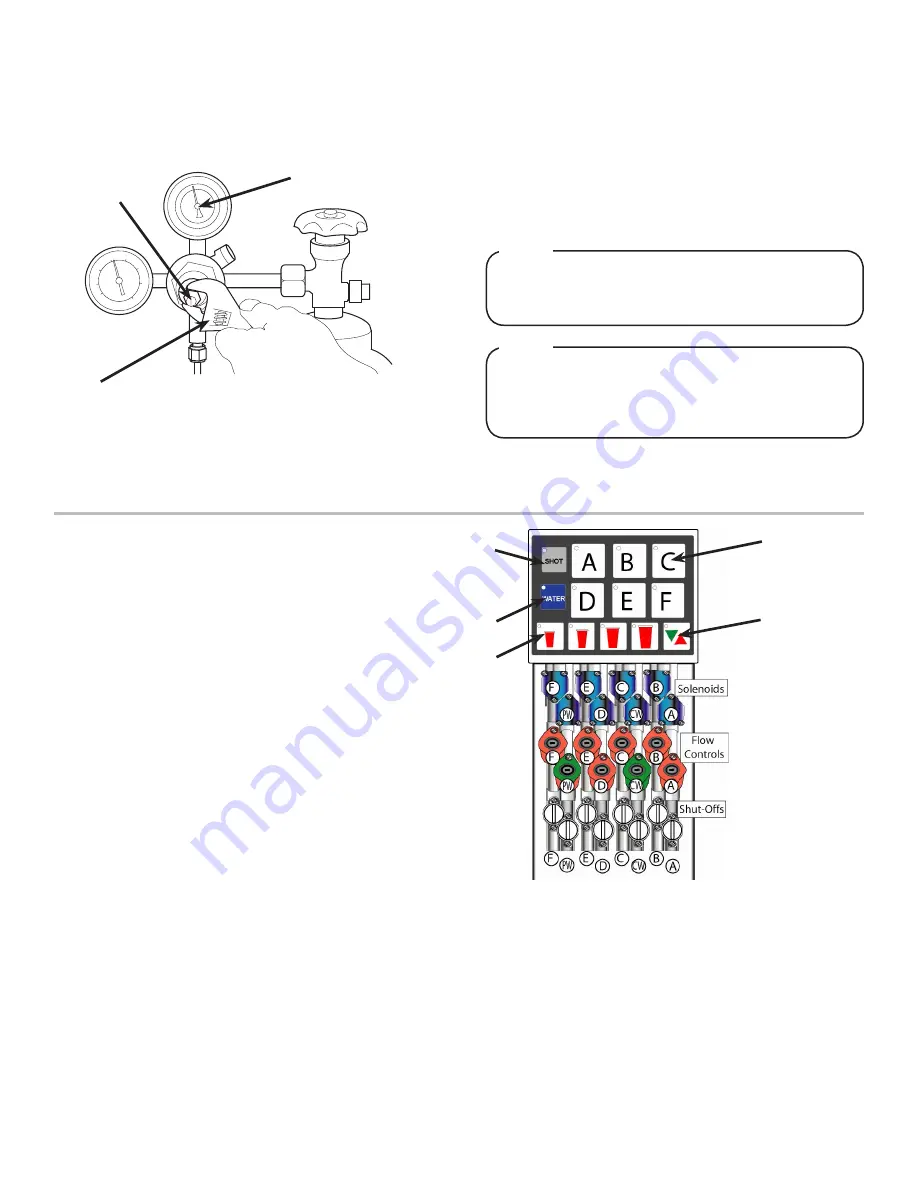
5
A. Regulator Adjustment Screw
B. Adjust to 110 PSI (0.758 MPA)
C. Wrench
A
B
C
8. Adjust both of the low pressure regulators on the regulator
manifold to 75 PSI (0.517 MPA) then tighten locknut with
wrench.
9. Activate each valve until gas-out.
10. Plug in the remote carbonator pump deck, if not already
done so, and turn the switch to the ON position.
11. Activate each valve until the carbonator pump comes on.
Release the button, allow carbonator to fill and stop.
Repeat this process until a steady flow of carbonated water
is achieved.
12. Activate each valve to purge air from the syrup lines.
The pump deck has a 3 minute timeout feature. If the
timeout occurs, turn the deck OFF then ON by flipping
the switch on the control box.
NOTE
To check for CO
2
leaks, close the valve on the CO
2
cylinder and observe if the pressure to the system
drops with the cylinder valve closed for five minutes.
Open the cylinder valve after check.
NOTE
5. Activate each valve to ensure a good flow of water is
achieved.
6. Ensure pump deck is turned OFF before turning on CO
2
.
7. Turn on CO
2
at the source then, using a screwdriver, adjust
the high pressure regulator at the source to 110 PSI (0.758
MPA) then tighten locknut with wrench.
MULTI-VALVE UNIT (MVU) PROGRAMMING
Overview
The MVU module is designed to dispense up to 6 beverages and/
or shots through one dispense nozzle. The MVU consists of: an
electronic board, touch pad which is used to both program and
dispense drinks, 8 solenoids (one for each circuit), 8 flow controls
(one for each circuit), and 8 shut-offs
1. Positions A and D are plumbed through the cold plate
meaning that the syrup is chilled in each of those locations.
2. Positions B, C, E, and F bypass the cold plate so the syrups
are not chilled and should
NOT
be used for carbonated
beverages.
3. The water flow controls are green in color the plain water
control is labeled with “PW”, and the carbonated water is
labeled with “CW”. There are no stickers on the water flow
controls.
4. The syrup flow control modules are red and correspond to
the touch pad, (touchpad position A activates solenoid A).
5. The 8 solenoids are 24 VDC, activated by the touch pad, and
controlled by the MVU circuit board.
A. Brand Button
B. Shot Button
C. Water Button
D. Portion Control
Buttons
E. Pour/Cancel
A
E
B
C
D