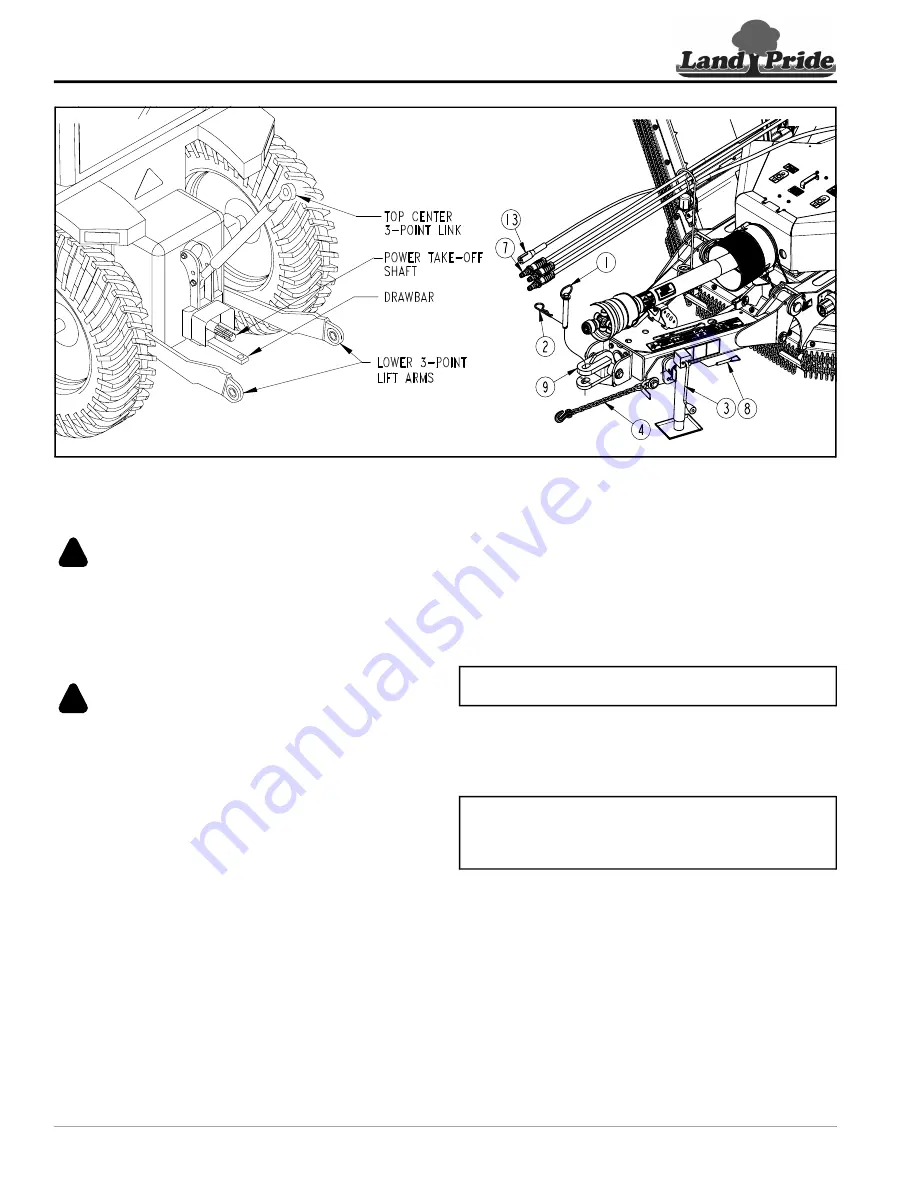
Section 1: Assembly & Set-up
RCB(M)5710 & RCB(M)L5710 Rotary Cutters 337-049M
7/9/20
20
Hook-up Constant Level Clevis Hitch
DANGER
!
To avoid serious injury or death:
A crushing hazard exists while hooking-up and unhooking the
implement. Keep people and animals away while backing-up
to the implement or pulling away from the implement. Do not
operate hydraulic controls while a person or animal is directly
behind the power machine or near the implement.
WARNING
!
To avoid serious injury or death:
The ball detent pin must be fully inserted into the park jack
with ball visible and popped out on the far side of the jack
before working on or around an unhooked cutter.
Refer to Figure 1-10:
1. Make certain park jack (#3) is properly attached to
the cutter hitch and secured with detent pin (#8). If
park jack is not vertical, refer to
2. Store tractor’s top center 3-point link in its storage
hook.
3. Start tractor and raise lower 3-point arms fully up.
4. Carefully back tractor within close proximity of
clevis (#9).
5. Shut tractor down before dismounting according to
6. Verify tractor drawbar is adjusted correctly. Refer to
7.
Raise or lower park jack (#3) to align clevis (#9) with
tractor drawbar. Drawbar should fit between lower
and upper plates of clevis.
8. Restart tractor and continue to back tractor up to the
cutter hitch until hitch holes in tractor drawbar and
clevis (#9) are aligned.
9. Shut tractor down before dismounting according to
10. Attach cutter to tractor drawbar with hitch pin (#1).
Secure hitch pin with hairpin cotter (#2).
11. Lower park jack (#3) until hitch weight is supported
by the tractor drawbar.
12. Remove detent pin (#8) and relocate park jack (#3)
from the hitch mount to the storage mount on the left
side of the cutter. Secure jack with its detent pin.
Make sure the jack base is level with, or lower than
the jack crank head. See cover picture for the correct
mounting positioning.
13. Attach hitch safety chain (#4) to the tractor. Adjust
chain length to remove all slack except what is
necessary to permit turning. Lock chain hook
securely to the safety chain.
NOTE:
Hitch pin (#1) and hairpin cotter (#2) are
supplied by the customer.
IMPORTANT:
Before moving the cutter, relocate the
park jack to its storage mount on the cutter. Make sure
the jack is stored with its base level or lower than the
head to prevent water and freeze damage.
Hook-up Swivel Clevis Hitch
Figure 1-10
37298
74108