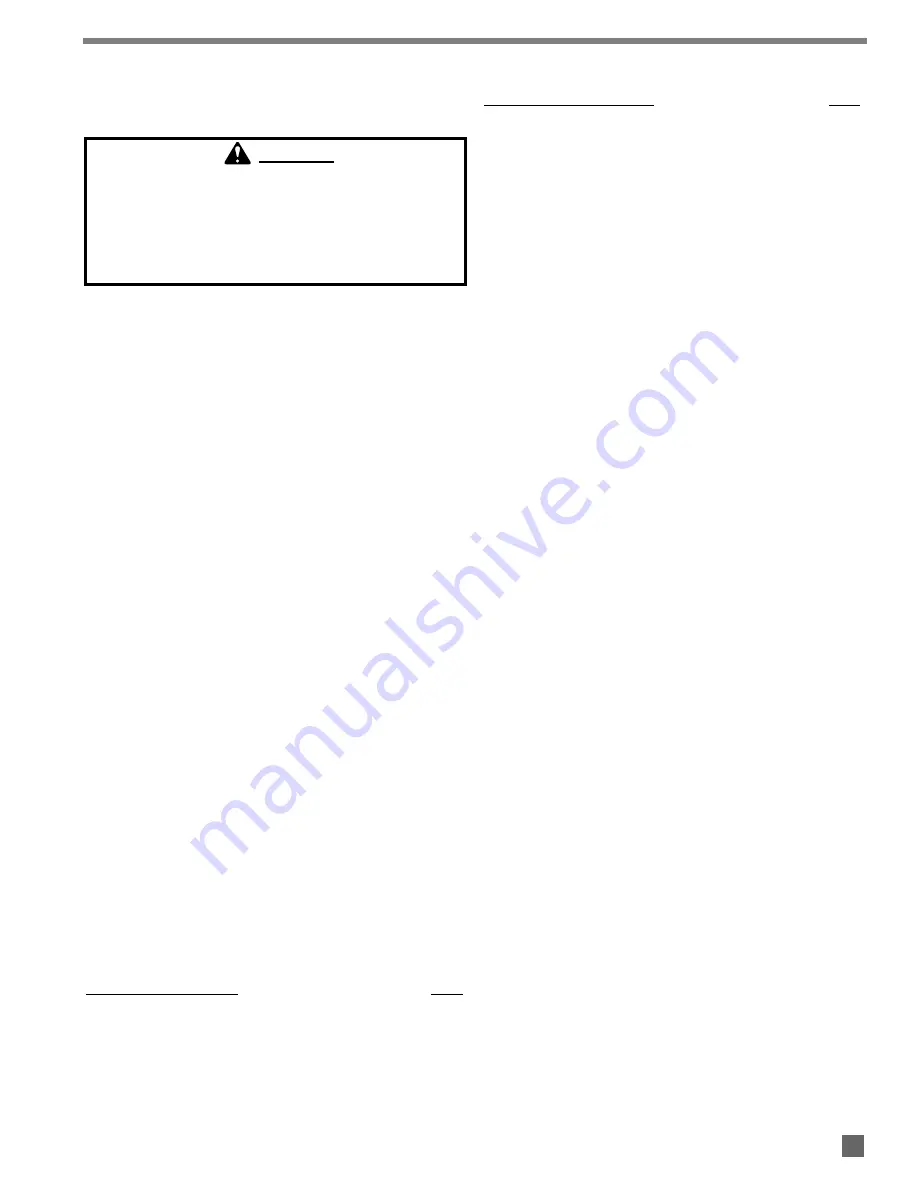
READ THIS ENTIRE SECTION BEFORE BEGINNING
TO TROUBLESHOOT PROBLEMS.
The following troubleshooting guide provides systematic
procedures for isolating equipment problems. This guide is
intended for use by a QUALIFIED GAS HEATER SERVICE
PERSON. DO N
NOT AATTEMPT TTO S
SERVICE TTHESE H
HEATERS
UNLESS YYOU H
HAVE B
BEEN PPROPERLY TTRAINED.
TEST EEQUIPMENT R
REQUIRED
The following pieces of test equipment will be required to
troubleshoot this system with minimal time and effort.
