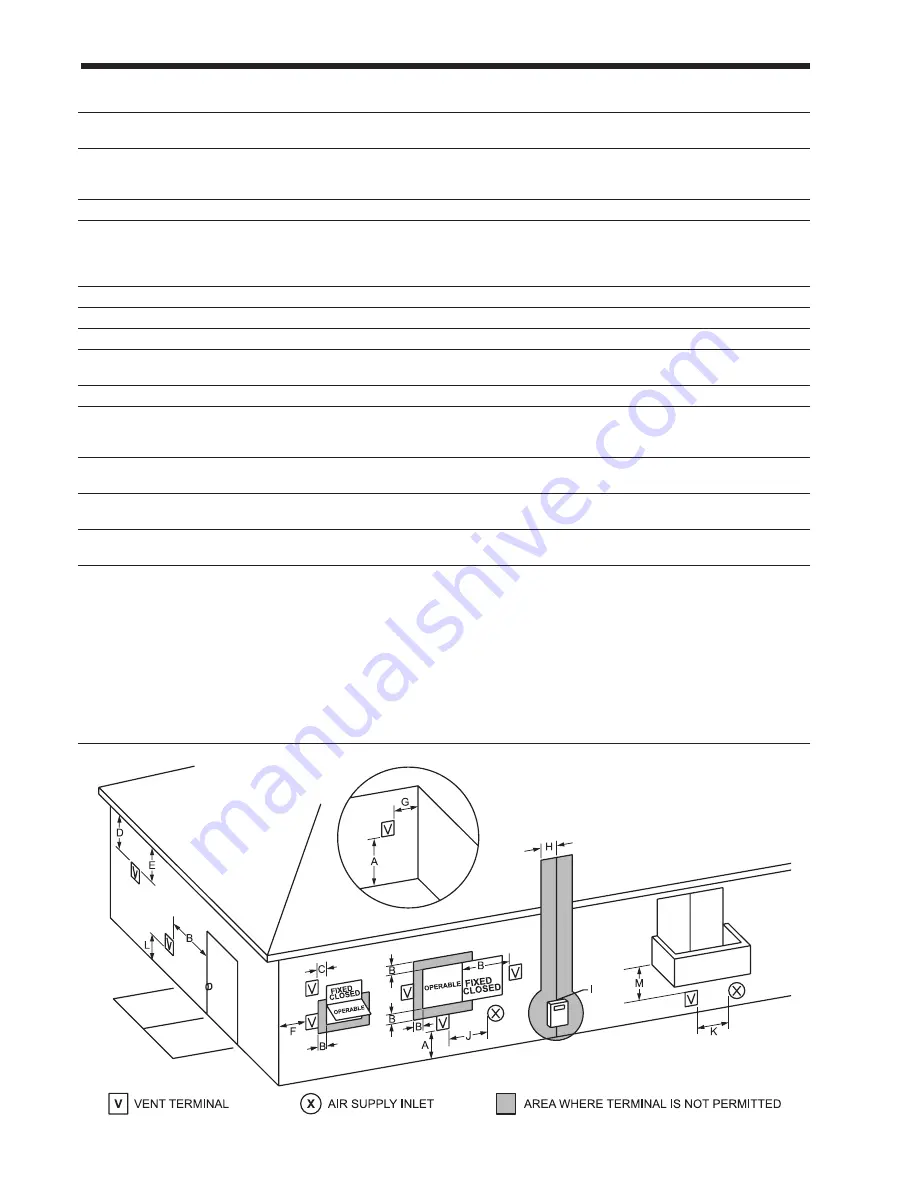
LAARS Heating Systems
Page 16
*When vent terminal is less than 10 feet (3 m) horizontally
from a forced air inlet, the terminal must be at least 3 feet
(0.9 m) above the air inlet. (US only)
Figure 5. Combustion Air and Vent Through Side Wall
U.S. Installations (see note 1)
Canadian Installations (see note 2)
A=
Clearance above grade, veranda, porch,
12 inches (30 cm)
12 inches (30 cm)
deck, or balcony
See note 6
See note 6
B=
Clearance to window or door that may be
Direct vent only: 12 inches (30 cm);
36 inches (91 cm)
opened
Other than Direct vent: 4 ft (1.2m) below or to
side of opening; 1 ft (30 cm) above opening
C=
Clearance to permanently closed window
See note 4
See note 5
D=
Vertical clearance to ventilated soffit located
above the terminal within a horizontal
See note 4
See note 5
distance of 2 feet (61 cm) from the center
line of the terminal
E=
Clearance to unventilated soffit
See note 4
See note 5
F=
Clearance to outside corner
See note 4
See note 5
G=
Clearance to inside corner
See note 4
See note 5
H=
Clearance to each side of center line
3 feet (91 cm) within a height 15 feet
extended above meter/regulator assembly See note 4
above the meter/regulator assembly
I=
Clearance to service regulator vent outlet
See note 4
3 feet (91 cm)
J=
Clearance to nonmechanical air supply
Direct vent only: 36” (91cm)
inlet to building or the combustion air inlet Other than Direct vent: 4 ft (1.2m) below
36 inches (91 cm)
to any other appliance
or to side of opening; 1 ft (30 cm) above opening
K=
Clearance to a mechanical air supply inlet 3 feet (91 cm) above if within 10 feet (3 m)
6 feet (1.83 m)
horizontally
L=
Clearance above paved sidewalk or paved
Vent termination not allowed in this location
7 ft (2.1 m)
driveway located on public property
for category IV appliances.
See note 5
M=
Clearance under veranda, porch, deck,
See note 4
12 inches (30 cm)
or balcony
See note 5
Notes:
1. In accordance with the current ANSI Z223.1 / NFPA 54 National Fuel Gas Code.
2. In accordance with the current CAN/CSA-B149 Installation Codes.
3. Permitted
only if veranda, porch, deck, or balcony is fully open on a minimum of two sides beneath the floor.
4. For clearances not specified in ANSI Z223.1 / NFPA 54, clearance is in accordance with local installation codes and the
requirements of the gas supplier.
5. For clearances not specified in CAN/CSA-B149, clearance is in accordance with local installation codes and the requirements of the
gas supplier.
6. IMPORTANT: All terminals must be placed so that they remain a minimum 12” above expected snow line. Local codes may have
more specific requirements, and must be consulted.