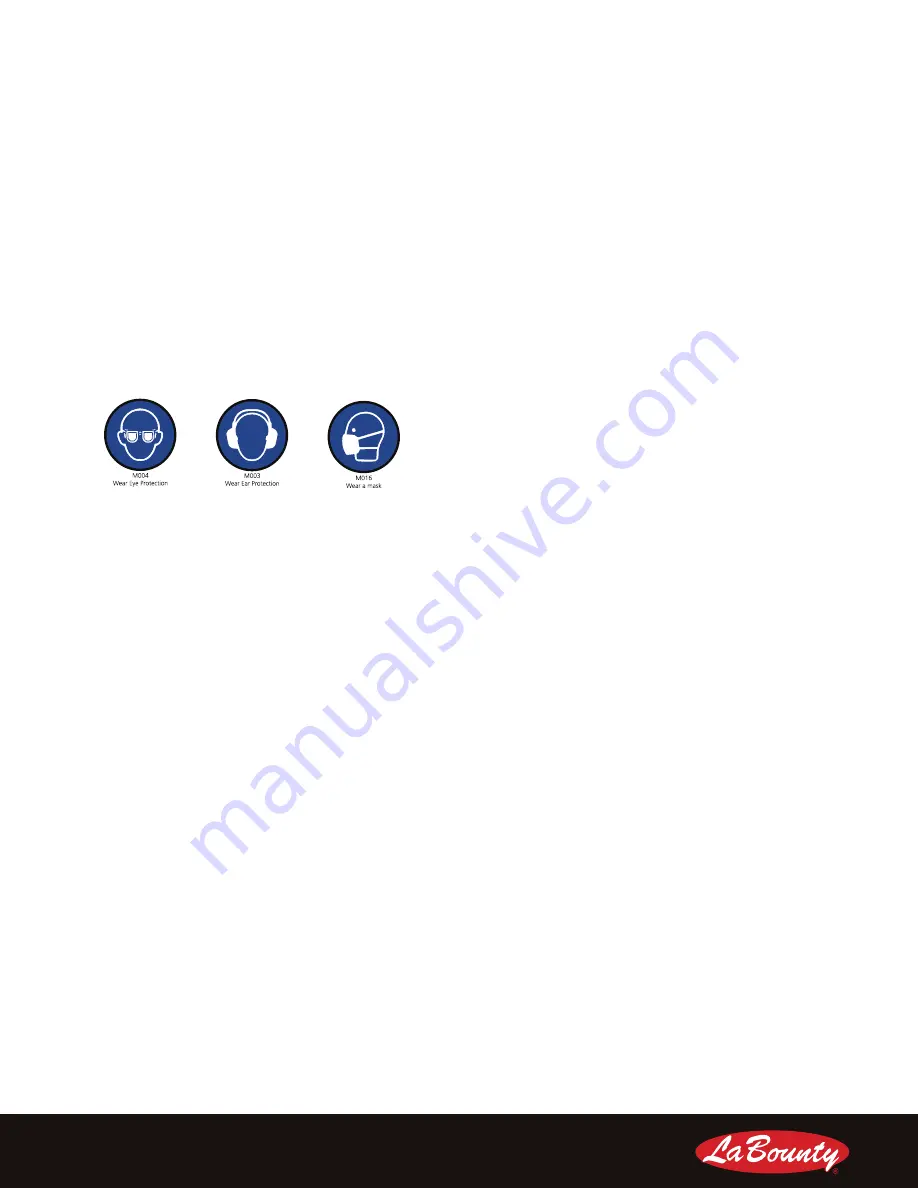
10 | MDG Operating & Maintenance Manual
OPERATION
BEFORE YOU START
Know Your Safety Program
•
Read and understand this manual and the base
machine manual.
•
Know the employer’s safety rules. Consult your
foreman for instructions and safety equipment.
•
Learn the traffic rules at the work site. Know the hand
signals used on the job and who is responsible for
signaling. Take signals from only
ONE
person.
•
Wear personal protection equipment. This includes
eye protection, hard hat, steel toe shoes, gloves,
hearing protection and respirator.
Know Your Equipment
•
Learn and test the function of all controls. If
malfunctions are found, shut the machine down and
report the malfunction for repair.
•
Be familiar with safety devices, indicators, warning
devices and caution instructions. They will alert you to
conditions that are hazardous.
•
Know the clearances in the work area.
Daily Safety Checks
•
Ensure all decals are installed and legible. Contact
LaBounty for replacements as required.
•
Have a
DAILY
safety dialog with all workers. Inform
them of any abnormal work that is planned. Remind
them of the safe working distance.
•
Clear the area.
ALWAYS
look out for others. In any
work area, people constitute a serious safety hazard.
Before operating, walk around the machine to ensure
no workers are next to, under or on it. Warn nearby
workers that you are starting up.
DO NOT
start up until
they are out of danger.
•
Check the location of cables, gas lines and water
mains before operation. Ensure work site footing has
sufficient strength to support the machine. When
working close to an excavation, position machine with
the propel motors at the rear.
•
Keep bystanders clear, especially before moving
the boom, swinging the upper structure, or traveling.
ALWAYS
be alert for bystanders in or near the
operating area.
SAFETY DEVICES
• Seat belts
• Canopies
• Safety decals
• Shields and guards
•
Flags and flares
• Barricades
• Signs and other
markings
• Warning lights
• Falling Objects
Protective Structures
(FOPS)
• Visual or audible
warning devices
General Rules For Safe Operation
•
KNOW
the capacity of the excavator and it’s
attachments.
DO NOT
overload or serious injury
could result. The attachment may have altered the
machine’s lift capabilities.
•
MDG is for sorting materials.
DO NOT
use for
unapproved purposes or warranty may be voided.
•
If MDG stalls during processing, scale back the
amount of material being processed at one time.
Overloading can cause overheating and has adverse
effects on the hydraulic system.
•
Cycle the MDG cylinder completely when processing.
Fully cycling MDG will allow hydraulic fluid to circulate
and prevents overheating.
•
Maintain a safe distance.
•
NEVER
leave MDG suspended or pass it over people,
occupied vehicles or buildings.
•
When working in confined spaces, keep watch on
exposed parts, such as cylinder rods and hoses, to
avoid damage.
•
Maintain at least 50 feet (15 meters) between MDG
and any nearby power lines.
• ALWAYS
lower MDG to the ground and turn the base
machine off when leaving the machine unattended.
•
DO NOT
close the jaws on a structure and reverse
the excavator in an attempt to pull down material. This
is dangerous and will damage the excavator and the
attachment.
•
DO NOT
alter factory preset hydraulics. This may void
the warranty.
•
DO NOT
shear high tensile steel, such as railroad
rail, spring steel, axles and some types of wire. Jaw
damage will result. This type of material breaks when
processed and can become a projectile which could
cause injury or death.
•
Ensure the connecting pins between the excavator
and the MDG are secured, as well as the wedge and
the security pin of the quick release hitch system.