.
IMPORTANT
The straight coulter at the end of each disc gang is to
control the flow of soil out of the side of the machine.
Spray Shield Adjustment
1.
The spray shields directly behind the disc gang have
two uses and can be adjusted accordingly.
a.
The spray shield controls the flow of soil so an
even spray pattern for herbicide can be
maintained directly behind the spray shield.
b.
The spray shield controls the movement of soil
by the discs. The discs are used primarily to cut
residue and level the ground for good spray
application.
2.
The spray shields should be run at ground level to
level the soil.
3.
The shields should also be set at an angle to carry
some soil back to the center of the machine as it
levels the soil. Set the spray shield up if the machine
is to operate deeper or there is excessive trash.
4.
Set the spray shield down if the machine is to operate
at a shallower depth, or when there is a minimum
amount of trash.
5.
Adjust spray shields outward on machine if too much
dirt is moving around the outer edge and leaving a
ridge. This will move dirt toward center and level the
soil.
Spray Boom Location
The spray boom for herbicide incorporation should be set
directly behind the spray shield when working in ridged
field conditions. It can also be set in front of the machine
in level field conditions.
Reel Adjustment
1.
The reel is preset at the factory at the correct angle.
This angle is set to move worked soil back to the
center of the implement. The angle also determines
the incorporation ability of the reel
2.
Check lock collars on reel bearings during the first
hour of use. Retighten, if necessary, as described in
step 4 on page 3-19.
CAUTION
When working with the reels, use care because
they rotate freely and can catch an arm, hand, or
foot and can cause severe injury.
Summary of Contents for 876-30
Page 2: ......
Page 16: ...2 10 F 143 0211 Edition STANDARD SPECIFICATIONS...
Page 18: ...3 2 F 143 0211 Edition ASSEMBLY INSTRUCTIONS Figure 3 1 Frame Assembly...
Page 19: ...ASSEMBLY INSTRUCTIONS 3 3 Figure 3 2 Wing Assembly 876 30 876 35 Models...
Page 22: ...3 6 F 143 0211 Edition ASSEMBLY INSTRUCTIONS Figure 3 4 Shank Clamp and Sweep Assembly...
Page 26: ...3 10 F 143 0211 Edition ASSEMBLY INSTRUCTIONS Figure 3 7 Hydraulic Lift Assembly 876 40 H...
Page 28: ...3 12 F 143 0211 Edition ASSEMBLY INSTRUCTIONS Figure 3 8 Hydraulic Fold Assembly...
Page 32: ...3 16 F 143 0211 Edition ASSEMBLY INSTRUCTIONS Figure 3 10 Center Reel Assembly Installation...
Page 33: ...ASSEMBLY INSTRUCTIONS 3 17 Figure 3 11 Outer Reel Assembly Installation...
Page 36: ...3 20 F 143 0211 Edition ASSEMBLY INSTRUCTIONS Figure 3 12 Harrow Assembly Installation...
Page 38: ...3 22 F 143 0211 Edition ASSEMBLY INSTRUCTIONS Figure 3 13 Pull Hitch Installation...
Page 40: ...3 24 F 143 0211 Edition ASSEMBLY INSTRUCTIONS Figure 3 14 Electrical Installation...
Page 42: ...3 26 F 143 0211 Edition ASSEMBLY INSTRUCTIONS Figure 3 15 Decal Installation...
Page 44: ...3 28 F 143 0211 Edition ASSEMBLY INSTRUCTIONS Notes...
Page 54: ...4 10 F 143 0211 Edition OPERATION AND MAINTENANCE Notes...
Page 58: ...5 4 F 143 0211 Edition TROUBLESHOOTING GUIDE Notes...
Page 59: ......