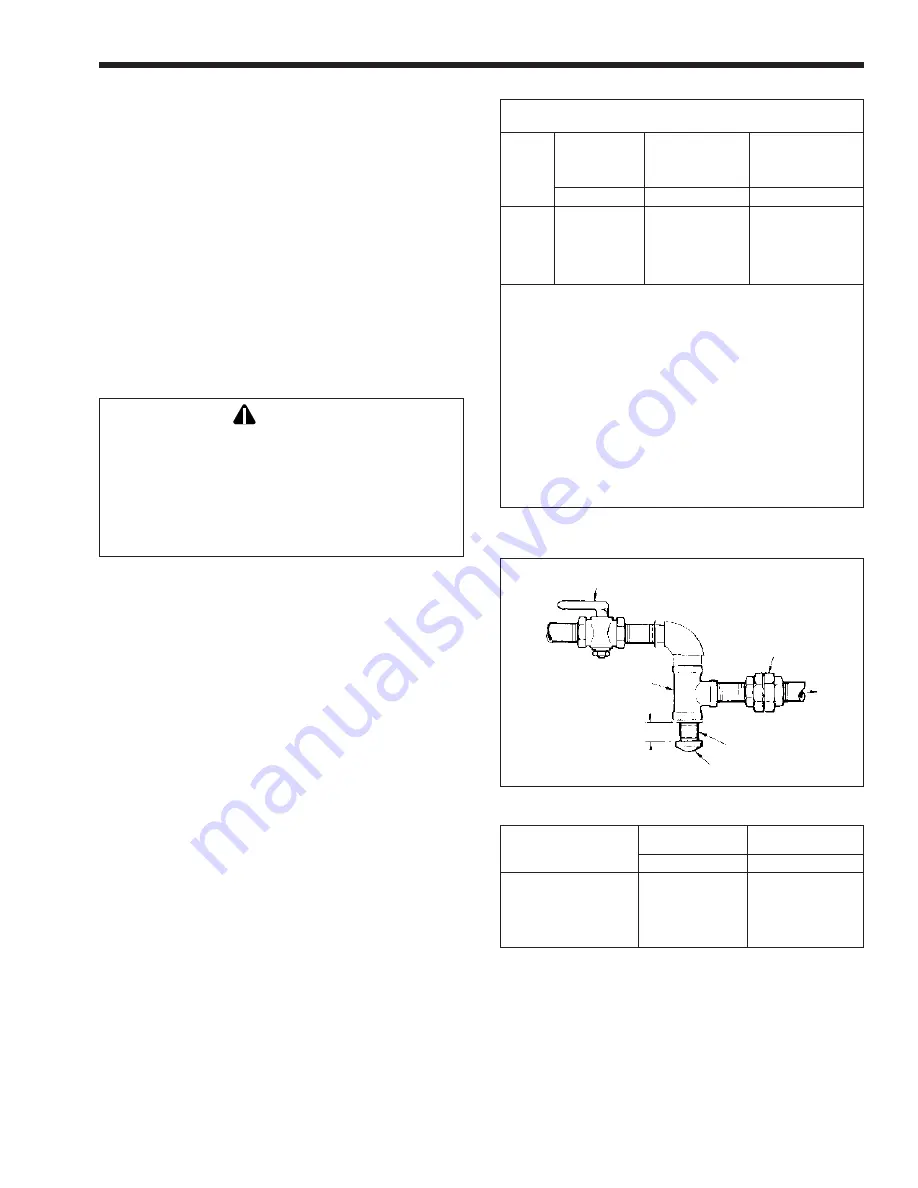
Mighty Therm VW - PW Volume Water Heaters
Page 15
2F-11. Thermal Circulation of Hot Water
in Cold Water Supply Lines
Under certain circumstances, thermal circulation
will occur in the cold water pipe supplying the water to
the heating system. This happens in a multi-story
building when the cold water pipe rises from its
connection to the system. To correct the problem, a
check valve in the cold water line supplying the heater
will prevent thermal circulation, and a small expansion
tank will permit heated water to expand without
popping off the relief valve.
2G. Gas Supply and Piping
2G-1. General Instructions
Review the following instructions before
continuing the installation.
WARNING
The conversion of heaters from natural gas to
propane gas, or propane to natural, must be done
by a professional service technician. Laars provides
kits and detailed instructions for converting the
heater. Changing burner and/or pilot orifices is
prohibited. The installer must add and sign a gas
conversion tag when the conversion is made.
1.
Gas piping installation must be in accordance
with the latest edition of ANSI Z223.1. In
Canada, the installation must be in accordance
with CAN1-B149.1 or .2 and all local codes that
apply.
2.
Check the rating plate to make sure the heater is
fitted for the type of gas being used. Laars
heaters are normally equipped to operate below a
2000 foot (609 m) altitude. Heaters equipped to
operate at higher altitudes have appropriate
stickers or tags attached.
3.
If a gas pressure regulator is required, the
installation must be in accordance with the latest
edition of ANSI Z223. In Canada, the installation
must be in accordance with CAN1-B149.1 or .2
and all local codes that apply.
4.
The figures in Table 5 should be used to size the
gas piping from the gas meter to the heater.
5.
Install a sediment trap (drip leg) ahead of the gas
controls (see Figure 24 ). Fit the trap with a
threaded cap which can be removed for cleaning.
6.
Install a manual gas shutoff valve for service and
safety. Check the local codes.
7.
Disconnect the heater and its individual shutoff
valve from the supply gas system during pressure
test of the system at pressures higher than 1/2 psi
(3.4 kPa).
8.
Gas supply pressures to the heater are listed in
Table 6.
Figure 24. T-Fitting and sediment trap.
MANUAL SHUT-OFF
VALVE
GAS
SUPPLY
INLET
T-FITTING
3" (76 mm)
MIN.
UNION
NIPPLE
CAP
TO
BOILER
INLET
NOTE: The heater and all other gas appliances
sharing the heater gas supply line must be firing at
maximum capacity to properly measure the inlet
supply pressure. Low gas pressure could indicate
an under-sized gas meter and/or obstructed gas
supply line.
9.
Do not exceed the maximum inlet gas pressures
specified. Excessive pressure will result in
Distance from Gas Meter or Last Stage Regulator
0-100 feet
100-200 feet
200-300 feet
0-30 m
30-60 m
60-90 m
Boiler
Nat.
Nat.
Nat.
Size
in.
mm
in.
mm
in.
mm
175
1
25
1¼
32
1¼
32
250
1¼
32
1¼
32
1½
38
325
1¼
32
1½
38
1½
38
400
1¼
32
1½
38
2
51
Notes:
1. These numbers are for natural gas (0.65 Sp. Gr.) and
are based on
½
inch (13mm) water column pressure
drop. Check supply pressure with a manometer, and
local code requirements for variations. For liquefied
petroleum gas, reduce pipe diameter one size, but
maintain a
½
inch (13mm) minimum diameter.
2. Check supply pressure and local code requirements
before preceding with work.
3. Pipe fittings must be considered when determining gas
pipe sizing.
4. For propane gas: Reduce pipe diameter one size, but
maintain a
¾
inch (19mm) minimum diameter.
Table 5. Natural Gas and Propane,
Pipe Size Requirements.
Supply Pressure
Natural Gas
Propane Gas
Water Column
in.
mm
in.
mm
Minimum
6.5
165
11
279
See Rating Plate
Maximum
9
229
14
356
Table 6. Gas Supply Pressure Requirements.