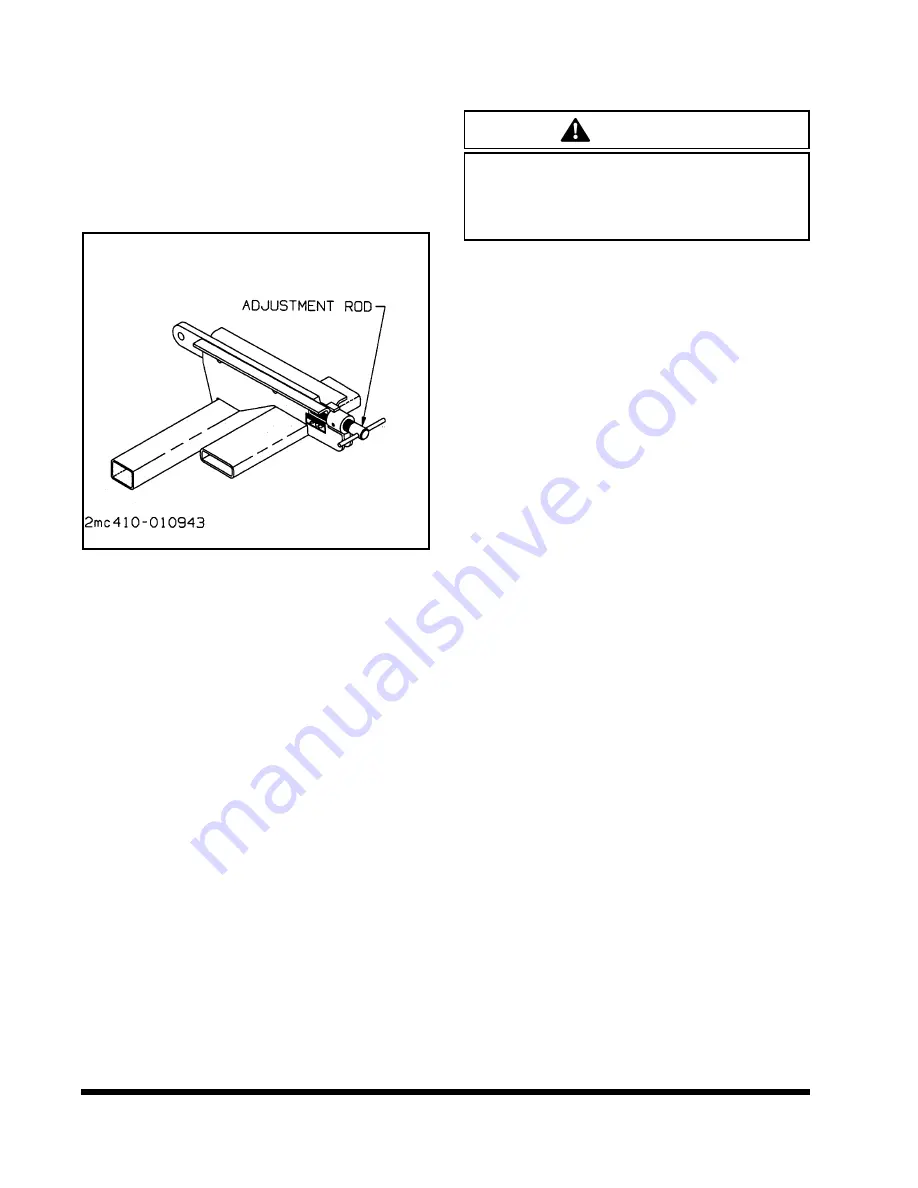
4-4.4
Set the unit working depth.
a.
To adjust the depth, lower unit to the ground
and completely retract the lift cylinders.
b.
Screw the adjustment rod in to decrease the
working depth, out to increase the working
depth.
(See Figure 4-3).
CAUTION
THE TWO ADJUSTMENT RODS ON
THE MAIN FRAME MUST BE AD-
JUSTED EQUALLY OR PERMANENT
EQUIPMENT DAMAGE WILL RESULT.
IMPORTANT
IT MAY BE NECESSARY TO ADJUST THE
WINGS DIFFERENT THAN THE MAIN FRAME
FOR THE UNIT TO OPERATE LEVEL.
