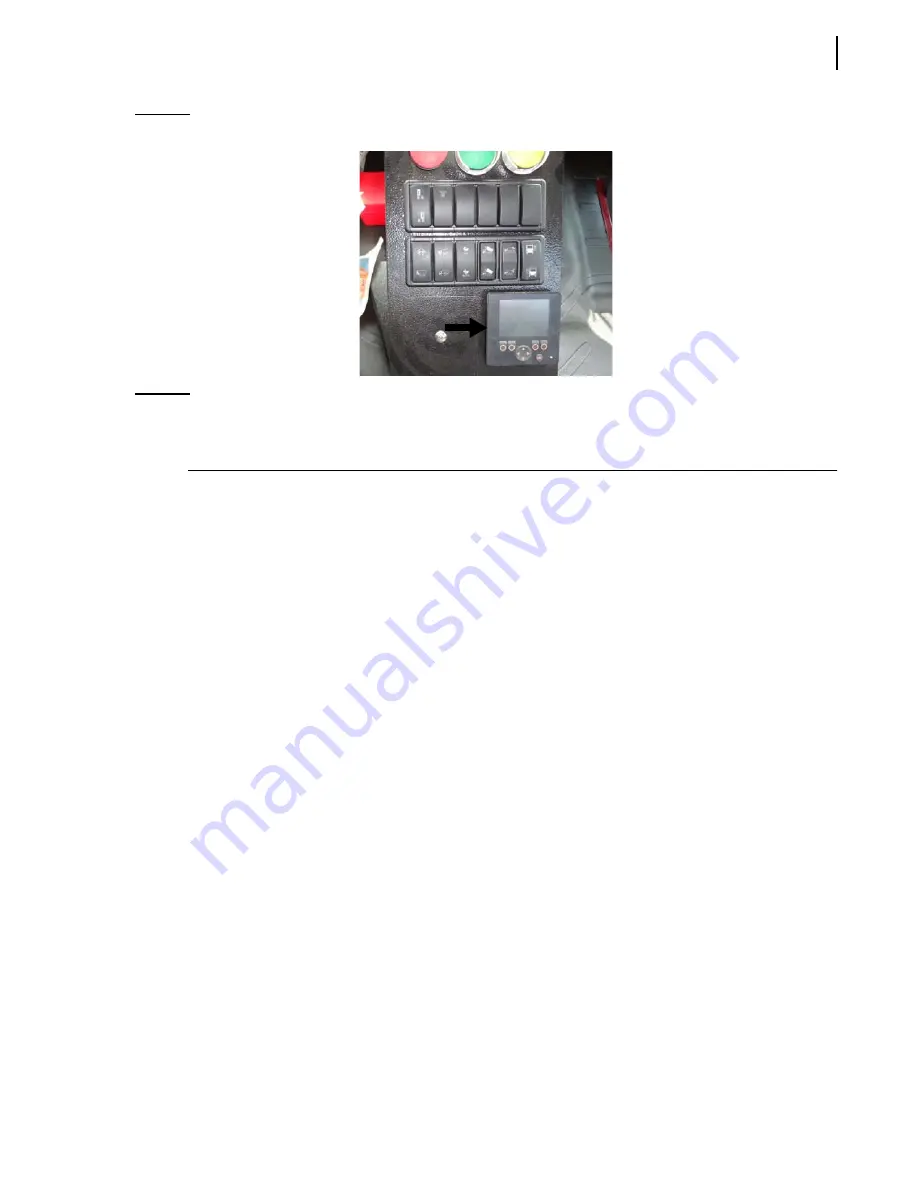
Introduction
3
Figure 1-1 Monitor
N
OTE
:
Maintenance personnel as well as in-the-field technicians who encounter any problems with
the multiplexed system should refer to the
Multiplex Diagnostic Manual
(part# 153143) for
troubleshooting information and guidelines.
Key Features
The A
UTOMIZER
™, with its advanced design, delivers a lower total vehicle weight and allows for a
higher packing capacity. This translates into greater flexibility and a lower Total Cost of Ownership
(TCO) for our customers.
Key features of the A
UTOMIZER
™:
Environmental benefits
Light weight, high compaction, fast cycle times
Reliable electronic monitoring system
Strongly built automated lifting arm
Increased fuel efficiency and decreased fuel consumption
Low maintenance
Low profile
Warning
Your A
UTOMIZER
™ unit MUST BE COMPLETELY LUBRICATED before its first use.
Initial lubrication carried out by Labrie Enviroquip Group is sufficient for production and transport
purposes ONLY.
Important Notice about the Warranty
Do not forget to complete the Owner Registration Form and send it to Labrie Enviroquip Group.
Make sure to indicate the date the truck is placed in service (“In-Service Date”). This date will be
used to start the warranty period. Otherwise, the date of delivery from the factory will be used instead.
Summary of Contents for automizer
Page 1: ...AUTOMIZERTM MAINTENANCE MANUAL...
Page 2: ......
Page 3: ...AUTOMIZER MAINTENANCE MANUAL...
Page 10: ...viii Table of Contents...
Page 16: ...6 Introduction...
Page 30: ...20 Safety 7 Put the safety pin back in place...
Page 83: ...General Maintenance 73 Figure 3 72 Rubber seal...
Page 114: ...104 Lubrication Figure 4 10 Lube charts on vehicle right hand side...
Page 115: ...Lubrication 105 Figure 4 11 AUTOMIZER lubrication charts...
Page 116: ...106 Lubrication...
Page 124: ...114 Lubrication Packer Lubrication Points 2 Grease fitting LH side front cylinder pin...
Page 126: ...116 Lubrication Sump Box Hinges Grease fittings...
Page 180: ...170 Pneumatic System...
Page 183: ...Troubleshooting 173 Figure 8 4 Ball end hex wrench metric and SAE...
Page 192: ...182 Troubleshooting Figure 8 9 Tailgate locking mechanism...
Page 239: ...Lifting Arms 229 Figure 10 23 Arm w 96 gallon gripper...