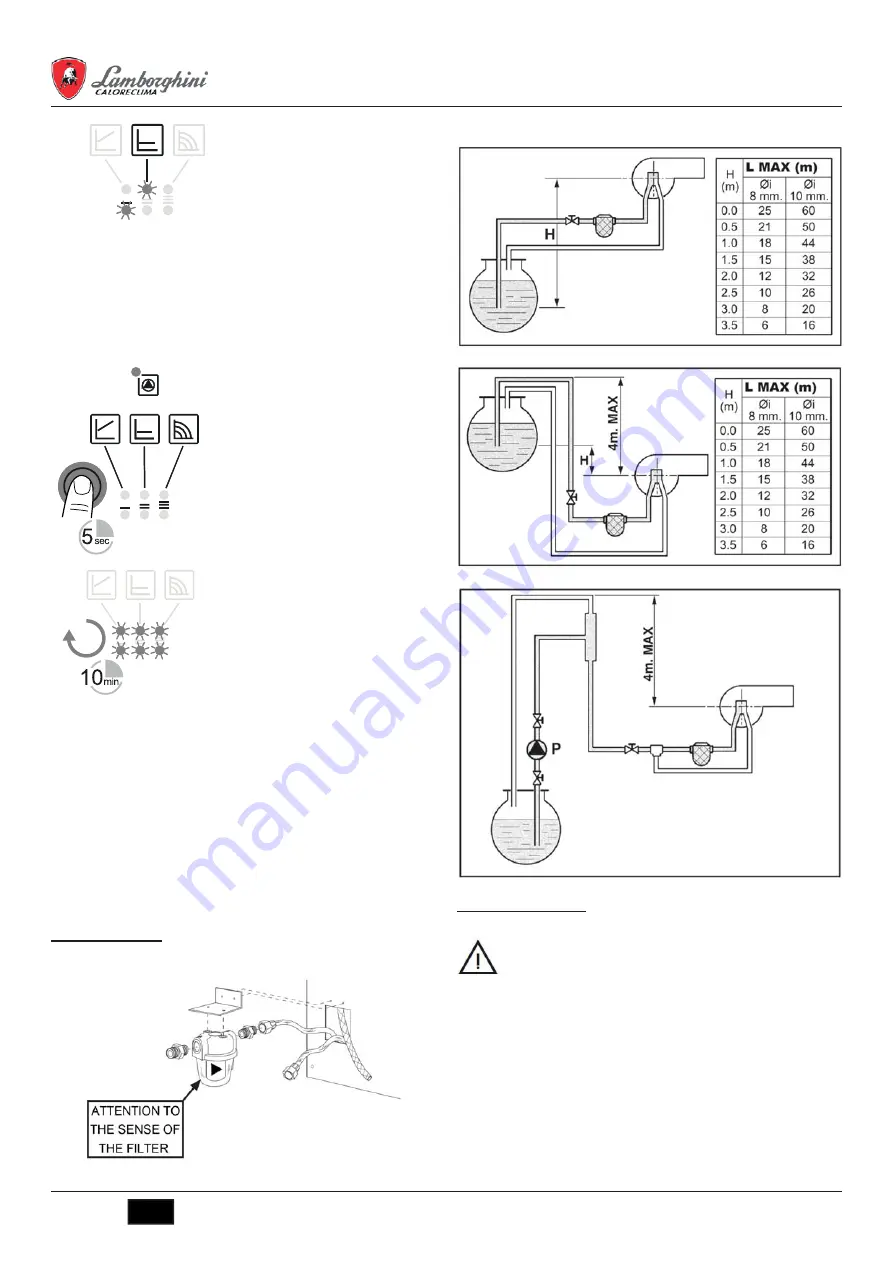
KYRA D 30 SI UNIT COND
A73022660
40
EN
ATTENTION
In case of a power failure, all settings
and displays remain stored.
Factory setting activation
The factory setting is activated by pressing and holding the control button and
deactivating the pump.
• Press the control button continuously for at least 4 seconds.
-
All LEDs
fl
ash for 1 second.
-
The LEDs of the last setting
fl
ash for 1 second.
On restarting the pump, it will work with the factory setting (delivery status).
Manual restart
•
When a blockage is detected, the pump
tries to restart automatically.
If the pump does not restart automatically:
•
Activate manual restart by pressing the
control button for 5 seconds, then release.
-
The restart function starts and lasts max.
10 minutes.
-
The LEDs
fl
ash clockwise one after the
other.
•
To stop, press the control button for 5 sec-
onds.
ATTENTION
After restarting, the LED indicator shows the
previously set pump values.
If it is not possible to eliminate a fault, con-
tact a system installer or Customer Service
System water characteristics
In case of water with hardness exceeding 25° Fr (1°F = 10ppm CaCO3), use suitably
treated water to prevent possible encrustations in the boiler. Treatment must not
reduce the hardness to values below 15°F (Decree 236/88 on water intended for
human consumption). However, treatment of the water is essential in case of very
large systems or frequent system water replenishment.
Frost protection system, antifreeze liquids, additives and inhibitors
A frost protection system activates the boiler in heating mode when the system
fl
ow temperature drops below 6°C. The device is not active if the power and/or
gas supply to the unit are disconnected. If necessary, the use of antifreeze liquids,
additives and inhibitors is allowed, only and exclusively if their manufacturer
provides a guarantee ensuring that the products are suitable for use and do not
cause damage to the boiler exchanger or to other components and/or materials of
the boiler and system. The use of antifreeze liquids, additives and generic inhibitors,
not speci
fi
cally suitable for use in heating systems compatible with the boiler and
system materials, is prohibited.
3.4 Burner connection
The burner is equipped with
fl
exible pipes and a
fi
lter for connection to the oil feed
line.Run the
fl
exible pipes out of the back and install the
fi
lter as indicated in
fi
g.20.
fi
g.18 - Fuel
fi
lter installation
The oil feed circuit must be made according to one of the following diagrams, with-
out exceeding the pipe lengths (LMAX) given in the table.
fi
g.19 -Suction feed
fi
g.20 - Siphon feed
fi
g.21 - Ring feed
3.5 Electrical connections
Connection to the electrical grid
The unit’s electrical safety is only guaranteed when correctly connected
to anef
fi
cient earthing system executed according to current safety
standards. Havethe ef
fi
ciency and suitability of the earthing system
checked by professionally quali
fi
ed personnel. The manufacturer is not
responsible for any damage caused by failure to earth the system. Also
make sure that the electrical system is adequate for the maximum power
absorbed by the unit, as speci
fi
ed on the boiler dataplate.
The boiler is prewired and provided with a Y-cable and plug for connection to the
electricity line. The connections to the grid must be made with a permanent connec-
tion andequipped with a bipolar switch whose contacts have a minimum opening of
at least 3mm, interposing fuses of max. 3A between the boiler and the line. It is im-
portant to respect the polarities (LINE: brown wire / NEUTRAL: blue wire / EARTH:
yellow-greenwire) in making connections to the electrical line. During installation or
when changingthe power cable, the earth wire must be left 2 cm longer than the
others.