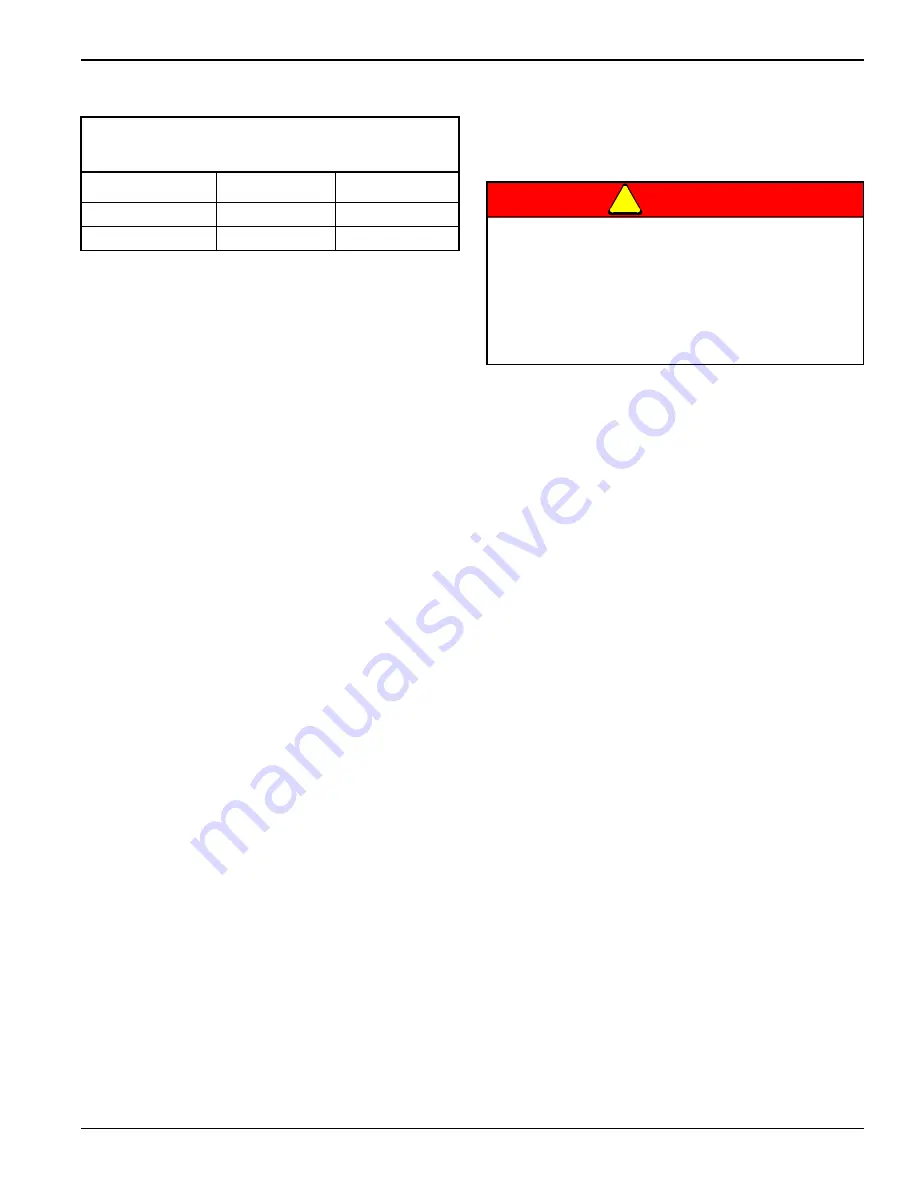
MAINTENANCE AND LUBRICATION
4-7
4.
Lower the trailer by exhausting air from the air
springs by moving the control arm to the “down”
position (about 45°) until the axle tube is resting on
the block.
5.
Check the ride height to make sure it is correct.
Consult Landoll Service Center if correct height
cannot be obtained.
6.
Loosen the 1/4” adjusting lock nut located on the
adjusting block, allowing the control arm to move
approximately 1 inch. Move the adjusting block until
holes align, then insert locating pin
7.
Align the control arm linkage to the control arm lower
bracket and re-tighten the 1/4" adjusting lock nut to
2-4 ft.lbs. The ride height valve should now be
correctly adjusted.
8.
Remove the locating pin.
9.
The block can now be removed by using the height
control valve as an improvised jack by disconnecting
the control arm at the lower bracket and pushing the
control arm to an “up” position.
10. Remove the block and reconnect the linkage. This
allows the Automatic Height Control Valve to resume
normal operation.
11. Check the air ride height. If necessary, go through
the adjustment procedure again until the proper air
ride height is achieved.
12. Check the air ride height periodically and adjust as
needed.
Alignment
Wheel Alignment
DANGER
When trailer tires show signs of scuffing, feather-edging
or uneven wear, examine the trailer for damaged
suspension (frame, shocks, linkage, etc.), axle, wheel
bearings and wheels. Proper wheel alignment and wheel
bearing adjustment is essential for proper tire wear. The
simplest form of checking wheel alignment “toe” is by
running the trailer over a “SCUFF GAUGE”. A scuff
gauge reading of 16 feet or less per mile is considered
satisfactory. If a scuff gauge is not readily available, or
edge wear on one side of a tire is occurring signifying
positive or negative camber, alignment can be checked
as follows:
1.
Remove wheel, hub and bearing assemblies.
2.
Place a 3-point axle gauge against the front side of
the axle, and adjust each axle gauge point to the
axle. (Double point end against the inner and outer
wheel bearing surfaces of the spindle being checked
and the other point on the inner bearing surface on
the other spindle.)
3.
Move the axle gauge and place against the back side
of the axle. If either of the points of double point end
fails to touch the axle surface, a bent spindle is
evident. A point gap of .015" or more is considered
excessive tire “toe” and the axle must be replaced
4.
Follow the same procedures as in
except place the axle gauge above and below the
axle. If gauge point gap is found, the axle has
positive or negative camber. The trailer axle has no
camber from the factory. If it is found to have positive
or negative camber, axle replacement is necessary
(See Figure 4-3
for examples of camber).
AIR SUSPENSION
RIDE HEIGHT AND BLOCK
Brake Size
Ride Height
Block Height
12-1/4” Dia.
3.5”
5”
16-1/2” Dia.
5.5”
7”
To prevent a life threatening accident:
1.
Support trailer and undercarriage so tires are
off the ground.
2.
Support the trailer and undercarriage on jack
stands with sufficient capacity to support the
total weight of the trailer and any load which
it may be carrying.
Summary of Contents for 345F
Page 2: ......
Page 6: ......
Page 22: ...3 10 F 944 1017 Edition OPERATING INSTRUCTIONS Figure 3 4 Steps for Loading and Unloading...
Page 30: ...3 18 F 944 1017 Edition OPERATING INSTRUCTIONS Page Intentionally Blank...
Page 44: ...4 14 F 944 1017 Edition MAINTENANCE AND LUBRICATION Figure 4 8 Axle and Brake Assembly...
Page 61: ......