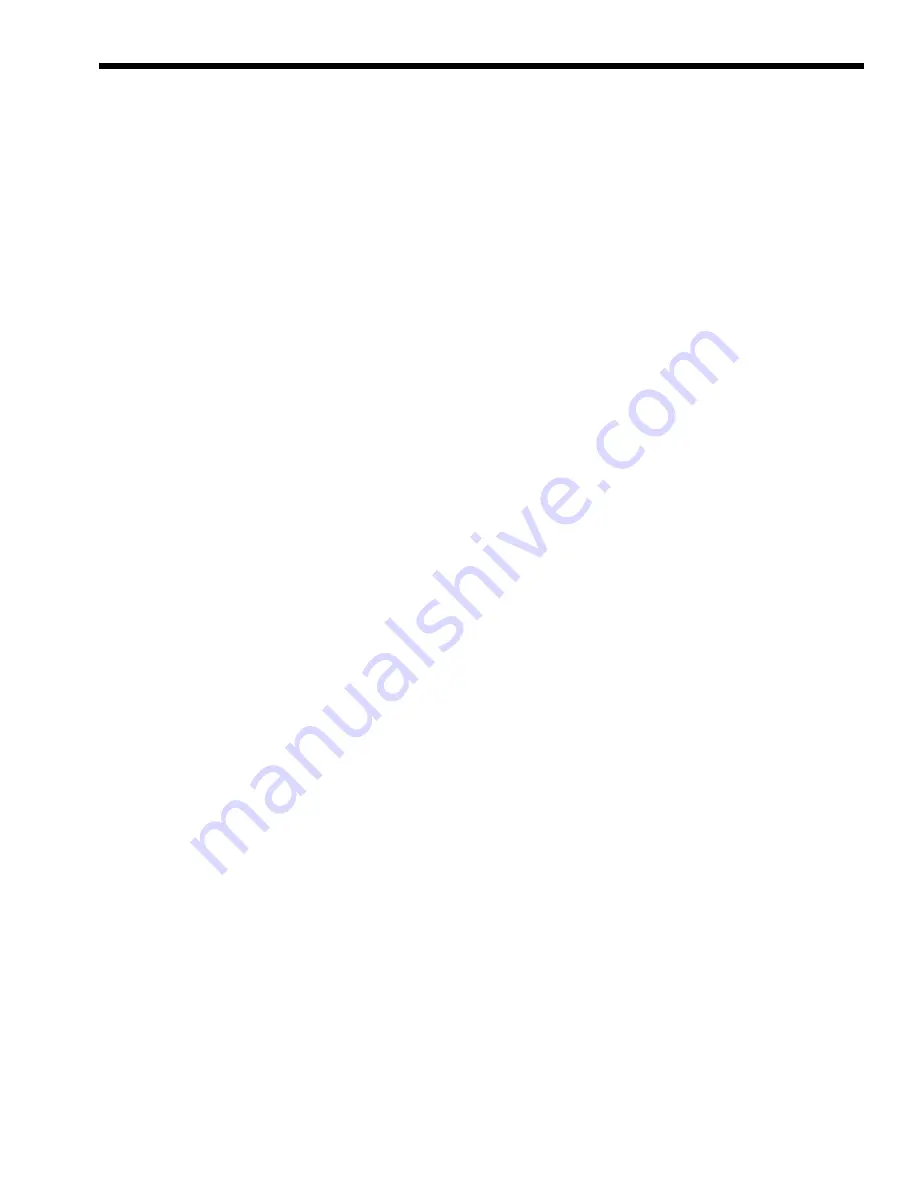
Rheos Boiler and Water Heater
Page 45
SECTION 8.
Trouble Shooting
8.1 Sequence of Operation
The Rheos appliance is a cold start appliance
that should start only on a call for heat from a tank
aquastat, room thermostat, zone valve end switch or
other space temperature control device.
1. Upon a call for heat,
(a) The internal pump will start. (Pump is
optionally mounted on unit.)
(b) The blower will begin a 15 second pre-
purge.
2. Following the prepurge cycle the hot surface
ignitor will heat and will begin a 7 second trial
for ignition. The unit is allowed three attempts
for ignition.
3. The gas valve will then be energized and low-
fire (50% of full fire) ignition will occur. The
unit will remain in a low-fire start-up period for 15
seconds.
