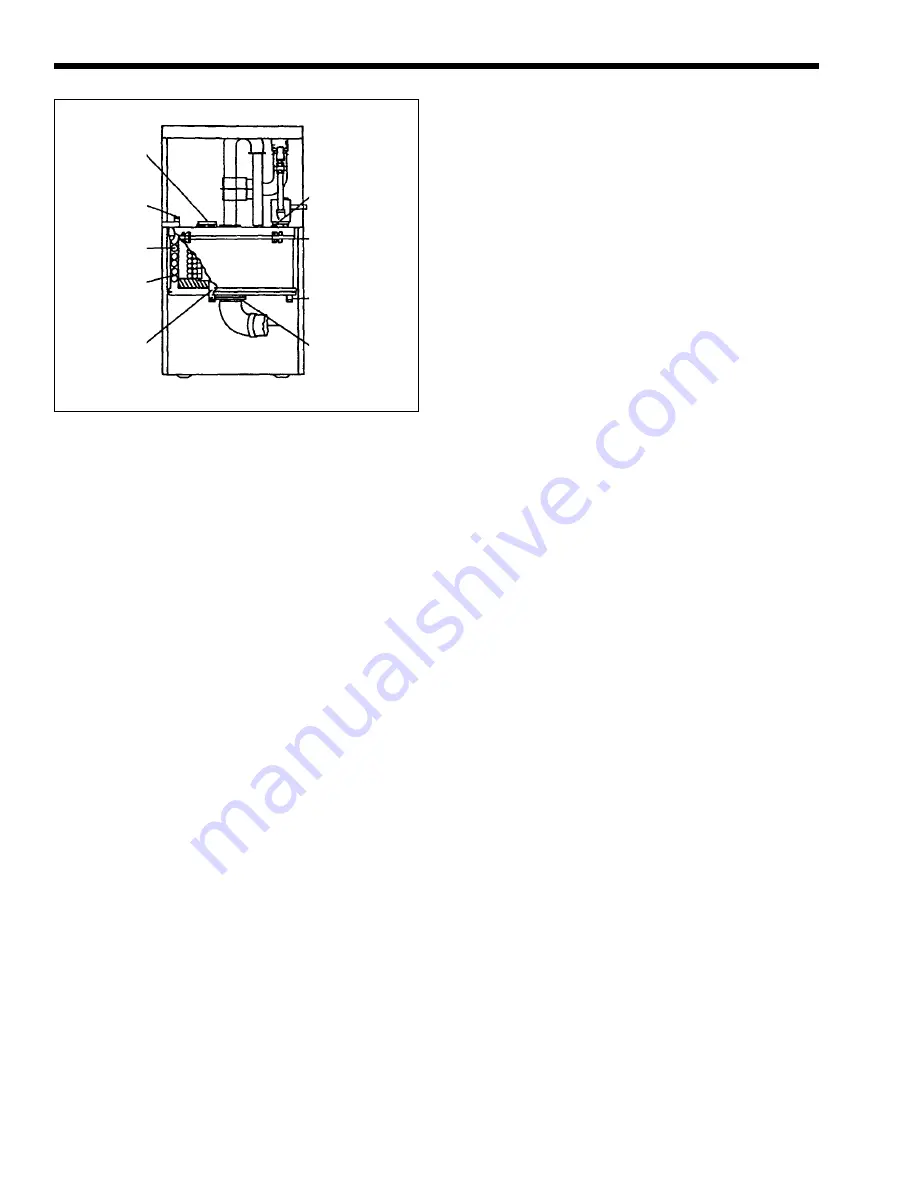
Page 10
LAARS Heating Systems
1D. Cleaning the Combustion
Chamber Coil
Note
: In normal operation this procedure is
seldom required. Should it prove necessary, the
following procedure is used to access the coil for
cleaning.
1.
Turn off gas and electrical power to unit.
2.
Remove upper and lower front covers.
3.
Disconnect flue and combustion air pipes and
remove jacket top.
4.
Remove flue pipe assembly by disconnecting
from outer shroud.
5.
Remove mixer tube and blower assembly.
6.
Remove igniter and burner (flameholder).
7.
Fit mask and eye protection.
8.
Fit mask and eye protection.
9.
Locate vacuum hose at flue outlet of outer
shroud and start vacuum cleaner.
10.
Bend air chuck extension 90° at a point about
2-3" from end.
Insert air chuck extension through burner hole in
upper head. Direct end of extension toward fins of
heat exchanger and blow off accumulated residue.
Methodically move up and down and completely
around the heat exchanger. After completion of this,
remove the extension from the burner hole and inspect
the condition of the heat exchanger with a flashlight
and inspection mirror. If there are areas on the heat
exchanger that still have some residue, repeat the
process on those areas until the heat exchanger is
clean.
Figure 8. Disassembly.
After the heat exchanger is clean, remove the
vacuum cleaner from the outer shroud flue outlet and
stop vacuum cleaner.
Carefully inspect the seal between the outer
shroud and the upper head and the joint in the outer
shroud. If there is any evidence of leakage from either
of these joints, clean off the silicone in that area and
prepare the surface for resealing. Commercially
available oven cleane is an appropriate cleaning agent.
Reseal the affected areas witih silicone, reassemble all
parts in the reverse order and check boiler operation.
1E. Diverting Valve
The diverting valve is a thermostatically
controlled device which keeps the primary heat
exchanger (H-X) from operating in the condensing
mode. When return water from the storage tank or the
system is below 130°F (54°C) the diverting valve
recycles a portion of the outlet water from the primary
H-X back to the primary H-X inlet so that the
minimum temperature required to prevent
condensation on the primary H-X is maintained at
160°F (71°C). The thermostat element is similar to
those used in large industrial engines.
To change the thermostatic element, valve off
the unit and turn off electrical power. Open boiler
drain to relieve pressure and close again. Remove the
cap screws (3) and remove top of valve. Remove and
replace the element (with barrel up), spring and sealing
disc. Place O-ring under valve top and replace top.
Secure with cap screws and tighten. Turn on valves
and bleed air from the top of the diverting valve. Turn
on electrical power and restart unit.
1F. Safety Limit Switch
The Safety Limit Switch has a fixed set point of
245ºF (118°C). It has a manual reset button which
may be reset at temperatures below 240ºF (116°C).
To replace the switch, shut off the 120 volt
power and valve off the unit. Drain a gallon of water
from the boiler and remove the 3/8 NPTM fitting
which seals the capillary. Remove the two screws
which hold the switch to the side panel, remove the
switch and unplug the switch wires. Install the
replacement in the reverse order, open isolation valves
and bleed air from the diverting valve petcock. Switch
on 120 volt power and restart unit.
1G. Boiler Control
The boiler control controls the combustion
process, the gas valve, the igniter, the blower, and the
unit pump.
It provides blower prepurge as well as burner
flame sensing. When replacing the boiler control all
plugs are color coded and it is not possible to miswire
the control. See sequence of operation for operating
details.
ECONOMIZER
RETAINERS (4)
OUTER SHROUD
CLAMPS (4)
COLD WATER
INLET
PLASTIC FLANGE,
(4) NUTS
COMBUSTION
COIL
MANIFOLDS
ECONOMIZER
OUTLET
ECONOMIZER
INNER
SHROUD
MANIFOLD
DRAIN