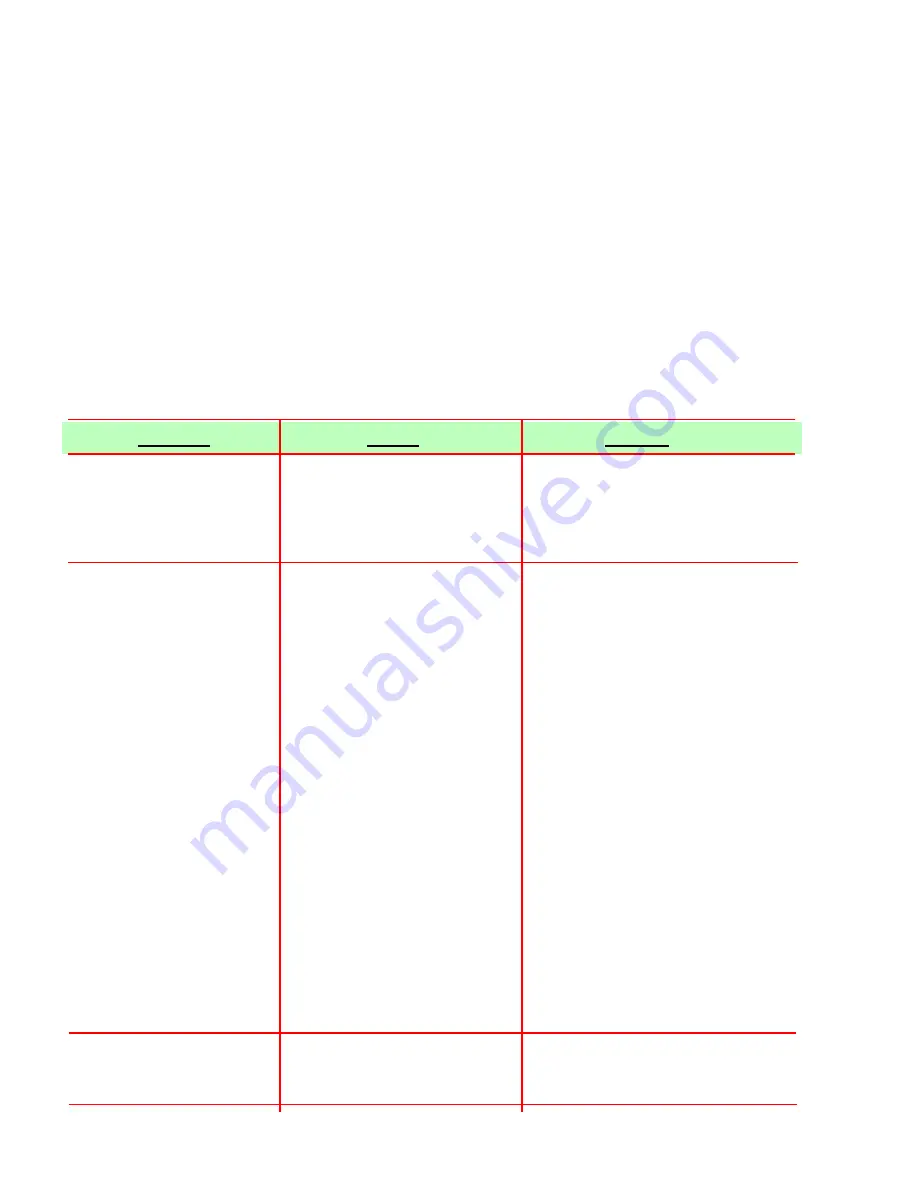
working parts, such as driver boards, from one side of the dispenser to the other side of the
dispenser. Similarly, the right and left door harnesses can be swapped at the electronic control box
to aid in trouble-shooting door problems.
Before troubleshooting a problem with the Electronic Control System, first perform a few initial tests
to aid in diagnosing the problem.
1. Be sure that the unit is plugged in.
2. Remove the splash plate and check all harness connections to the Electronic Control Box.
3. Turn the key switch to the ON position, and observe if the door lights illuminate.
4. Open the door and verify that the circulation fan is operating.
5. Check the harnesses at the top of the door to be sure they are completely engaged and latched.
6. Check the status of the LEDs on the front of the control box to be sure that all boards are
powered up properly to indicate the status of the machine.
7. Install a package in all of the valve positions. If packages are already installed, remove them
and reinstall to reset the SOLD OUT status.
Causes are listed in order of probability.
TROUBLE
CAUSE
REMEDY
6.6
Packages load properly
A. No water supply.
A. Check that unit is connected to an
but dispenser does not
adequate water supply. Check that
function on
all
valves.
1/4 turn inlet valve on dispenser is
Low water pressure
open.
signs come on the door
Board LCD.
6.7
Packages load properly,
A. Product sold out.
A. Check that valve position does not
but dispenser does not
have an empty package and that
function on
some
Refill Now light on door is off.
valves.
(Light will be off if there is a
useable package properly loaded in
the valve position. An empty
package will have non-blinking
Refill Now light.)
B. Sold out feature malfunction.
B. Check if Refill Now light on the
door goes out after inserting a
known good package from another
valve position and prime the pump
as shown in Section 2.2. If the
light does not go out, it indicates
either a faulty sold out emitter
module. Replace as necessary.
C. No signal from the water
C. 1.
Inspect connections of
calibration valve.
Low water
harnesses from insulated tank
pressure sign comes on.
assembly to Electronic Control
Box. Rectify if necessary
2.
Remove Fan plate and check
connections at water calibration
valve. Rectify if necessary.
3.
Swap suspect water calibration
valve with a known working
assembly and retest. If
suspect valve now functions,
replace water calibration valve
assembly (see Sec. 5.9).
6.8
Packages load properly
A. Key switch in rinse mode.
A. Turn key switch to the dispense
but dispenser only
position.
dispenses water from
B. Faulty key switch.
B. Replace key switch assembly.
all
valves.
17
Summary of Contents for 85-3322
Page 37: ...7 13 ASSEMBLED UNIT 34...