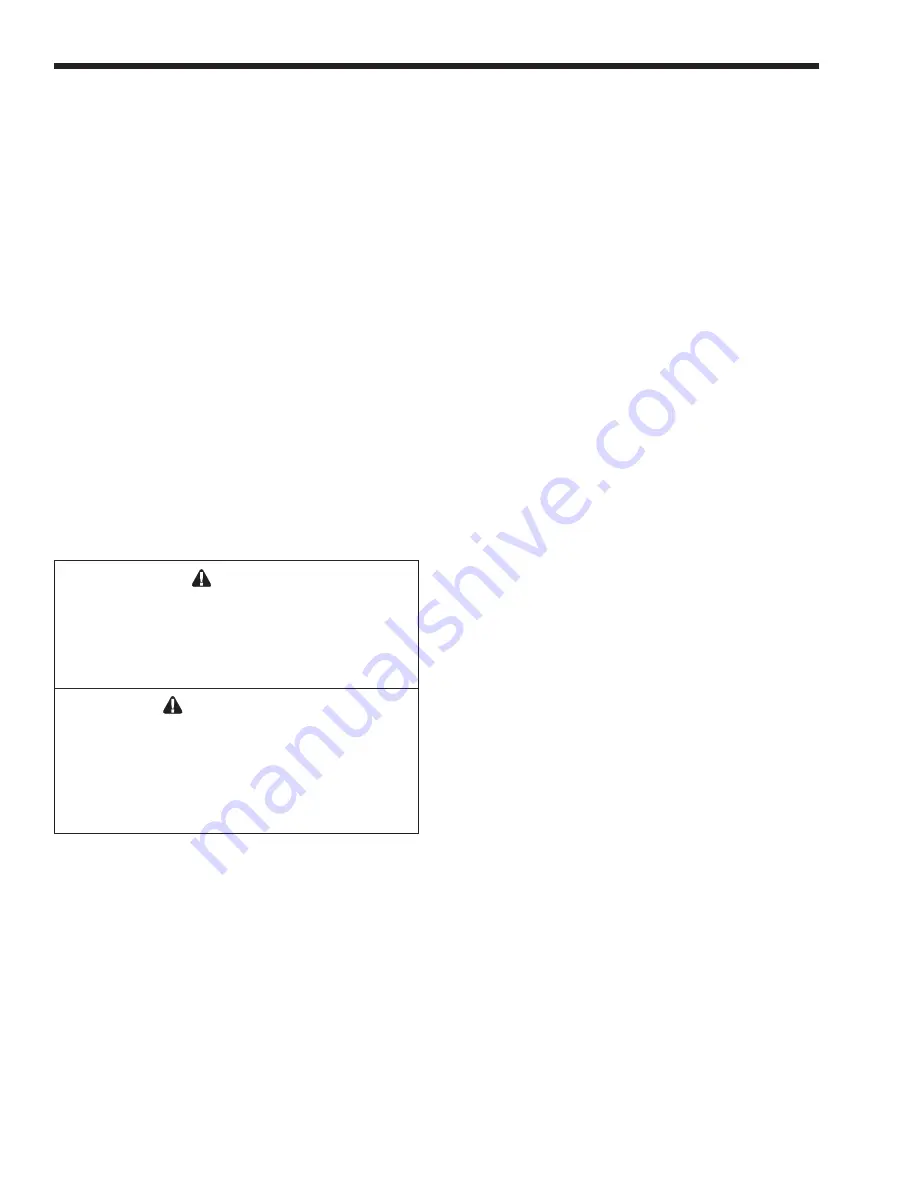
Laars Heating Systems
Page 20
SECTION 6.
Operating Instructions
6.1 Filling the Water Heater System
1. Ensure the system is fully connected. Allow
system to fill slowly.
2. Start up water heater according to the procedure
in this manual.
3. After placing the unit in operation, the ignition
system safety shutoff device must be tested.
First, shut off the manual gas valve, and call
the unit for heat. After the pre-purge and ignitor
heat-up time, the main gas terminals will be
energized, attempting to light, for seven (7)
seconds, and then will de-energize. The unit will
attempt to light two more times, and then will go
into lockout mode. Second, turn the power off
and then on again, open the manual gas valve
and allow the unit to light. While the unit is
operating, close the manual gas valve and ensure
that power to the main gas valve has been cut.
