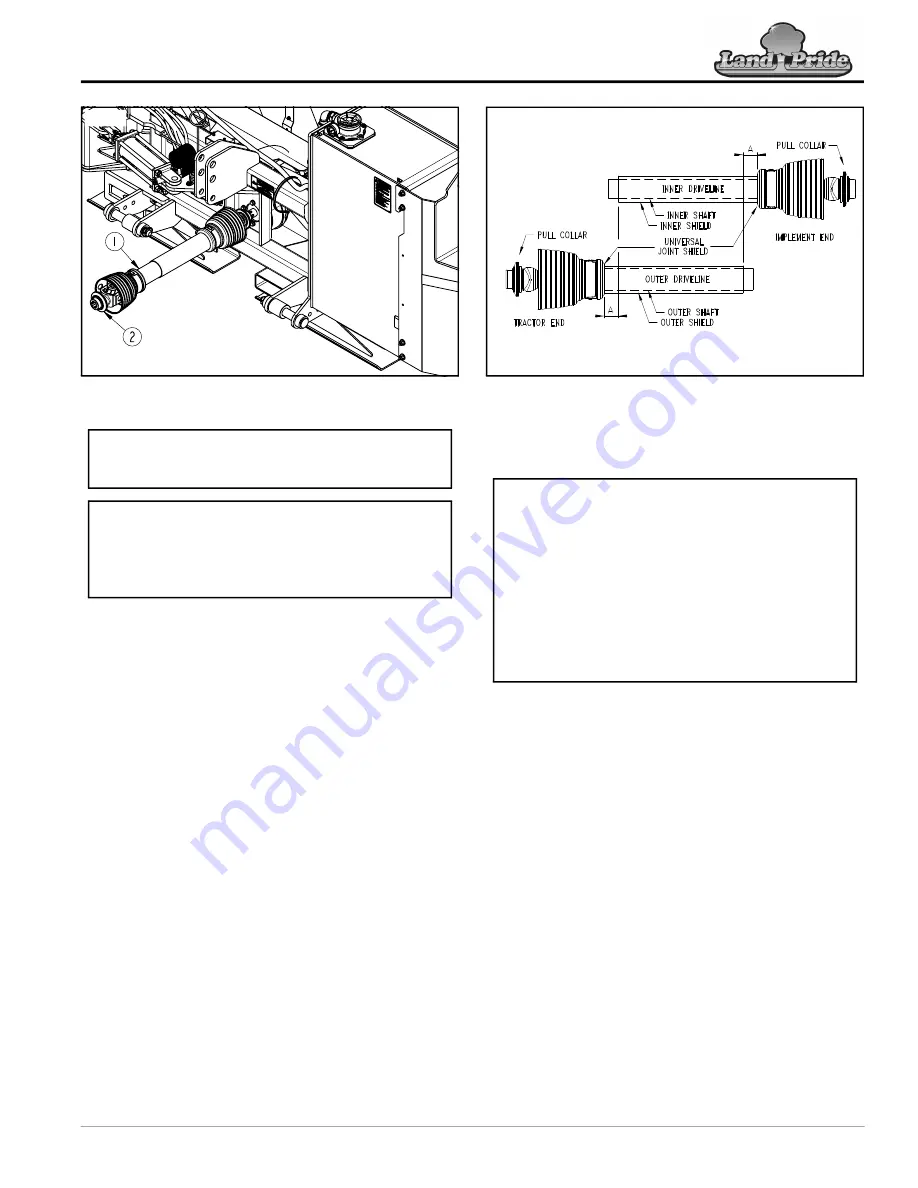
Section 1: Assembly & Set-up
3/12/21
RCP(M)2760 & RCP(M)3760 Parallel Arm Rotary Cutter 316-548M
21
Driveline Hook-up
Figure 1-6
1. If driveline minimum length has not been checked, go
to
“Driveline Minimum Operating Length”
page. Otherwise, continue with step 2 below.
2. Park tractor and Rotary Cutter on a level surface.
3. Shut tractor down before dismounting. Refer to
4. If tractor drawbar interferes with the driveline during
hook-up, move drawbar forward, to the side, or
remove.
5. Collapse driveline (#1) by pushing tractor end of
driveline toward the Rotary Cutter’s gearbox.
6. Pull back on the driveline pull collar (#2) and push
yoke onto the tractor power take-off shaft. Release
pull collar and continue to push driveline yoke
forward until pull collar pops out and locks in place.
7.
Pull on driveline ends to make sure they are secured
to the tractor and Rotary Cutter.
“Install Stabilizer Turnbuckles”
74474
IMPORTANT:
An additional driveline may be
required if implement is attached to more than one
tractor or if a Quick Hitch is used.
IMPORTANT:
Check driveline minimum length
before completing
. Structural
damage to the tractor and reservoir can occur if this
check is not made. Refer to
Check Driveline Minimum Length
Figure 1-7
Driveline Minimum Operating Length
Refer to Figure 1-7:
1. With driveline attached only to the 3-point implement,
remove outer driveline (tractor end) from inner
driveline to separate the two profiles.
2. Park tractor and implement on a level surface.
3. Raise implement until its gearbox input shaft is level
with the tractor’s power take-off shaft.
4. Without changing the 3-point lift height, shut tractor
5. Place support blocks under the mainframe to keep
the gearbox input shaft level with the tractor’s output
shaft.
6. Attach outer driveline to the tractor power take-off
shaft. Refer to steps 6-7 under
7.
Hold inner and outer drivelines parallel to each other.
If dimension “A” is greater than or equal to 1" (2.5 cm),
then skip to
on this page. Otherwise continue with step
30398
IMPORTANT:
A driveline that is too long can bottom
out causing structural damage to the tractor and
implement. Always check driveline minimum length
during initial setup, when connecting to a different
tractor, and when alternating between using a Quick
Hitch and a standard 3-point hitch. More than one
driveline may be required to fit all applications.
The power take-off shaft and gearbox
input shaft must be aligned and level with each other