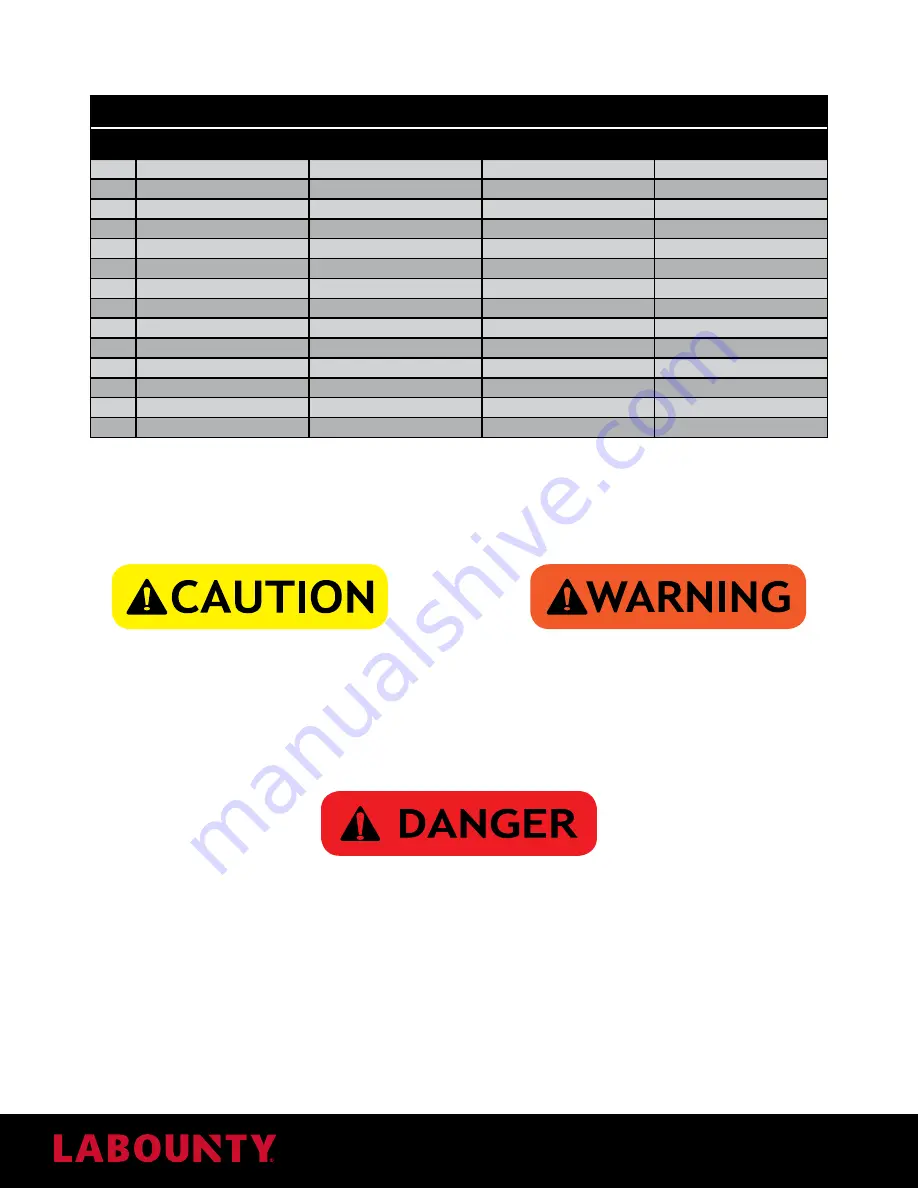
MRX Multi-kit Demolition Tool Operation & Maintenance Manual | 23
INSPECT / TORQUE BOLTS
General Fastener Torque Table
Size
6S
8.8 - (8G)
Class 10.9
Class 12.9
M5
4 Ft. Lbs. (5.10 Nm)
4 Ft. Lbs. (5.98 Nm)
6 Ft. Lbs. (8.5 Nm)
8 Ft. Lbs. (10.2 Nm)
M6
6 Ft. Lbs. (8.73 Nm)
8 Ft. Lbs. (10.3 Nm)
11 Ft. Lbs. (14.7 Nm)
13 Ft. Lbs. (17.6 Nm)
M8
16 Ft. Lbs. (21.58 Nm)
19 Ft. Lbs. (25.5 Nm)
26 Ft. Lbs. (35.3 Nm)
31 Ft. Lbs. (42 Nm)
M10
31 Ft. Lbs. (42.2 Nm)
37 Ft. Lbs. (50 Nm)
52 Ft. Lbs. (70.6 Nm)
63 Ft. Lbs. (85.5 Nm)
M12
54 Ft. Lbs. (73.6 Nm)
64 Ft. Lbs. (87.3 Nm)
90 Ft. Lbs. (122.6 Nm)
108 Ft. Lbs. (147 Nm)
M14
86 Ft. Lbs. (116.7Nm)
102 Ft. Lbs. (138.3 Nm)
143 Ft. Lbs. (194.2 Nm)
174 Ft. Lbs. (235.5 Nm)
M16
132 Ft. Lbs. (178.5 Nm)
156 Ft. Lbs. (210.9 Nm)
221 Ft. Lbs. (299.2 Nm)
264 Ft. Lbs. (358 Nm)
M18
181 Ft. Lbs. (245 Nm)
213 Ft. Lbs. (289.4 Nm)
304 Ft. Lbs. (412 Nm)
362 Ft. Lbs. (490.5 Nm)
M20
257 Ft. Lbs. (348.5 Nm)
304 Ft. Lbs. (412 Nm)
427 Ft. Lbs. (578.8 Nm)
514 Ft. Lbs. (696.5 Nm)
M22
347 Ft. Lbs. (471 Nm)
412 Ft. Lbs. (559.2 Nm)
579 Ft. Lbs. (784.8 Nm)
695 Ft. Lbs. (942 Nm)
M24
441 Ft. Lbs. (598.5 Nm)
525 Ft. Lbs. (711.2 Nm)
738 Ft. Lbs. (1000.5 Nm)
883 Ft. Lbs. (1197 Nm)
M27
655 Ft. Lbs. (888 Nm)
774 Ft. Lbs. (1049.7 Nm)
1092 Ft. Lbs. (1481 Nm)
1310 Ft. Lbs. (1776 Nm)
M30
890 Ft. Lbs. (1206.5 Nm)
1049 Ft. Lbs. (1422.4 Nm)
1483 Ft. Lbs. (2011 Nm)
