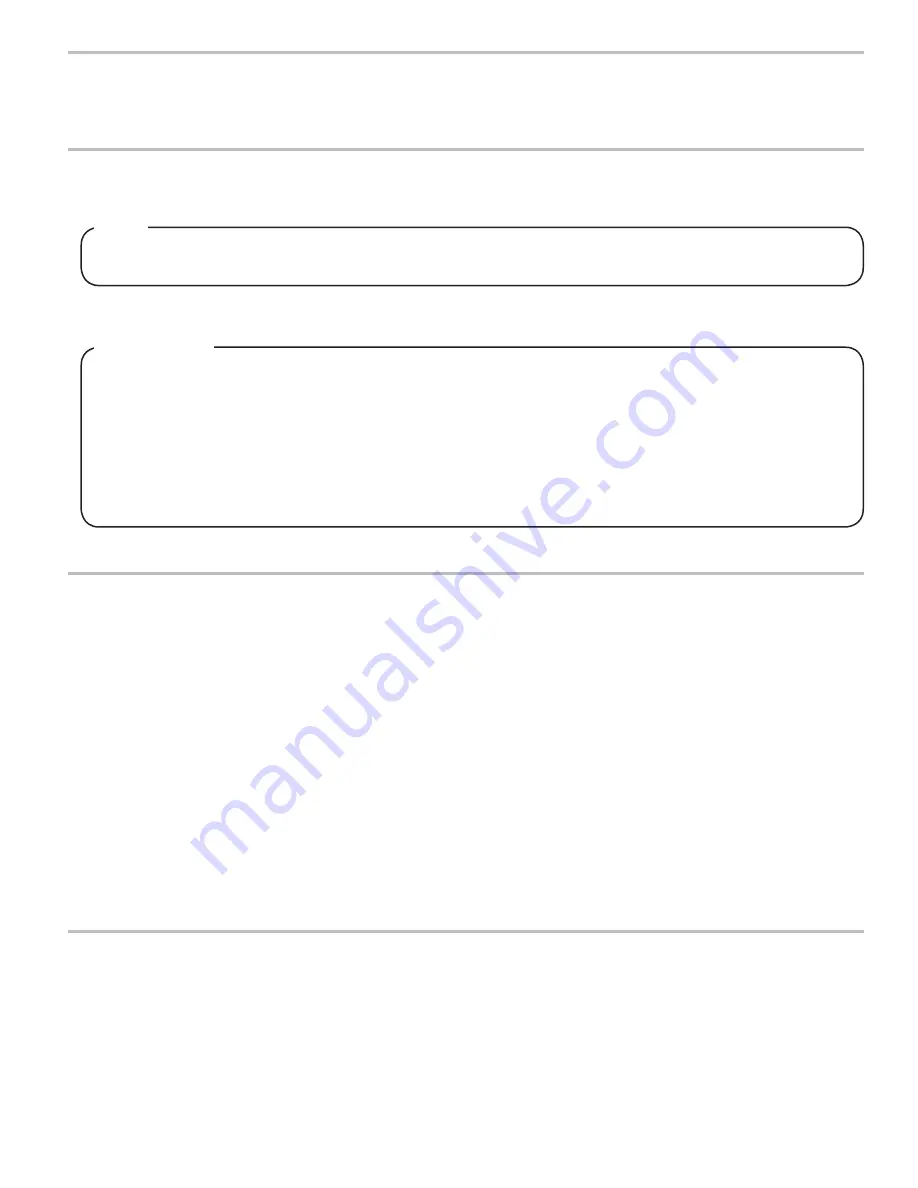
14
General Information
CLEANING AND SANITIZING
•
Lancer equipment (new or reconditioned) is shipped from the factory cleaned and sanitized in accordance with NSF guidelines.
The operator of the equipment must provide continuous maintenance as required by this manual and/or state and local health
department guidelines to ensure proper operation and sanitation requirements are maintained.
The cleaning procedures provided herein pertain to the Lancer equipment identified by this manual. If other
equipment is being cleaned, follow the guidelines established by the manufacturer for that equipment.
NOTE
•
Cleaning should be accomplished only by trained personnel. Sanitary gloves are to be used during cleaning operations.
Applicable safety precautions must be observed. Instruction warnings on the product being used must be followed.
• Use sanitary gloves when cleaning the unit and observe all applicable safety precautions.
• DO NOT
use a water jet to clean or sanitize the unit.
• DO NOT
disconnect water lines when cleaning and sanitizing syrup lines, to avoid contamination.
• DO NOT
use strong bleaches or detergents; These can discolor and corrode various materials.
• DO NOT
use metal scrapers, sharp objects, steel wool, scouring pads, abrasives, or solvents on the dispenser.
• DO NOT
use hot water above 140° F (60° C). This can damage the dispenser.
• DO NOT
spill sanitizing solution on any circuit boards. Insure all sanitizing solution is removed from the system.
!
ATTENTION
Cleaning and Sanitizing Solutions
Daily Cleaning
Cleaning Solution
Mix a mild, non-abrasive detergent (e.g. Sodium Laureth
Sulfate, dish soap) with clean, potable water at a temperature
of 90°F to 110°F (32°C to 43°C). The mixture ratio is one
ounce of cleaner to two gallons of water. Prepare a minimum of
five gallons of cleaning solution. Do not use abrasive cleaners
or solvents because they can cause permanent damage to the
unit. Ensure rinsing is thorough, using clean, potable water at a
temperature of 90°F to 110°F. Extended lengths of product lines
may require additional cleaning solution.
Sanitizing Solution
Prepare the sanitizing solution in accordance with the
manufacturer’s written recommendations and safety guidelines.
The type and concentration of sanitizing agent recommended
in the instructions by the manufacturer shall comply with 40
CFR §180.940. The solution must provide 100 parts per million
(PPM) chlorine (e.g. Sodium Hypochlorite or bleach) and a
minimum of five gallons of sanitizing solution should be
prepared.
Nozzle Sanitizing Solution
Prepare a chlorine solution (less than pH 7.0) containing 50
PPM chlorine with clean, potable water at a temperature of 90
– 110°F. Any sanitizing solution may be used as long as it is
prepared according to manufacturer’s recommendations and
safety guidelines, and provides 50 PPM cholorine.
Other Supplies Needed:
1.
Clean cloth towels
2.
Bucket
3. Extra nozzle
4. Sanitary gloves
5. Small brush (PN 22-0017)
1. Using the cleaning solution, clean Top Cover and all
exterior stainless steel surfaces.
2. Clean exterior of dispensing valves and ice chute.
3.
Remove Cup Rest, clean Drip Tray and Cup Rest, and
replace Cup Rest.
4.
Wipe clean all splash areas using a damp cloth soaked in
cleaning solution.
5. Clean beverage valves as specified by the section “Clean
-
ing and Sanitizing Nozzles” on page 16.
Summary of Contents for Sensation
Page 23: ...23 INTENTIONALLY LEFT BLANK...
Page 26: ...26 Wiring Diagram 115 Volt...