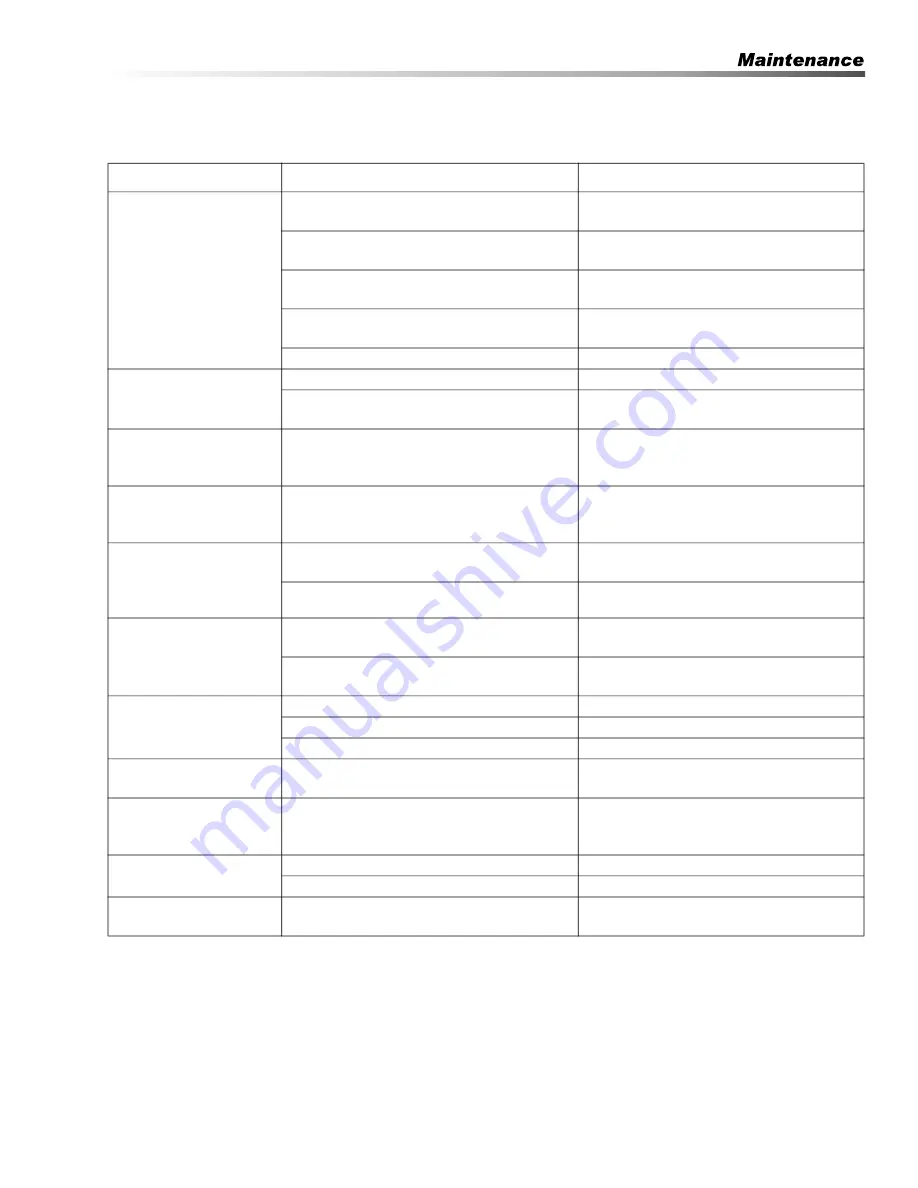
33
PROBLEM
POSSIBLE CAUSE
REPAIR
WASHER FAILS TO
DRAW DETERGENT
Detergent metering valve closed
or valve clogged or defective
Open detergent metering valve, following
procedure in operating instructions.
Back pressure in hose (when using
additional lengths of pressure hose)
Contact dealer for proper injector
size when adding lengths of hose.
Back pressure in pressure hose (when
using dual lance wand)
Use proper size flood nozzle in dual lance
wand (refer to parts breakdown).
Suction tube not below liquid surface
Completely submerge suction tube and
strainer in detergent solution.
Clogged or damaged suction strainer
Clean or replace strainer.
DETERGENT
SOLUTION
TOO WEAK
Clogged detergent strainer
Clean or replace strainer.
Air leak in detergent suction tube or inlet
plumbing
Find air leak and clean or
replace parts as necessary.
DETERGENT
SOLUTION TOO
CONCENTRATED
Original detergent too concentrated
Dilute product as necessary to achieve
proper concentration.
DETERGENT IN
RINSE CYCLE
Dual lance wand or adjustable nozzle
holder in open position or chemical
metering valve open
Close dual lance wand adjustable lance
holder to achieve high pressure. Close
detergent metering valve.
DILUTION OF
DETERGENT
CONCENTRATE
DURING CYCLE
Worn or defective internal check valve
Repair or replace check valve or
injector parts as necessary.
Defective check valve in detergent tank
Replace parts as necessary.
NOISY OPERATION
Worn bearings
Replace bearings, refill crankcase oil with
recommended lubricant.
Cavitation
Check inlet lines for restrictions
and/or proper sizing.
PUMP NOISY
Low oil level
Add oil
Worn or dirty valves
Replace or clean.
Bad bearings
Inspect bearings; replace as required
IRREGULAR
SPRAY PATTERN
Worn or partially clogged nozzle
Clean or replace nozzles.
EXCESSIVE WEAR
Worn or loose bearings
Replace bearings. Check bearing seals,
spacers and retainers. Replace any worn
parts.
HIGH CRANKCASE
TEMPERATURE
Wrong grade of oil
USE SAE 90 Gear Oil.
Improper amount of oil in crankcase
Adjust oil level to proper amount.
OIL LEAKS
Worn pistons and/or leaking crank seals,
crankcase cover seal or drain plugs
Replace seals, sleeves or O-Rings.
Landa ECOS 7000 Operator’s Manual 9.801-316.0 - G