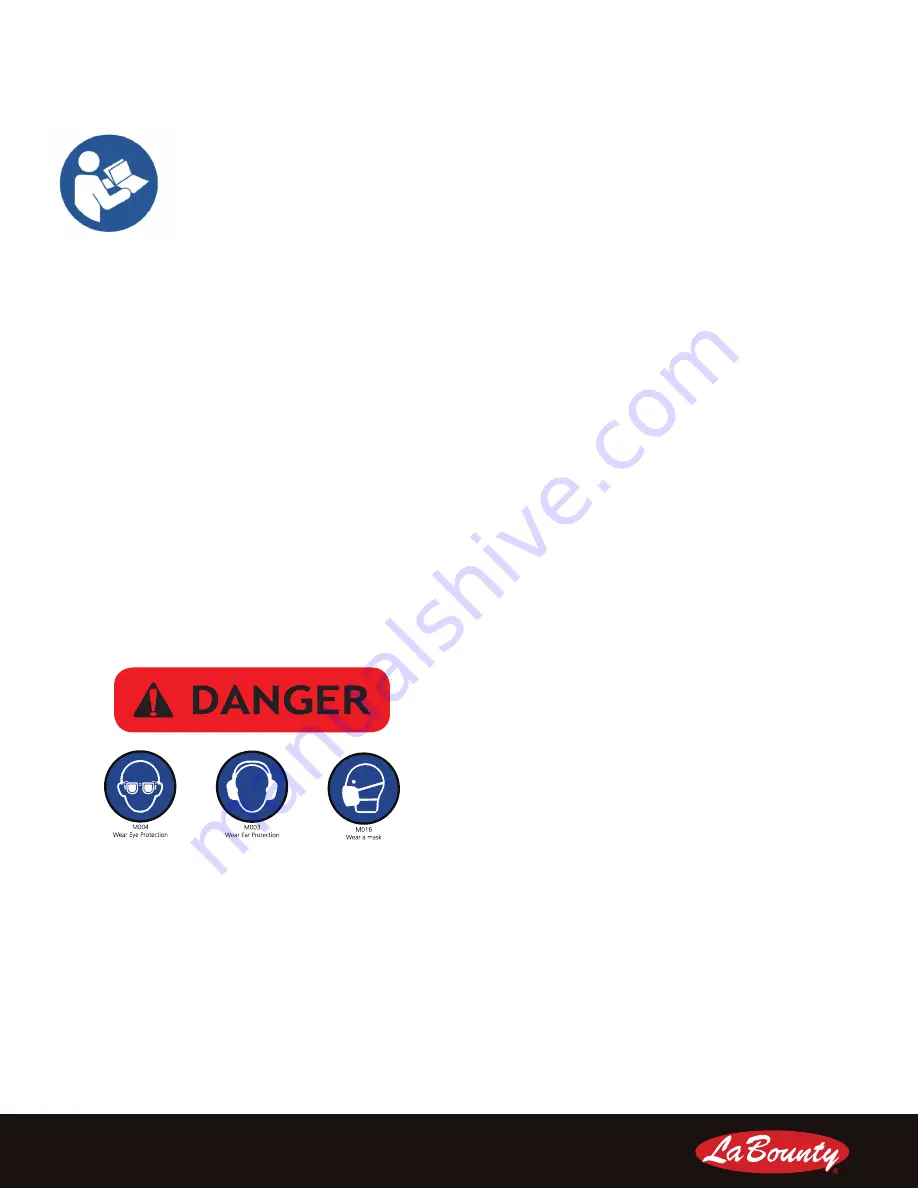
4 | MDG Operating & Maintenance Manual
SAFETY
Your safety and the safety of others
is a direct result of how you operate
and maintain your equipment. Read
and understand this manual and other
safety information provided with the
base machine and be sure that you
understand all controls and operating
instructions before attempting to operate this equipment.
Failure to follow the safety precautions can result in
personal injury, death or property damage.
Carefully read all safety messages in this manual and on
your equipment safety decals to reduce the risk of injury.
Keep safety decals in good condition. Replace missing or
damaged safety decals. Failure to follow the warnings and
instructions may result in serious injury or damage to the
tool.
Because LaBounty cannot foresee all hazardous
circumstances, the precautions listed in this manual and
on the equipment are not all-inclusive. If a procedure,
method, tool or part is not specifically recommended by
LaBounty, determine whether it is safe for you and others,
and that the equipment will not be damaged or made
unsafe as a result of your decision to implement it.
The basic rules are summarized in this section of the
manual. They also appear throughout the manual along
with additional specific rules for safety and operation.
•
Wear personal protection equipment. This includes
eye protection, hard hat, steel toe shoes, gloves,
hearing protection and respirator.
•
Use PPE that conforms to standards ANSI Z87.1 (Eye
and Face Protection), ANSI Z89.1 (Head Protection)
and ANSIZ41.1 (Foot Protection).
•
If the attachment is not functioning properly, shut
down the machine, follow proper lockout / tag out
procedures and follow proper repair procedures.
•
NEVER operate equipment without the original safety
guards in place.
•
Ensure that the cab is equipped with the proper
safety guards for LaBounty applications. The cab
MUST be equipped with an approved Falling Object
Protection Structure (FOPS). The FOPS must
meet the requirements of SAE standard J1356. A
transparent, shatter-resistant shield covering the
front of the cab, is also required. Contact your base
machine equipment dealer or manufacturer for more
information on the availability of FOPS. Lack of proper
FOPS may result in injury or death.
•
NEVER operate the excavator without a proper
restraint (seat belt) system in place. Doing so can
create loss of control or ejection from cab.
•
NEVER operate the equipment while under the
influence of drugs, alcohol or other substances that
inhibit mental abilities or reaction time.
•
DO NOT process material with the attachment over
the operator’s cab. Doing so will result in severe
personal injury or death from falling debris.
•
NEVER remove any pins unless the attachment is
on the ground and blocked up, or serious injury or
death could result. Metal chips or debris may fly when
a connecting pin is struck. Use a brass drift when
striking pins and always wear protective clothing and
proper eye protection.
•
Clear all persons and equipment from the area of
operation and machine movement. NEVER move
loads over people or equipment. When viewing the
operation of the attachment, maintain a safe distance
of at least 75 feet (23 meters).
•
NEVER approach power lines with any part of the
machine. Keep clear at a minimum of 50 feet (16
meters).
•
DO NOT close the attachment on a structure and
reverse the excavator in an attempt to pull down
material.
•
Avoid tipping. The attachment will alter the lift
capacities of the base machine. DO NOT overload
the excavator or serious injury could result. Lift
capacities will vary if the base machine is not on level
ground. Lifting incorrectly can cause severe injury or
machine damage. Use the recommended excavator
counterweight. Use short slings and lift the load only
as high as necessary.