• Digital M
Multimeter - for measuring AC and DC voltage and
resistance.
• Low PPressure G
Gauge - for checking inlet and outlet
pressures at the gas control valve against dataplate
rating.
■
Visually inspect equipment for apparent damage.
■
Check all wiring for loose connections and worn
insulation.
Refer to the system operation sequence in this section to
gain an understanding as to how the equipment operates
during a call for heat.
Understanding the sequence of operation of the ignition
module and related components is important as it relates to
problem solving.
The ignition control module is self-diagnostic. The red light
(LED) located within the selector switch will flash a specific
light pattern depending upon the problem which is
diagnosed. To effectively use the flow charts, you must first
identify what the problem is by the light pattern of the
diagnostic light. If the light is flashing, the flash pattern will
be followed by a pause and then a repeat of the flash
pattern until the problem is corrected.
The red light will only be on when the selector switch is
positioned to HEAT and the thermostat is set above room
temperature. The light will not be on when the selector
switch is positioned to VENT.
Heating M
Mode PProblems
Page
Red light is steady on. No flash pattern. . . . . . . . . . . . . . 21
Red light light is not on. . . . . . . . . . . . . . . . . . . . . . . . . . . . 21
Red light is flashing:
A. One Time. . . . . . . . . . . . . . . . . . . . . . . . . . . . 22
B. Two Times . . . . . . . . . . . . . . . . . . . . . . . . . . . 23
C. Three Times . . . . . . . . . . . . . . . . . . . . . . . . . 24
D. Four Times . . . . . . . . . . . . . . . . . . . . . . . . . . 25
E. Five Times. . . . . . . . . . . . . . . . . . . . . . . . . . . 25
Ventilation M
Mode PProblems
Page
A. Motor Does Not Run . . . . . . . . . . . . . . . . . . . . . . . . . . . 25
B. Motor “Hums,” Does Not Run . . . . . . . . . . . . . . . . . . . 25
Components should be replaced only after each step has
been completed and replacement is suggested in the flow
chart. Refer to the Servicing sections as necessary to
obtain information on disassembly and replacement
procedures of the component once the problem is identified
by the flow chart.
DIRECT IGNITION OPERATION SEQUENCE:
-- The thermostat calls for heat.
-- Line voltage is sent to selector switch.
-- Red light. on selector switch is illuminated.
-- Selector switch sends line voltage to the transformer to . .
ignition control.
-- Transformer reduces line voltage to 24 volts which is sent
to ignition control.
-- Ignition control module performs self safety check.
-- Internal components are tested.
-- Air proving circuit is checked.
-- Ignition control module begins ignition trial sequence.
-- Ignition control module sends 24 volts to air proving switch.
-- Fan motor starts.
-- Air proving switch closes and 24 volts are returned to the
ignition control module.
-- Ignition control module sends high voltage to the igniter
electrode.
-- Igniter sparks.
-- Ignition control module sends 24 volts to the gas control
valve through the high limit switches.
-- Gas control valve opens.
-- Ignition occurs.
-- Igniter continues to spark until flame proving
occurs.
-- Ignition spark is cut off.
-- Gas valve stays open.
-- Room warms to desired temperature.
-- Thermostat is satisfied.
-- Heater shuts down.
-- Process starts again on a call for heat.
IIG
GN
NIITTIIO
ON
N FFAAIILLU
UR
REE S
SEEQ
QU
UEEN
NC
CEE::
-- Trial for ignition takes approximately 10 seconds.
-- If ignition module does not sense a flame within the ignition
trial,
the module goes into safety lockout (3 flash pattern.)
-- Gas valve closes.
-- Ignition spark shuts off.
-- Fan motor stops.
-- To retry for ignition, the systems must be reset:
-- Turn the thermostat down and then up to call for
heat
or unplug heater and plug it back in or
-- Position selector switch to off and then back to
on.
20
Troubleshooting Information
WARNING
■
This heater can start at any time.
■
Troubleshooting this system may require operating the
unit with line voltage present and gas on. Use extreme
caution when working on the heater.
■
Failure to follow this warning may result in property
damage, personal injury or death.
Summary of Contents for Premier TS170
Page 2: ......