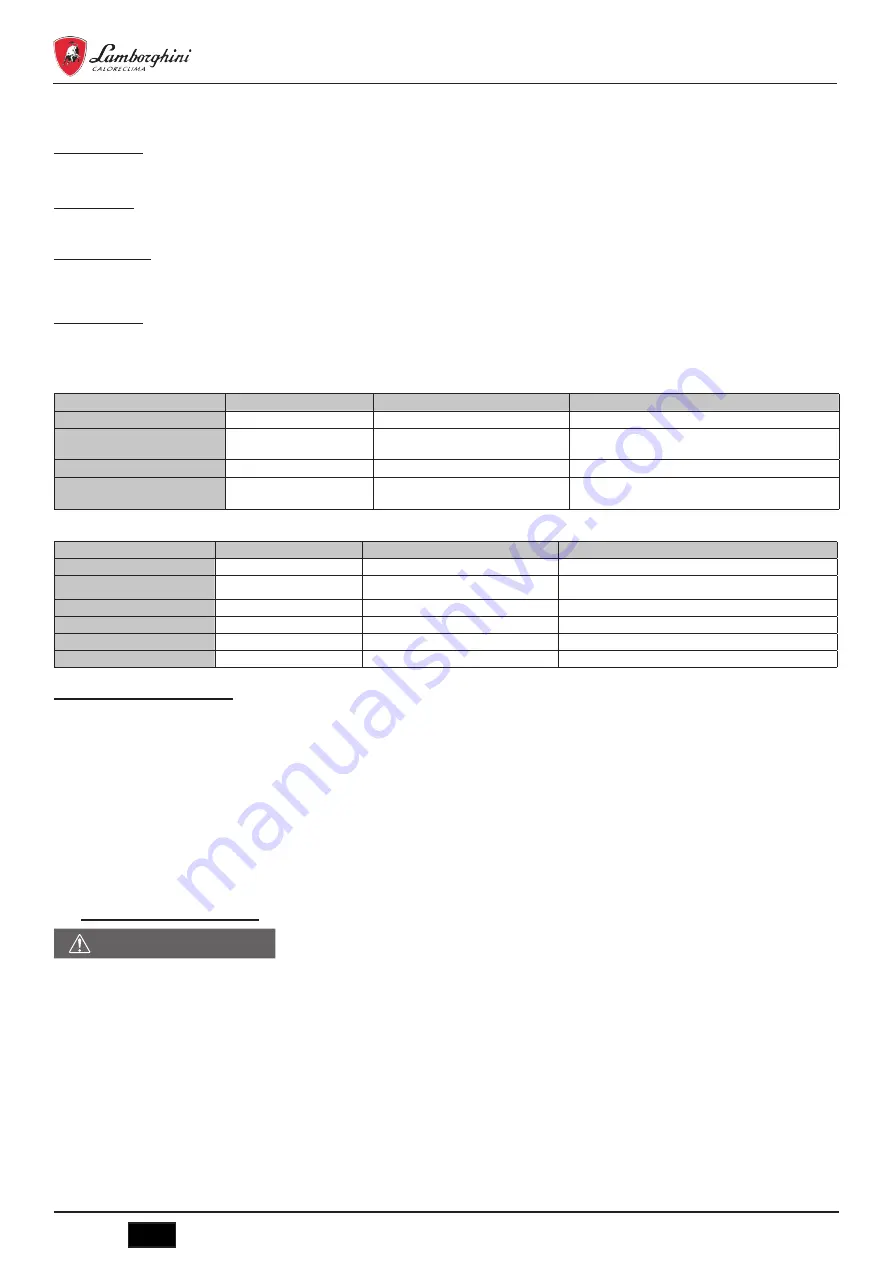
62
EN
Cod. 3541Z090 - Rev. 05 - 05/2022
IDOLA S 3.2
It is forbidden to leave containers of inflammable substances near the unit.
Do not touch the appliance with bare feet or with wet or moist parts of the body.
The checks described must be performed at least once a year by qualified personnel.
Electrical cabinet
Carry out a thorough visual inspection of the components of the electrical panel to check for damaged or incorrectly connected components or cables (check the tight-
ness of the terminal screws).
Residual Risks
The machines has been designed with a view to reducing the risks to persons and the environment in which it is installed, to the minimum. To eliminate residual risks,
it is therefore advisable to become as familiar as possible with the machine in order to avoid accidents that could cause injuries to persons and/or damage to property.
a. Access to the unit
Only qualified persons who are familiar with this type of machine and who are equipped with the necessary safety protections (footwear, gloves, helmet, etc.) may
be allowed to access the machine. Moreover, in order to operate, these persons must have been authorized by the owner of the machine and be recognized by the
actual Manufacturer.
b. Elements of risk
The machine has been designed and built so as not to create any condition of risk. However, residual risks are impossible to eliminate during the designing phase and
are therefore listed in the following table along with the instructions about how to neutralize them.
Indoor unit residual risks
Part in question
Residual risk hazard
Mode
Precautions
Refrigeration and hydraulic pipes
Burns
Contact with pipes
Avoid contact by wearing protective gloves
Refrigerant pipes, plate heat exchanger.
Explosion
Excessive pressure
Switch off the machine, check the high pressure switch and the
safety valve, fans and capacitor
Refrigerant pipes
Ice burns
Refrigerant leakage
Do not pull the pipes
Electric cables, metal parts
Electrocution, serious burns
Insulation of faulty cable, live metal parts
Suitable electric protection (correct unit grounding)
Outdoor unit residual risks
Part in question
Residual risk hazard
Mode
Precautions
Compressor and delivery pipe
Burns
Contact with pipes and/or compressor
Avoid contact by wearing protective gloves
Drain pipe and coil
Explosion
Excessive pressure
Switch off the machine, check the high pressure switch and the
safety valve, fans and capacitor
Refrigerant pipes
Ice burns
Refrigerant leakage
Do not pull the pipes
Electric cables, metal parts
Electrocution, serious burns
Insulation of faulty cable, live metal parts
Suitable electric protection (correct unit grounding)
Thermal exchange coil
Cuts
Contact
Wear protective gloves
Fan
Cuts
Contact with skin
Do not put your hands or objects through the fan grilles
General Rules for Maintenance
The maintenance is extremely important for the functioning of the system and the regular working of the unit over time.
In accordance with the European Regulation EC 303/2008 , it should be noted that companies and engineers in maintenance , repair, leak testing and recovery /
recycle refrigerant gases should be CERTIFIED in accordance with local regulations.
Maintenance must be performed in compliance with the safety rules and tips given in the manual supplied with the unit.
Routine maintenance helps maintain unit efficiency, reduce the rate of deterioration which each device is subject in time and gather information and data to understand
the efficiency of the unit and prevent failures.
For extraordinary maintenance or in case you need service , contact only to a specialized service centre approved by the manufacturer and use original spare parts.
In accordance with the European Regulation EC 1516/2007 it is necessary to prepare a “equipment record”.
Provide anyway a databook (not supplied) that allows you to keep track of interventions made on the unit; in this way it will be easier to properly program the various
interventions and will facilitate a possible troubleshooting.
Bring on the databook : date, type of intervention made, description of the intervention , measurements , reported anomalies , alarms recorded in the alarm history ,
etc. ...
12.2 Access to internal components
CAUTION
Some internal components of the indoor unit can reach sufficiently high temperatures that may cause serious burns. Before carrying out
any intervention, wait until these components have cooled down or wear suitable gloves.
For details about how to access to the internal components, refer to "How to access to the electric box" on page 33.