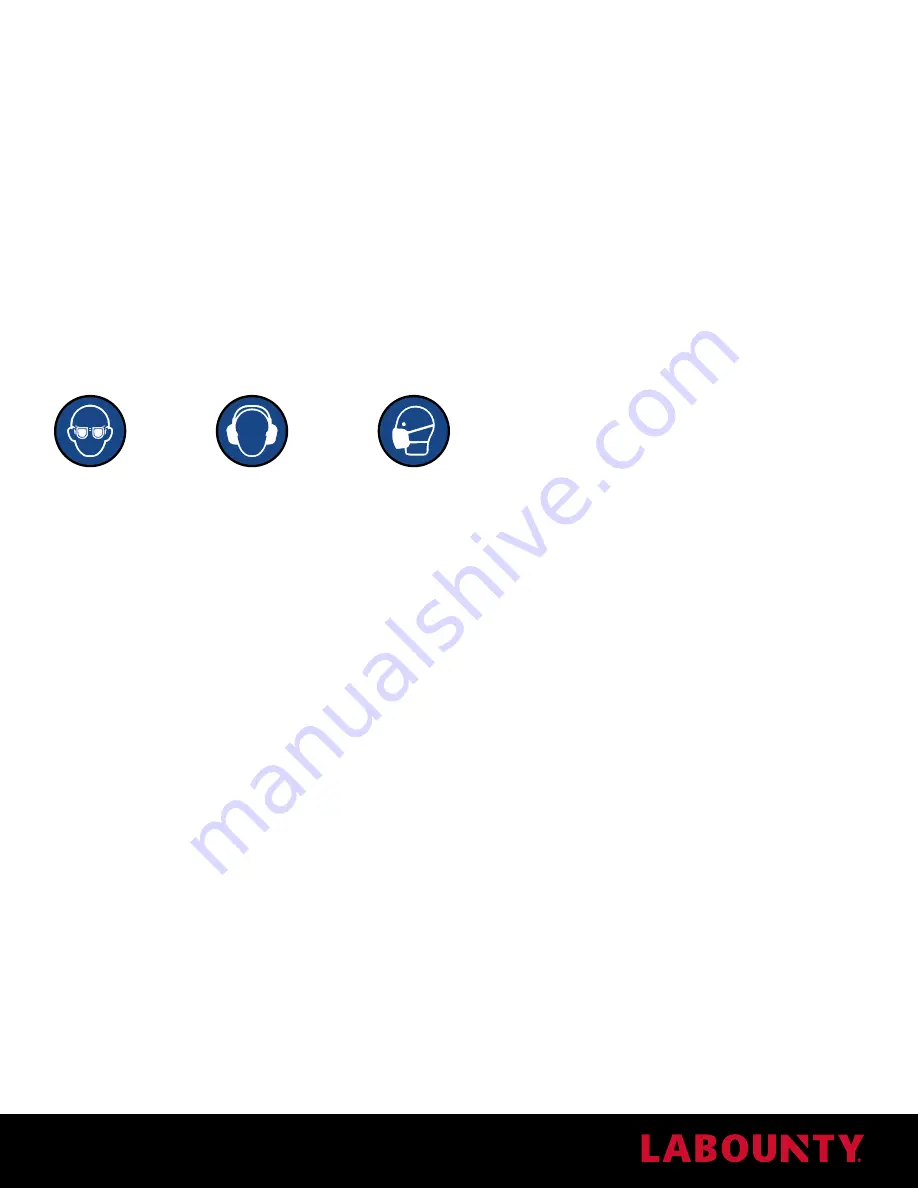
16 | MRX Multi-kit Demolition Tool Operation & Maintenance Manual
OPERATION
BEFORE YOU START
Know Your Safety Program
•
Read and understand this manual and the base
machine manual.
•
Know the employer’s safety rules. Consult your
foreman for instructions and safety equipment.
•
Learn the traffic rules at the work site. Know the hand
signals used on the job and who is responsible for
signaling. Take signals from only
ONE
person.
•
Wear personal protection equipment. This includes
eye protection, hard hat, steel toe shoes, gloves,
hearing protection and respirator.
Wear Ear
Protection
Wear Eye
Protection
Wear a Mask
Know Your Equipment
•
Learn and test the function of all controls. If
malfunctions are found, shut the machine down and
report the malfunction for repair.
•
Be familiar with safety devices, indicators, warning
devices and caution instructions. They will alert you to
conditions that are hazardous.
•
Know the clearances in the work area.
Daily Safety Checks
•
Ensure all decals are installed and legible. Contact
LaBounty for replacements as required.
•
Have a
DAILY
safety dialog with all workers. Inform
them of any abnormal work that is planned. Remind
them of the safe working distance.
•
Clear the area.
ALWAYS
look out for others. In any
work area, people constitute a serious safety hazard.
Before operating, walk around the machine to ensure
no workers are next to, under or on it. Warn nearby
workers that you are starting up.
DO NOT
start up until
they are out of danger.
•
Check the location of cables, gas lines and water
mains before operation. Ensure work site footing has
sufficient strength to support the machine. When
working close to an excavation, position machine with
the propel motors at the rear.
•
Keep bystanders clear, especially before moving the
boom, swinging the upper structure, or traveling.
ALWAYS
be alert for bystanders in or near the
operating area.
SAFETY DEVICES
•
Seat belts
•
Canopies
•
Safety decals
•
Shields and guards
•
Flags and flares
•
Barricades
•
Signs and other
markings
•
Warning lights
•
Falling Objects
Protective Structures
(FOPS)
•
Visual or audible
warning devices
General Rules For Safe Operation
• KNOW
the capacity of the excavator and it’s
attachments.
DO NOT
overload or serious injury
could result. The attachment may have altered the
machine’s lift capabilities.
•
This attachment is for processing materials.
DO NOT
use for unapproved purposes.
•
DO NOT continuously process oversized materials by
forcing them into the jaw. This will shorten the life of
the attachment.
•
If attachment stalls, scale back the amount of material
being processed at one time. Overloading can cause
overheating or damage to the hydraulic system.
•
Cycle the cylinder completely when processing.
Fully cycling will allow hydraulic fluid to circulate and
prevents overheating.
•
Maintain a safe distance.
• NEVER
leave the attachment suspended or pass it
over people, occupied vehicles or buildings.
•
When working in confined spaces, keep watch on
exposed parts, such as cylinder rods and hoses, to
avoid damage.
•
Maintain at least 50 feet (15 meters) between the
attachment and any nearby power lines.
• ALWAYS
lower the attachment to the ground and
turn the base machine off when leaving the machine
unattended.
• DO NOT
close the jaws on a structure and reverse
the excavator in an attempt to pull down material. This
is dangerous and will damage the excavator and the
attachment.
•
Avoid collision of the boom or jaws, especially when
working with limited visibility or inside buildings.
Know the height and reach of the attachment during
operation, transport and when swinging the excavator.
• DO NOT
alter factory preset hydraulics. This may void
the warranty.
• DO NOT
shear high tensile steel, such as railroad
rail, spring steel, axles and some types of wire. Jaw
damage will result. This type of material breaks when
processed and can become a projectile which could
cause injury or death.
Summary of Contents for MRX Series
Page 28: ...28 MRX Multi kit Demolition Tool Operation Maintenance Manual Wear Plates...
Page 30: ...30 MRX Multi kit Demolition Tool Operation Maintenance Manual...
Page 33: ......
Page 34: ......
Page 35: ......