1772 Ft. Lbs. (2403 Nm)
M33
1201 Ft. Lbs. (1628.5 Nm)
1425 Ft. Lbs. (1932.6 Nm)
2004 Ft. Lbs. (2717 Nm)
2410 Ft. Lbs. (3267 Nm)
BLADE MAINTENANCE
Before performing blade maintenance, place the attachment on the ground, so that the part being maintained is closest
to the ground. When performing maintenance on the upper jaw curl the attachment under the stick so that the upper
jaw is on the ground.
Wear personal protection equipment at all times. This
includes eye protection, hard hat, steel toe shoes,
leather gloves and hearing protection.
Blades are very heavy. Do not remove a blade if it’s not
supported. The blade may fall and cause injury.
CRACKER JAW
Measuring Blade Gap and Shimming
Note: Removing and handling blades can be hazardous if done incorrectly.
Stay at least 75 ft. (23 m) when moving.
1.
Cycle the tool until the upper jaw blade begins to overlap the lower jaw blade.
2.
Measure the blade gap. If the gap is larger than 0.4 mm, add shims between the guide blade and blade seat until the
gap is 0.4 mm - 0.4 mm.
Blade Rotation
Each cracker jaw blade has four edges. Each time you rotate the blade, use a different edge until all the edges are
worn to .25” radius.
Summary of Contents for MRX Series
Page 28: ...28 MRX Multi kit Demolition Tool Operation Maintenance Manual Wear Plates...
Page 30: ...30 MRX Multi kit Demolition Tool Operation Maintenance Manual...
Page 33: ......
Page 34: ......
Page 35: ......