4. After the low-fire start time is over, the unit
will be in normal operation firing rate and will
modulate based on the heating load via the
temperature controller settings and readings.
5. When the call for heat is complete, or the unit
reaches its setpoint temperature, the gas valve
will close, and the fan will continue to run for
its 30 second post-purge. If a pump time delay
is used, the pump will continue to run for the
specified amount of time (adjustable from 0.1 to
10 minutes).
8.2 Resolving Lockouts
There are many causes of lockouts. The three
most common causes are: (1) inadequate gas supply,
(2) poor combustion, (3) ignitor failure (4) combustion
air.
1. Inadequate gas supply: Before proceeding, ensure
that the gas supply has not been shutoff or the LP
tank (LP boilers) is not empty. Then, restart the
boiler and observe the operational cycle. After
the pre-purge time, the unit should light. If it
does not, consult the factory.
2. Poor Combustion: Poor combustion should be
suspected if there is a strong flue gas odor. The
odor may result from an improper gas/air ratio
(high or low O
2
or CO
2
). If an improper gas/air
ratio is suspected, consult the factory.
3. Ignitor failure: If the boiler goes through a
normal start cycle but combustion does not
occur, ignitor failure should be suspected. Check
the ignitor by unplugging the ignitor plug and
measuring the ignitor resistance. It should be
50-80 (
-
) ohms. If the resistance is not 50-80
ohms (
W
), replace the ignitor. If the resistance is
correct, reset the boiler and check for 120 VAC
at the ignitor plug during the start cycle. If there
is no voltage, replace the faulty ignitor wire
harness.
4. Inadequate combustion air: If the boiler goes
through a normal ignition cycle, and shuts off
after the blower ramps up to full speed, an
abnormal restriction in the air intake or exhaust
system should be suspected. Check the air filter
for buildup of debris and clean filter if necessary.
Inspect all exhaust venting and intake venting for
blockages. Remove any blockages and inspect
and replace any damaged vent sections. If the
unit still continues to lockout after igniting,
consult the factory.
Once the reason for the lockout has been
identified and resolved you can reset the unit by
pressing the manual reset button (see Detail A in
Figure 30. Control Panel).
8.3 Delayed Ignition - Possible Causes
8.3.1 High Lockup Pressure (LP
Appliances) - Occurs on Start-up
High lock up pressure is the most common
cause of delayed ignitions on LP fueled appliances. It
may result from an improper second stage regulator
selection or from a faulty regulator.
Lock up can be detected by measuring the gas
supply pressure to the appliance at the inlet pressure
port on the gas valve. The gas supply to the appliance
must be shut off before making any connections. To
check: use a water manometer or pressure gauge with
a scale reading of at least 25 in. W.C. or 15 oz/in
2
.
(6.2kPa). Attach the manometer to the gas valve inlet
pressure port. Turn on the gas supply. The Rheos
appliance is designed to operate with supply pressures
of 4-13 in. W.C. (2.3 - 7.5 oz/ in²) (0.1-3.2kPa). If
the supply pressure exceeds 13 in. W.C. (7.5 oz/ in²)
(3.2kPa) (with the appliance off) it is possible that this
may be the cause of the delayed ignitions and the inlet
pressure must be reset to between 4-13 in. W.C. (2.3
– 7.5 oz/in
2
) (0.1-3.2kPa). Restart the appliance and
then switch it off. If the inlet gas pressure exceeds 13
in. W.C. (7.5 oz/ in²) (3.2kPa) after the appliance is
switched off, correct the lock up problem.
8.3.2 Gas Valve Regulation
Gas valve regulation problems can also cause
delayed ignitions. If gas valve regulation problems
are suspected, consult the factory. Do not attempt field
adjustment or repair.
Summary of Contents for Rheos RHCH
Page 28: ...LAARS Heating Systems Page 28 Figure 20 Wiring Diagram Model 1200 Codes B and E...
Page 32: ...LAARS Heating Systems Page 32 Figure 24 Wiring Diagram Model 1200 Pump Mounted Codes B and E...
Page 53: ...Rheos Boiler and Water Heater Page 53 Figure 42 Electrical Components...
Page 57: ...Rheos Boiler and Water Heater Page 57...
Page 58: ...LAARS Heating Systems Page 58...