Important: The installer is responsible for identifying
to the owner/operator the location of all emergency
shutoff devices.
WARNING
Do not use this appliance if any part has been
under water. Immediately call a qualified service
technician to inspect the appliance and to replace
any part of the control system and any gas control
that may have been under water.
AVERTISSEMENT
N’utilisez pas cet appareil si l’une de ses pièces est
passée sous l’eau. Appelez tout de suite un technicien
en entretien et en réparation pour inspection de
l’appareil et remplacement des pièces du système de
commande, et des pièces de commande du circuit
gaz, qui sont passées sous l’eau.
6.2 Operating Temperature Control
To utilize the water heater's on-board controller,
be sure to have the “Local/Remote” selector switch to
“Local”. Set the controller to the desired operating set
point.
High limit should be set 40-50°F (4-10°C) higher
than the controller, to avoid nuisance lockout of the
manual reset high limit.
Maximum tank temp. allowed is 150°F (66°C).
6.3 External Water Heater Operations
If controlling the stages of the MS-080 from
an external source (multiple water heater control,
BAS, etc) the “Local/Remote” selector switch above
the terminal strip must be placed in the “Remote”
position. In this mode, the controller that is mounted
on the MS-080 will no longer have control of the unit.
The 24V from the unit waits at the input terminal, and
the external control switches this 24V from the input.
6.4 Sequence of Operation
The pump time delay relay will receive a signal
to initiate. The pump terminals on the field-wiring
terminals strip will energize a pump.
Once the water flow switch makes, if all of the
safety interlocks are closed, the ignition module
will energize the blower for a 15-second pre-purge,
followed by a 40-second period to allow the ignitor to
heat.
The ignition control energizes the blower. The
blower pressurizes the air box (which supplies air to
the burners) and closes the normally-open contact
on the airflow pressure switch. The blocked vent
pressure switch senses the pressure in the exhaust
plenum. This switch opens if the pressure is excessive
(as an indicator of a blocked vent). When these two
pressure switches are closed, voltage is sent to the
PSW terminal on the ignition control, which allows the
ignition module to proceed with the ignition sequence.
If the airflow proving circuit is not proven,
ignition module will lock out. Section 6.5
describes
the result of air flow faults in more detail.
When the ignition control gets the signal at the
PSW terminal, it will energize its MV terminal, which
sends power to the main valve.
After a 7-second trial for ignition, the ignitor
switches to flame sense mode. If a flame is not
detected, the gas valve will close and the ignition
module will attempt ignition again (up to two more
times, for a total of three attempts.) If all three
attempts fail, the ignition control will lock out.
If flame is sensed, the burner will continue to
fire as long as there is a call for heat, and none of the
safety circuit is interrupted.
If there is a loss of flame signal during a
successful firing sequence, the ignition control will
remove power from the gas valve, and then attempt to
light up to two more times. If successful, the Mighty
Stack will fire normally. If unsuccessful, the ignition
control will lock out.
When the call for heat is satisfied, the gas
valve(s) closes, and the blower starts a 45 second post-
purge. The Mighty Stack pump time delay relay will
continue to run for the time delay period (dialed by the
user, 0.1 to 10 minutes).
6.5 Ignition Control Reaction to Air Flow /
Blocked Vent Pressure Switch
Air flow and blocked vent status are continuously
monitored by the Mighty Stack ignition control, at the
control’s PSW terminal.
At the start of an ignition sequence, if the ignition
control sees power at PSW for 30 seconds, but the
combustion blower has not yet been energized by the
Summary of Contents for Mighty Stack MS-080
Page 14: ...Laars Heating Systems Page 14 Figure 4 Venting...
Page 19: ...Mighty Stack Page 19 Figure 7 Wiring Diagram ON OFF Water Heater...
Page 30: ...Laars Heating Systems Page 30 Figure 9 Combustion Chamber Components...
Page 31: ...Mighty Stack Page 31 Figure 10 Jacket Components...
Page 32: ...Laars Heating Systems Page 32 Figure 11 Heat Exchanger Components...
Page 33: ...Mighty Stack Page 33 Figure 12 Gas Train Components...
Page 34: ...Laars Heating Systems Page 34 Figure 13 Control Panel Components...
Page 35: ...Mighty Stack Page 35 Figure 14 Pump Assembly Components...