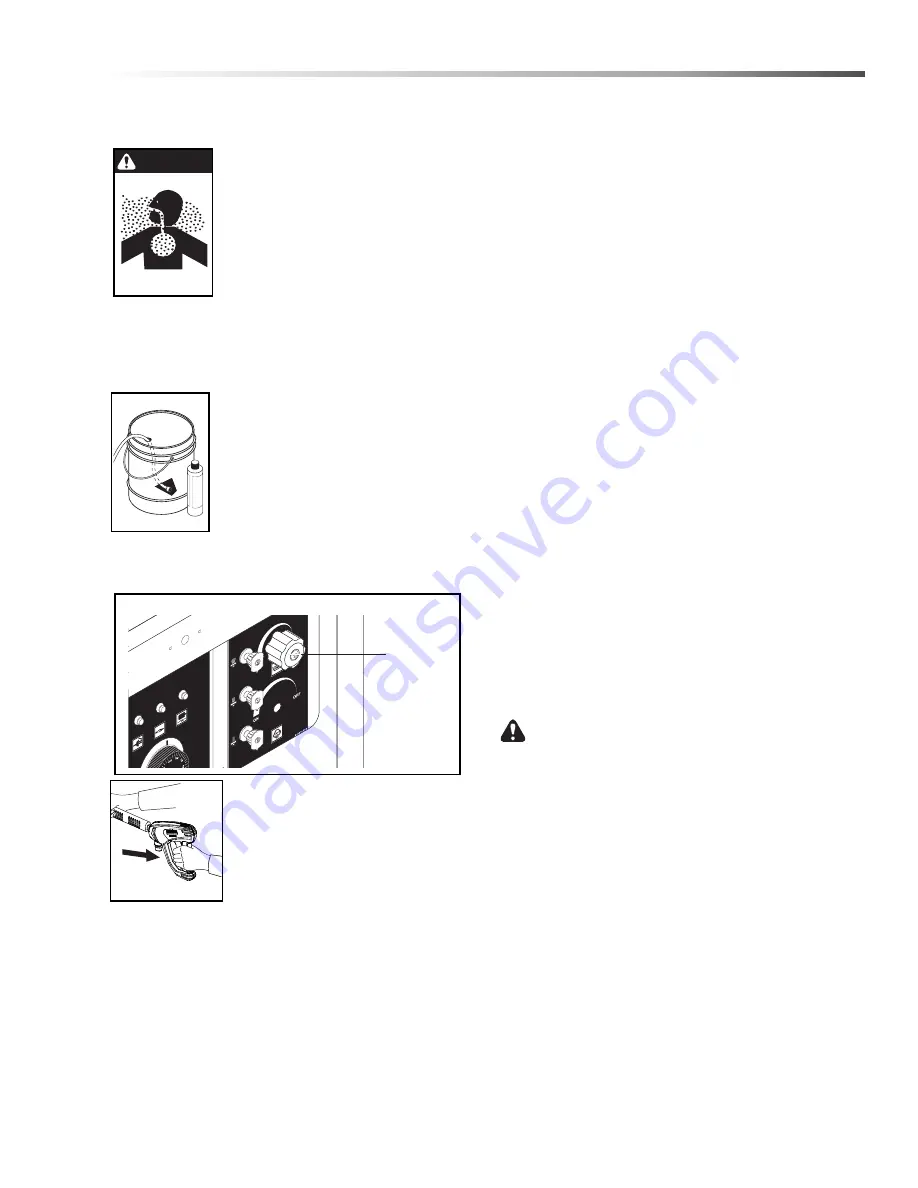
23
Operations
Applying Detergent &
General Operating Techniques
WARNING: Some detergents may be
harmful if inhaled or ingested,
causing severe nausea, fainting or
poisoning. The harmful elements
may cause property damage or
severe injury.
AVERTISSEMENT: Certains déter-
gents peuvent être dangereux s'ils
sont inhalés ou ingérés, provoquant
de fortes nausées, des évanouissements et l'empoi-
sonnement. Les éléments dangereux peuvent causer
des dommages à la propriété ou des blessures
graves.
STEP 1:
Use detergent designed specif-
ically for pressure washers. Household
detergents could damage the pump.
Prepare detergent solution as required
by the manufacturer. Fill a container with
pressure washer detergent. Place the
filter end of detergent suction tube into
the detergent container.
STEP 2:
Open detergent valve counter-
clockwise until you obtain desired mixture. Detergent will
mix with the high pressure water stream.
STEP 3:
With the motor running, pull
trigger to operate machine. Liquid
detergent is drawn into the machine
and mixed with water. Apply detergent
to work area. Do not allow detergent to
dry on surface.
IMPORTANT: You must flush the detergent from your
pressure washer after each use by placing the suction
tube into a bucket of clean water, then run the
pressure washer for 2 minutes.
NOTE: If you remove detergent siphon tube from
container or allow container to empty, it will cause low
pressure by sucking air, which will damage the pump
.
Thermal Pump Protection
If you run the engine for 3-5 minutes without pressing the
trigger on the spray gun, circulating water in the pump can
reach high temperatures. When the water reaches this
temperature, the pump protector engages and cools the
pump by discharging the warm water onto the ground.
This thermal device prevents internal damage to the
pump.
Cleaning Tips
Pre-rinse cleaning surface with fresh water. Place
detergent suction tube directly into cleaning solution and
apply to surface. For best results, limit your work area to
sections approximately 6 feet square and always apply
detergent from bottom to top. Allow detergent to remain on
surface 1-3 minutes. Do not allow detergent to dry on
surface. If surface appears to be drying, simply wet down
surface with fresh water. If needed, use brush to remove
stubborn dirt. Rinse at high pressure from top to bottom in
an even sweeping motion keeping the spray nozzle
approximately 1 foot from cleaning surface. Use overlap-
ping strokes as you clean and rinse any surface. For best
surface cleaning action spray at a slight angle.
Recommendations
:
•
Before cleaning any surface, an inconspicuous
area should be cleaned to test spray pattern and
distance for maximum cleaning results.
•
If painted surfaces are peeling or chipping, use
extreme caution as pressure washer may remove
the loose paint from the surface.
•
Keep the spray nozzle a safe distance from the
surface you plan to clean. High pressure wash a
small area, then check the surface for damage. If
no damage is found, continue to pressure
washing.
CAUTION - Never use:
•
Bleach, chlorine products and other corrosive
chemicals
•
Liquids containing solvents (i.e., paint thinner,
gasoline, oils)
•
Tri-sodium phosphate products
•
Ammonia products or acid-based products
ATTENTION: Ne jamais utiliser :
•
Eau de Javel, produits à base de chlore et autres
produits chimiques corrosifs
•
Liquides contenant des solvants (c.-à-d. diluant à
peinture, essence, huiles, etc.)
•
Produits à base de tripolyphosphate de sodium
•
Ammoniac ou produits à base d'acide
These chemicals will harm the machine and will damage
the surface being cleaned.
Rinsing
Turn detergent valve clockwise to close. Operate pressure
washer and allow a few seconds for the detergent to clear.
Landa ENG Operator’s 9.801-511.0 - F
WARNING
Detergent
Valve
Summary of Contents for ENG Series
Page 36: ...9 801 511 0 Printed in U S A...