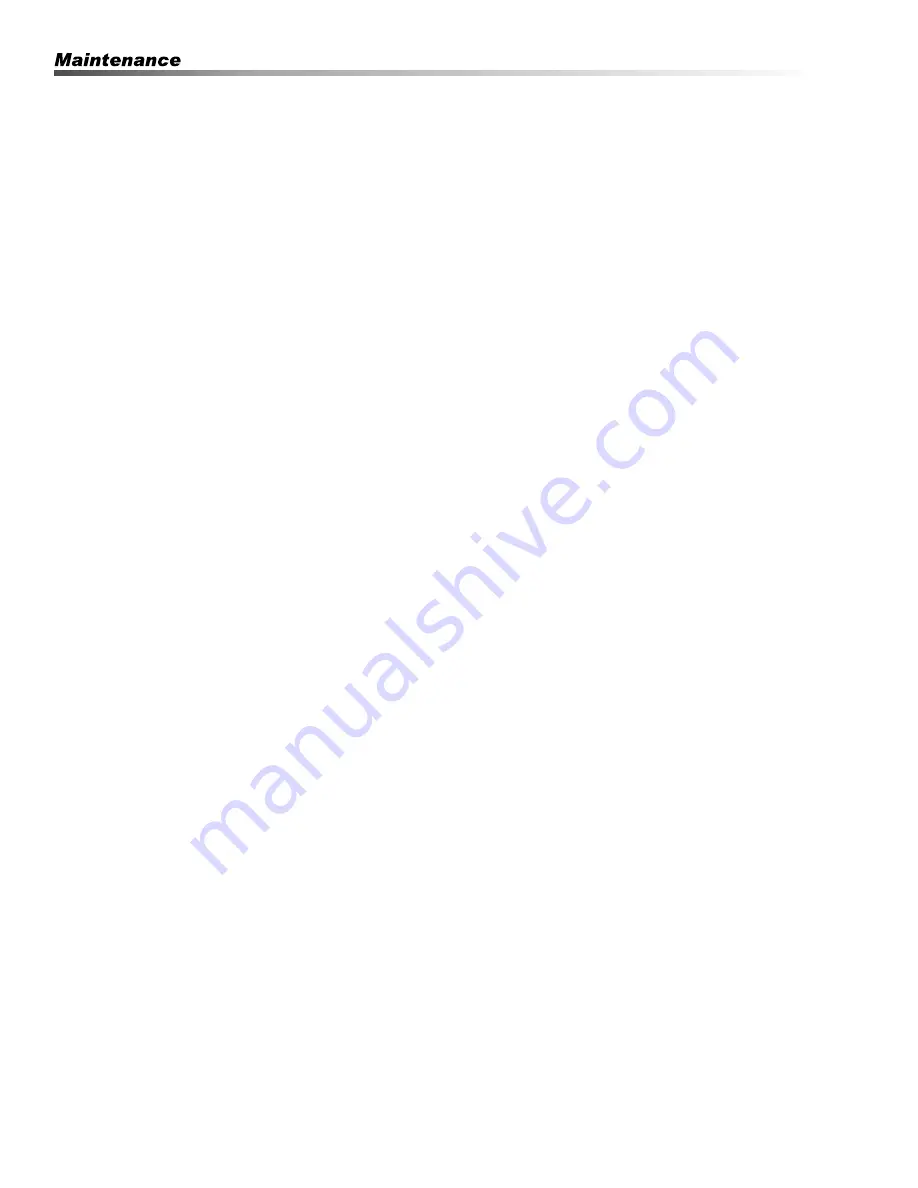
30
Removal of Soot and Heating Coil
In the heating process, fuel residue in the form of soot
deposits may develop on the heating coil pipe and
block air fl ow which will affect burner combustion.
When soot has been detected on visual observation,
the soot on the coil must be washed off after following
the coil removal steps (See Coil Removal).
Pressure Relief Valve
Each machine is equipped with a relief valve to relieve
pres sure in the system when higher than normal
operating pressures are encountered or if the unloader
valve should fail. Unusually high pressures come from
an object plugging the spray nozzle. If operating pres
sure is found to be normal and the relief valve
continues to leak, re pair or re place valve.
CAUTION:
This valve must be opened each year to check
operation
.
Rupture Disk
If pressure from pump or thermal expansion should
exceed safe limits, the rupture disk will burst allowing
high pressure to be discharged through hose to ground.
When disk ruptures it will need to be replaced.
The Rupture Disk should be replaced every two years.
Fuel
Use clean fuel oil/diesel that is not contaminated with
water and debris. Replace fuel filter and drain tank
every 100 hours of operation. Use No. 1 or No. 2
heating oil (ASTM D306) only.
NEV ER
use gas o line in
your burner fuel tank. Gasoline is more combustible
than fuel oil and could result in a serious explosion.
NEV ER
use crank case or waste oil in your burner.
Fuel unit malfunction could result from contamination.
Fuel Control System
This machine utilizes a fuel solenoid valve located on
the fuel pump to control the fl ow of fuel to the combus-
tion chamber. The solenoid, which is normally closed, is
ac ti vat ed by a fl ow switch when water flows through
it. When the operator releases the trigger on the spray
gun, the fl ow of water through the fl ow switch stops,
turning off the electrical current to the fuel solenoid. The
solenoid then closes, shutting off the supply of fuel to
the combustion chamber. Controlling the fl ow of fuel in
this way gives an instantaneous burn-or-no-burn situa-
tion, there by eliminating high and low water tempera-
tures, and combustion smoke normally associated with
machines incorporating a spray gun.
CAUTION:
Periodic inspection, to insure that the fuel
solenoid valve functions properly, is rec om mend ed.
This can be done by operating the ma chine and
checking to see that the burner is not firing when the
spray gun is in the off position.
Fuel Pressure Adjustment
To adjust fuel pressure, First install a pressure gage
into the port just after the pump fuel exit. Turn the
adjusting screw (located at the regulator port)
clockwise to increase, and counterclockwise to
decrease. Do not exceed 200 psi or lower the pressure
below 130 PSI, when checked at the post-pump
pressure port.
The fuel pressure may need to be adjusted due to
altitude. For every 500 ft altitude above sea level, the
boiling point of water goes down 1 °F. At high altitude
environments, this boiling point change may require the
heat input to be lowered so the water input does not
turn to steam earlier than at the factory settings and
activate the pressure sensors and pressure relief
equipment when the unit is operated and much higher
altitudes from factory settings or local dealer site
settings. Check with your dealer before making local
site fuel pressure adjustments.
Also, as ambient temperature changes seasonally, the
fuel temperature in the feed tank and air temperature
inlet can impact fuel flow. In more extreme tempera-
tures, this local-site adjustment may also require
different fuel nozzles for fuel inlet temperatures that are
at seasonal extremes (higher or lower) in locations
where the temperature changes are beyond moderate
temperatures of between 40°F and 90°F. Colder
temperatures will make for a thicker flow and less fine a
fuel spray while hotter temperatures will make for a
thinner flow a more fine spray with the same nozzle.
Consider alternate nozzle configurations from the
baseline factory-supplied nozzle for operating in such
temperature extremes if performance is not meeting
needs with air band and fuel pressure settings alone.
NOTE: When changing fuel pump, a by-pass plug
must be installed in return line port or fuel pump will
not prime.
Burner Nozzle
Keep the tip free of surface deposits by wiping it with a
clean, solvent saturated cloth, being careful not to plug
or enlarge the nozzle. For maximum efficiency, replace
the nozzle each season.
Landa ECOS 7000 Operator’s Manual 9.801-316.0 - G