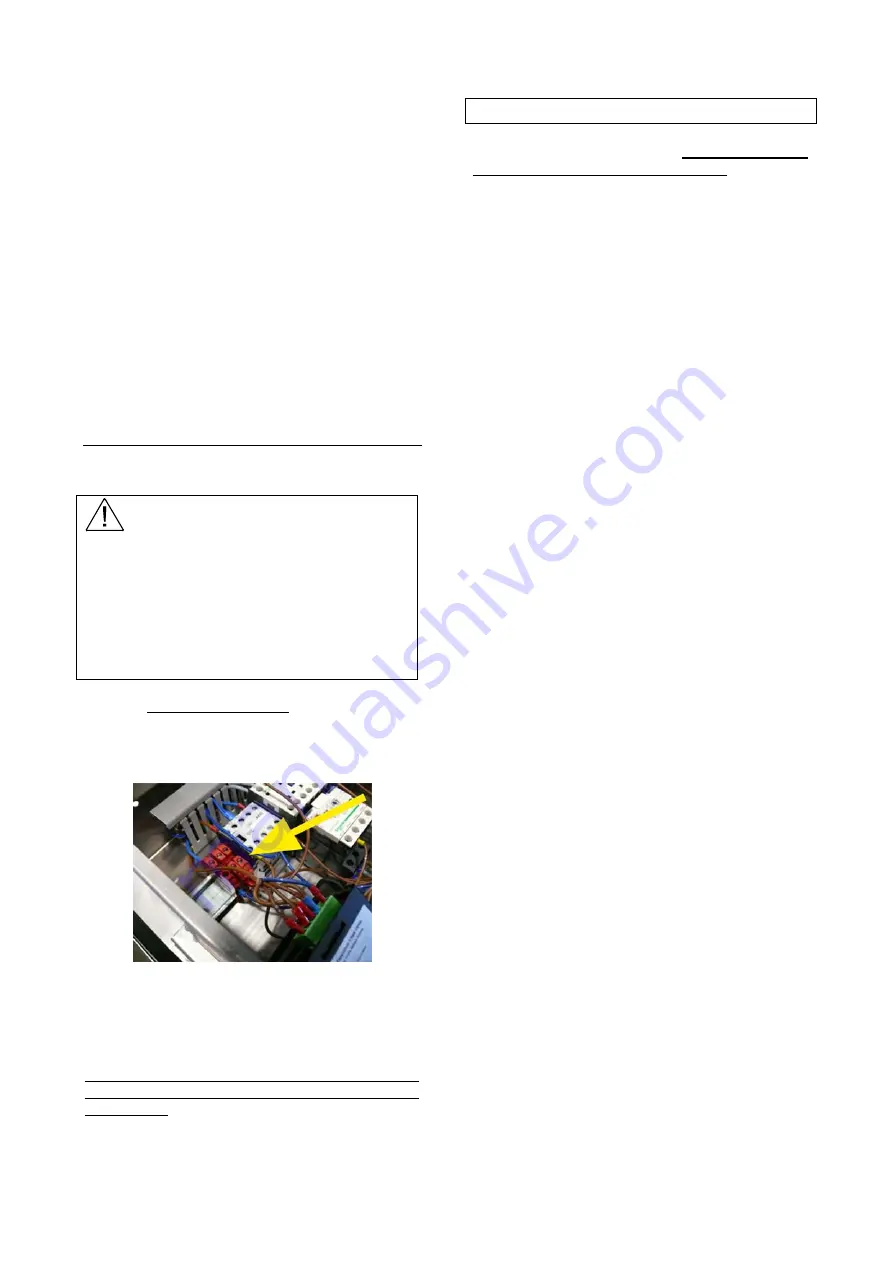
36
The choice of a suitable cleansing agent is an
essential condition if you want to obtain
extremely good washing results as regards
hygienic results. That’s why it’s important to
consider some points. First of all only highly
alkaline and chlorine-active antifoam products,
especially made for industrial dish-washing
machines, must be used and they must be
produced by well-known reliable Firms. Mean
concentration of the cleansing agents in powder
must be 1,5÷2,5 g/lt. Mean concentration of
liquid cleansing agents must be 2÷4 g/lt.
In order to avoid scales and corrosions, put
cleansing agent above water level on the
nearest area of the sucking pump filter, in this
way it will immediately dilute and will not deposit
on the tank bottom.
ELECTRICAL CONNECTION OF DETERGENT
DISPENSER
(ONLY FOR MACHINES WITH INCORPORATED
DETERGENT PUMP AND EXPANSION BOARD
WARNING
:
Danger to life due to live
components!
During all electrical operations, disconnect the
machine from the network and verify the
absence of power.
The machine and its accessories must be connected
in accordance with local regulation, by a
company that is specialized in electrical
installation authorized by the competent
authorities.
For the electrical connection of the dispenser,
refer to the red terminals inside the electrical
cabinet (see photo below) and refer to the wiring
diagram sheet 3.
To prevent damages to the electrical components
of the machine is mandatory the use of these
terminals to avoid flying connections in other parts
of the installation (valves, etc.)
N.B. For the cables using the cable gland
provided in the electrical control box and identified
with a lebel..
DESCALING CYCLE :
For programming, see section CONFIGURATION
USER TECHNICAL-PROGRAMMING
The descaling cycle has a duration of about 35
minutes and takes place according to the steps
listed below:
1. pump dispenser rinsing and descaling
until the tank is full
2. heating phase until the boiler
temperaturer >50°Cand tank> 45 °C
3. wash pumps for 1 minute
4. 1 minute rest
5. wash pump for 1 minute
6. rinsing pump and limestone dosing for
15 seconds
7. 1 minute rest
8. wash pump for 1 minute
9. 1 minute rest
10. wash pump for 1 minute
11. rinsing pump and limestone dosing for
15 seconds
12. 1 minute rest
13. wash pump for 1 miunute
14. 1 minute rest
15. washing pump for 1 minute
16. rinsing pump for 15 seconds
17. heating boiler off
18. 1 minute rest
19. washing pump for 1 minute
20. 1 minute rest
21. washing pump for 1 minute
22. rinsing pumps for 15 seconds
23. 1 minute rest
24. drain pump until the tank is empty and
for another 2 minutesi
25. rinsing pump up to full tank
26. washing pump for 5 seconds
27. drain pump until the tank is empty and
for another 2 minutes
Summary of Contents for LP6-dy
Page 1: ...POT WASHER LP6 dy LP8 dy LP6 dy CVP S LP8 dy CVP S INSTRUCTIONS MANUAL R00 2017...
Page 2: ...2...
Page 9: ...INSTRUCTIONS FOR THE USER...
Page 28: ...28...
Page 30: ......
Page 31: ......
Page 32: ...32...
Page 45: ...01 02 2017 15 06 39...
Page 46: ...01 02 2017 15 06 40...
Page 47: ...01 02 2017 15 06 40...
Page 48: ...01 02 2017 15 06 40...
Page 51: ......
Page 52: ......