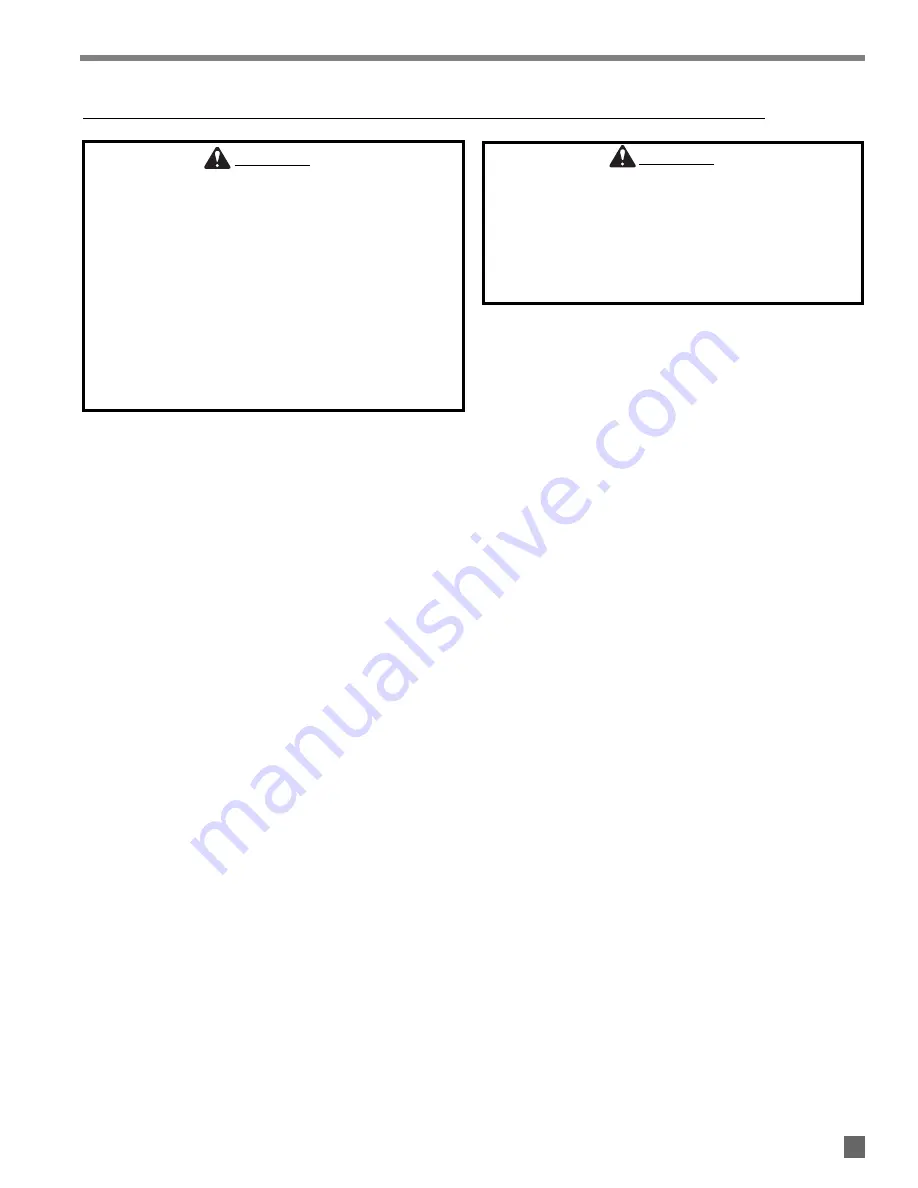
1.
Read all safety precautions and follow L. B. White
recommendations when installing this heater. If
during the installation or relocating of heater, you
suspect that a part is damaged or defective, call a
qualified service agency for repair or replacement.
2.
Make sure the heater is level and properly positioned
before use. Observe and obey all minimum safe
distances of the heater to the nearest combustible
materials. Safe distances are given on the heater
dataplate and on page 4 of this manual.
3.
This heater may be installed either indoors or
outdoors. For outdoor installations, only the following
air distribution devices may be used:
-- 43.7 cm Dia. x 3.66 m Duct: Part #22841
-- End Diffuser: Part #23054
DO NOT USE ANY OTHER LENGTH OF DUCTWORK OR
FIELD FABRICATED DUCT, TARPS, STOVE PIPE, ETC.
ON THIS HEATER.
4.
The heater’s gas pressure regulator (with pressure
relief valve) must be protected from adverse weather
conditions (rain, ice, snow) as well as from building
materials (tar, concrete, plaster, etc.) which can affect
safe operation and could result in property damage or
injury.
5.
Heaters used in the vicinity of combustible tarpaulins,
canvas, plastics, wind barriers, or similar coverings
shall be located at least 3 meters from the coverings.
The coverings shall be securely fastened to prevent
ignition or upsetting of the heater due to wind action
on the covering or other material.
6.
Check all connections for gas leaks using approved
gas leak detectors. Gas leak testing is performed as
follows:
-- Check all pipe connections, hose connections,
fittings and adapters upstream of the gas control
with approved gas leak detectors.
-- In the event a gas leak is detected, check the
components involved for cleanliness and proper
application of pipe compound before fur ther
tightening.
-- Fur thermore tighten the gas connections as
necessary to stop the leak.
-- After all connections are checked and any leaks
are stopped, turn on the main burner.
-- Stand clear while the main burner ignites to
prevent injury caused from hidden leaks that could
cause flashback.
-- With the main burner in operation, check all
connections, hose connections, fittings and joints
as well as the gas control valve inlet and outlet
connections with approved gas leak detectors.
-- If a leak is detected, check the components
involved for cleanliness in the thread areas and
proper application of pipe compound before further
tightening.
-- Tighten the gas connection as necessary to stop
the leak.
-- If necessary, replace the parts or components
involved if the leak cannot be stopped.
-- Ensure all gas leaks have been identified and
repaired before proceeding.
7.
A qualified service agency must check for proper
operating gas pressure upon installation of the
heater.
8.
Light according to instructions on heater or within
owner's manual.
9. The heater must have the proper regulator for the
application.The gas pressure regulator supplied on
this heater is approved for both propane and natural
gas use. Contact your gas supplier, or the L.B. White
Co., Inc. if you have any questions.
10. This heater is configured for use for L.P. gas vapor
withdrawal. Do not use the heater in an L.P. gas liquid
withdrawal system or application. If you are in doubt,
contact the L.B. White Co., Inc.
11. The heater must be installed so as not to interfere
WARNING
Fire and Explosion Hazard
Can cause property damage, severe injury or death
■
To avoid dangerous accumulation of fuel gas, turn
off gas supply at the heater service valve before
starting installation, and perform gas leak test after
completion of installation.
■
Do not force the gas control knob. Use only your
hand to turn the gas control knob. Never use
any tools. If the knob will not operate by normal hand
pressure the gas control valve should be replaced by
a qualified service technician. Force or attempted
repair may result in fire or explosion.
7
Installation Instructions
GENERAL
WARNING
Fire and Explosion Hazard
■
Do not use open flame (matches, torches, candles,
etc.) in checking for gas leaks.
■
Use only approved leak detectors.
■
Failure to follow this warning can lead to fires or
explosions.
■
Fires or explosions can lead to property damage,
personal injury or death.