4-4.5
Always lift the Finisholl completely out
of the ground before turning or backing. This
prevents shank or disc damage or damage
to their respective mounting brackets.
4-4.6
Reduce speed at field ends, and lift the
Finisholl completely out of the ground before
turning.
4-4.7
After a few hours of operation, check all
bolts for tightness, especially the shank U-
bolts and pivot bolts. Tighten wheel lug bolts
to 90 ft-lbs of torque. Tighten any loose bolts
to the torques shown in
4-4
Figure 4-3 Adjusting Unit Working Depth
Summary of Contents for 850 FINISHOLL
Page 3: ...MODEL 850 FINISHOLL OPERATOR S MANUAL PURCHASED FROM DATE ADDRESS PHONE NO SERIAL NO...
Page 4: ...i...
Page 8: ......
Page 12: ...2 4 Figure 2 1 850 11 Shank Placement Assembly...
Page 13: ...2 5 Figure 2 2 850 14 Shank Placement Assembly...
Page 14: ...2 6 Figure 2 3 850 16 8 Shank Placement Assembly...
Page 15: ...2 7 Figure 2 4 850 16 8 Shank Placement Assembly...
Page 16: ...2 8 Figure 2 5 850 19 4 Shank Placement Assembly...
Page 17: ...2 9 Figure 2 6 850 19 4 Shank Placement Assembly...
Page 18: ...2 10 Figure 2 7 850 22 Shank Placement Assembly...
Page 19: ...2 11 Figure 2 8 850 22 Shank Placement Assembly...
Page 20: ...2 12 Figure 2 9 850 24 8 Shank Placement Assembly...
Page 21: ...2 13 Figure 2 10 850 24 8 Shank Placement Assembly...
Page 22: ...2 14 Figure 2 11 850 27 4 Shank Placement Assembly...
Page 23: ...2 15 Figure 2 12 850 27 4 Shank Placement Assembly...
Page 24: ...2 16 Figure 2 13 850 30 Shank Placement Assembly...
Page 25: ...2 17 Figure 2 14 850 30 Shank Placement Assembly...
Page 26: ...2 18 Figure 2 15 850 33 N Shank Placement Assembly...
Page 27: ...2 19 Figure 2 16 850 33 N Shank Placement Assembly...
Page 28: ...2 20 Figure 2 17 850 33 Shank Placement Assembly...
Page 29: ...2 21 Figure 2 18 850 33 Shank Placement Assembly...
Page 30: ...2 22 Figure 2 19 850 35 Shank Placement Assembly...
Page 31: ...2 23 Figure 2 20 850 35 Shank Placement Assembly...
Page 32: ...NOTES 2 24...
Page 34: ...3 2 Figure 3 1 Frame Assembly 30 to 35...
Page 36: ...3 4 Figure 3 2 Rockshaft Installation Frame Figure 3 3 Rockshaft Installation Frame 30 and 35...
Page 38: ...3 6 Figure 3 5 Wing and Wing Extensions 17 35 Models...
Page 41: ...3 9 Figure 3 9 Fold Cylinder Bracket 17 through 27...
Page 42: ...3 10 Figure 3 10 Fold Cylinder Bracket 30 and Larger...
Page 43: ...3 11 Figure 3 11 Installation of Fittings in Manifold...
Page 44: ...3 12 Figure 3 12 Installation of Shanks and Clamps...
Page 46: ...3 14 Figure 3 14 Spring Shank Assembly Figure 3 15 Ratchet Jack Installation...
Page 47: ...3 15 Figure 3 16 Disc Gang Hydraulic Assembly...
Page 50: ...3 18 Figure 3 19 Leveling Assembly Installation...
Page 52: ...3 20 Figure 3 20 Warning Light Installation...
Page 54: ...3 22 Figure 3 21 Hydraulic Radius Rod...
Page 55: ...3 23 Figure 3 22 Rear Hitch Assembly Option...
Page 58: ...NOTES 3 26...
Page 65: ...4 7 Figure 4 6 Spike Harrow 3 and 5 Bar Figure 4 7 Spike Harrow Tilloll Style...
Page 68: ...4 10 Figure 4 11 Lubrication Schedule...
Page 70: ...NOTES 4 12...
Page 73: ...NOTES 5 3...
Page 74: ......