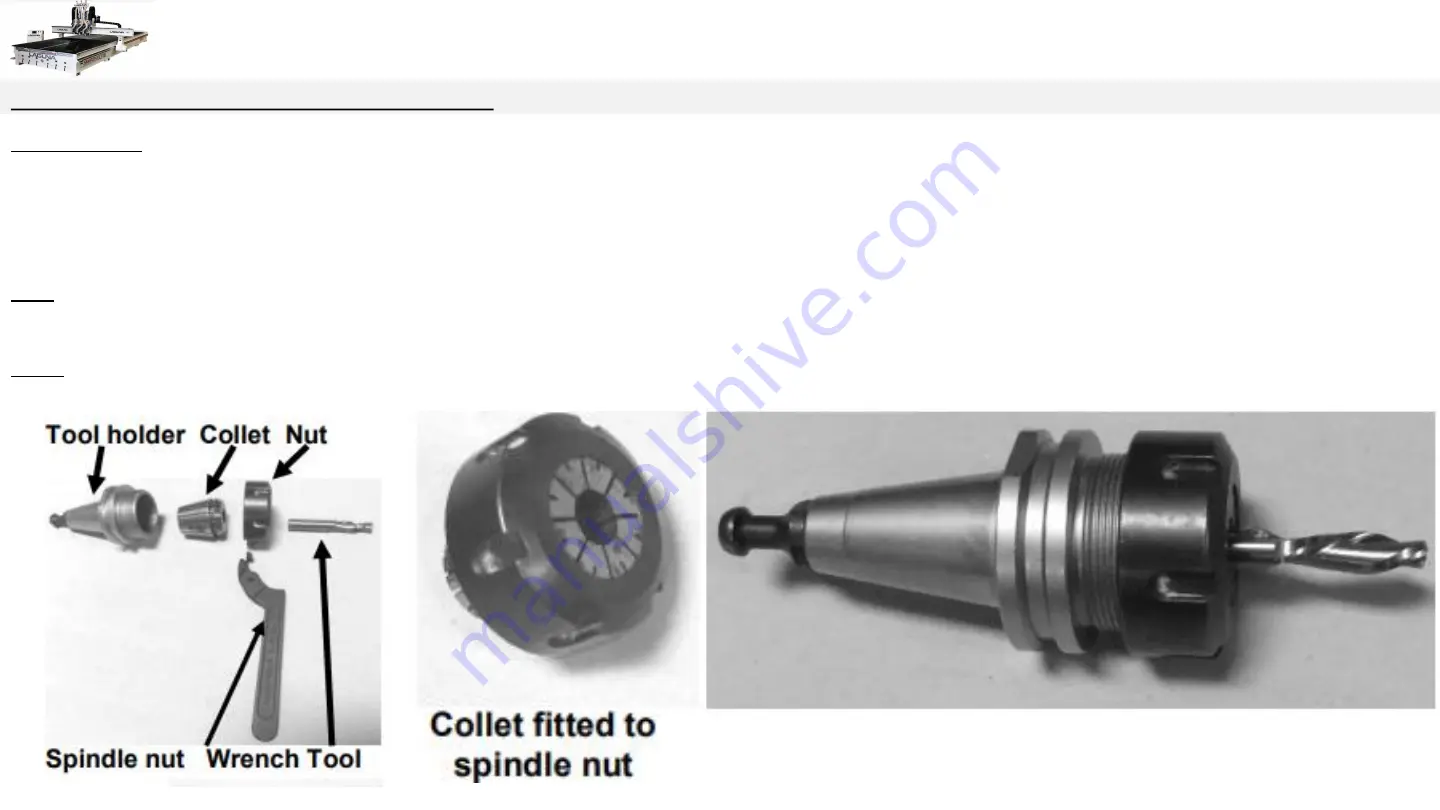
Fitting the Router Bit into the Router Head-
Safety Note
: Before changing or fitting the router bit, always disconnect the power from the machine.
Note
: The router bit must not be fitted into the collet until the collet has been fitted into the spindle nut. With the router bit fitted into the collet, the collet cannot
compress and snap into the spindle nut. The face of the collet and the face of the spindle nut will be close to flush.
Note:
To remove the collet, hold the spindle nut and press the collet on the side. The collet will compress and pop out. Do not try to remove the collet while a cutter is
fitted, as the collet will not compress and pop out.
1.) Select a router bit and its relevant collet.
2.) Fit the collet into the spindle nut. Press the collet into the spindle nut until it snaps into place.
Fully Assembled.
Summary of Contents for Smartshop Composite Fabricator 16
Page 32: ...32 Main Screen Button s Flow Main Screen...
Page 53: ...Schematics...
Page 54: ...Schematics Cont d...
Page 55: ...Schematics Cont d...
Page 56: ...Schematics Cont d...
Page 57: ...Schematics Cont d...
Page 58: ...Schematics Cont d...
Page 59: ...Schematics Cont d...
Page 60: ...Schematics Cont d...
Page 61: ...Schematics Cont d...
Page 62: ...Schematics Cont d...
Page 63: ...Schematics Cont d...
Page 64: ...Schematics Cont d...
Page 65: ...Schematics Cont d...
Page 66: ...Schematics Cont d...
Page 72: ...Laguna Tools Warranty...
Page 75: ...Laguna Tools Packaging Laguna Tools RMA Example RMA...
Page 76: ...76 Laguna Tools Packaging Laguna Tools BILL of LADING Example...