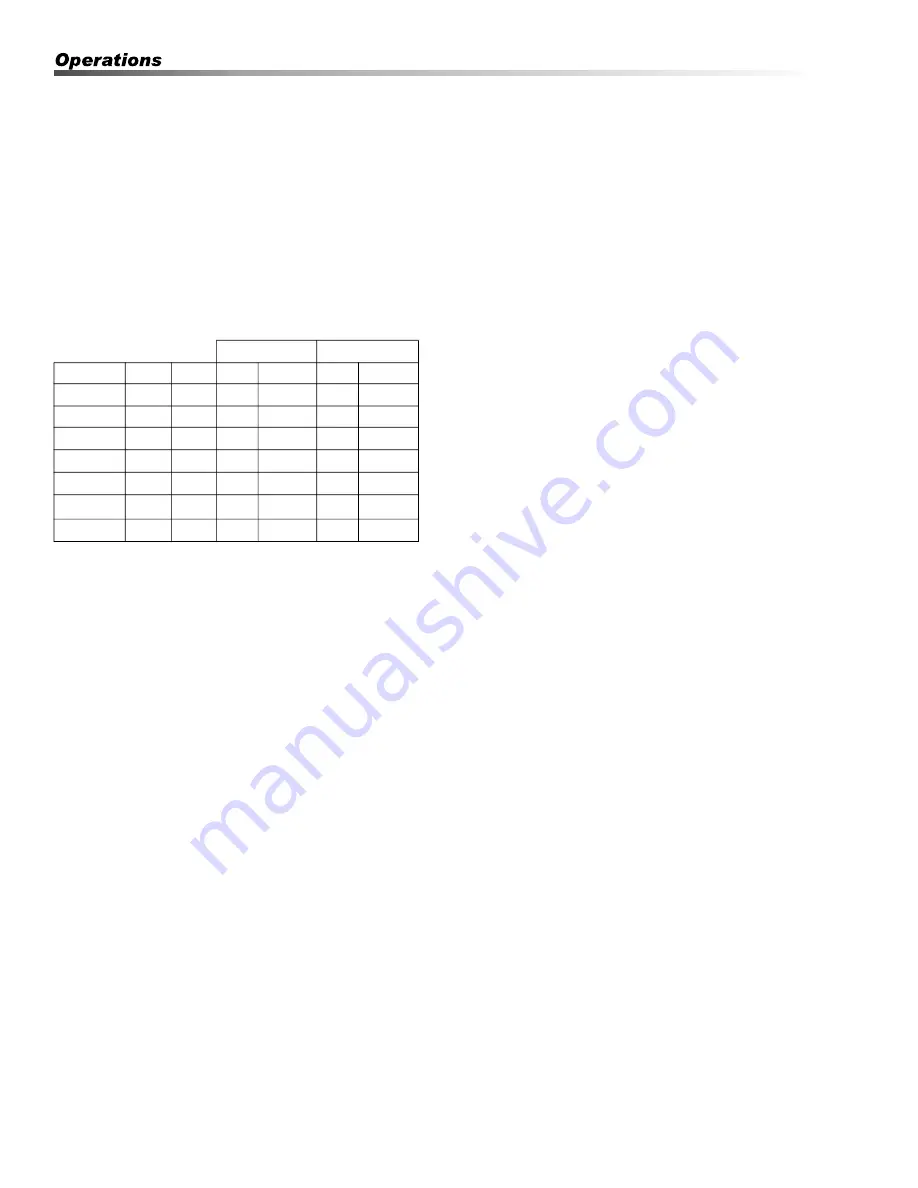
16
For Tech Tip Instructions
Combustion efficiency in a natural draft pressure
washer is significantly influenced by the heat created
inside the coil, the design of the coil and flue and the
length and diameter of the exhaust stack. The table
below shows data included in the operator’s manual for
flue and stack sizes and gas manifold pressure
settings. These sizes are critical for achieving proper
combustion and acceptable emissions.
Testing has shown that simply adding a 36” stack
extension to the flue adapter on top of the pressure
washer can reduce the outlet temperature by 5-10°F.
This occurs by inducing a higher pressure differential at
the exit of the coil and increasing the flow of air into the
combustion process and through the stack. Most or all
of the lost outlet temperature can be recovered by
installing and adjusting a damper in the stack. However
this adjustment must only be performed by a trained
technician using a combustion analyzer.
The damper should be installed 24-36” above the flue
adapter. The pressure washer can be operated safely
with the damper fully open but with the lower outlet
temperature. If the damper is closed too far there will
not be enough oxygen to burn all of the fuel. This will
cause higher and potentially dangerous levels of CO in
the flue gas emissions.
To adjust the damper for proper combustion and effi-
ciency perform the following:
1. If there is no sample port for the analyzer probe,
drill a hole slightly larger than the combustion
analyzer probe through the exhaust stack at a point
about 18” above the flue adapter.
2. Insert the probe of the combustion analyzer so that
the tip is at the center of the stack.
3. Open the damper to the fully open position.
4. Start the pressure washer and allow it to heat up
for at least 20 minutes before making any adjust-
ments.
5. Note the values for % Excess Air and/or %
Oxygen.
6. Close the damper in small increments until %
Excess Air is between 20-30% and/or % Oxygen is
4-5%.
This process can also be used when turning down the
firing rate for high altitude installations above 2000 ft.
1. Adjust the gas pressure down 4% for every 1000 ft
of elevation.
Example: Recommended firing rate for a 4.8@3000
is 4.2 wc-in. For an installation at 3500 feet reduce
this pressure by 16% by setting the manifold pressure
to 4.2*.84 = 3.5 wc-in.
A manometer capable of reading to at least the nearest
0.1 wc-in will be required for this adjustment. These can
be found for less than $200 (Extech HD700).
2. Follow steps 1-6 above to optimize the outlet
temperature of the pressure washer.
Installations Above 2000 ft:
Installation at altitudes greater than 2000 ft will require
adjustments to the gas manifold pressure.
For installations above 2000 feet the firing rate should
be reduced by 4% per 1000 feet. Example: Recom-
mended firing rate for a 4.8@3000 is 4.2 wc-in. For an
installation at 3500 feet reduce this pressure by 16% by
setting the manifold pressure to 4.2*.84 = 3.5 wc-in.
This adjustment should only be made by a properly
trained service technician. A manometer capable of
reading to the nearest 0.1 wc-in will be required for this
adjustment.
In Canada, certification for installation at altitudes over
4500 feet is the jurisdiction of local authorities.
NG
LP
Model
Collar Stack wc-in kBTU-in wc-in kBTU-in
3.5@2000
10"
8"
3.6
310
7.8
310
4.0@3000
10"
8"
3.4
354
7.4
354
4.0@2200
10"
8"
5.1
364
11.2
364
5.0@3000
10"
10"
4.2
415
9.1
415
5.0@2300
10"
10"
4.7
437
9.5
439
6.0@3800
12"
10"
4.3
507
7.4
507
8.0@3800
12"
12"
3.1
658
7.0
658
Landa VHG Operator’s Manual 8.913-952.0 - BR