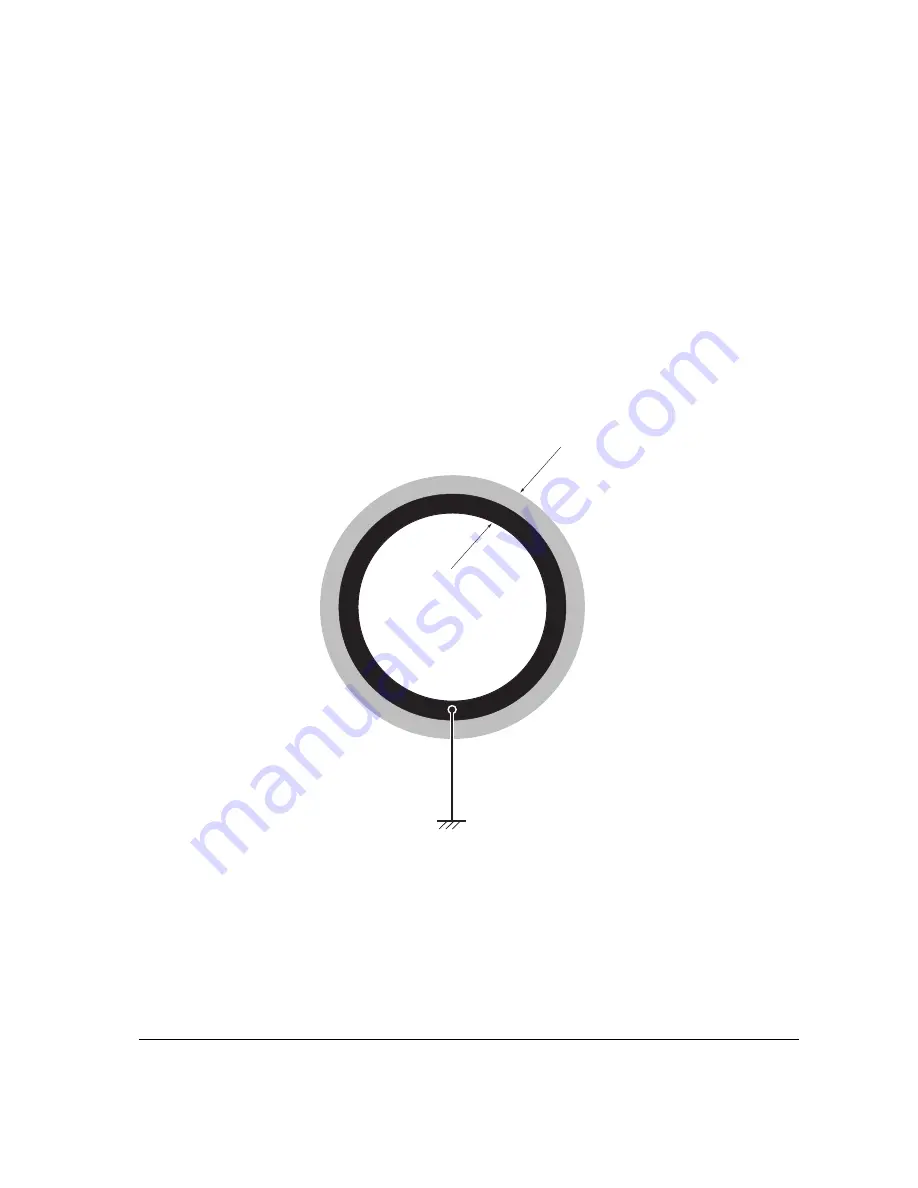
4-5
FS-1010
(1) Main charging
Photo conductive drum
The durable layer of organic photoconductor (OPC) is coated over the aluminum cylinder base.
The OPC tend to reduce its own electrical conductance when exposed to light. After a cyclic process
of charging, exposure, and development, the electrostatic image is constituted over the OPC layer.
Since the OPC is materialized by resin, it is susceptible to damage caused by sharp edges such as a
screwdriver, etc., resulting in a print quality problem. Also, finger prints can cause deterioration of
the OPC layer, therefore, the drum (in the process unit) must be handled with care. Substances like
water, alcohol, organic solvent, etc., should be strictly avoided.
As with all other OPC drums, the exposure to a strong light source for a prolonged period can cause
a print quality problem. The limit is approximately 500 lux for less than five minutes. If the drum
(process unit) remains removed form the printer, it should be stored in a cool, dark place.
Figure 4-1-3 Photo conductive drum
Aluminum base cylinder
Photo conductive layer
Summary of Contents for Ecosys FS-1010
Page 1: ...SERVICE MANUAL Published in Dec 01 Laser printer...
Page 2: ...Version Replaced pages Remarks Date 1 0 Revision history 5 Dec 2001...
Page 9: ...Chapter 1 P r o d u c t I n f o r m a t i o n...
Page 24: ...Chapter 2 Installation Operation...
Page 40: ...Chapter 3 Maintenance Adjustments...
Page 52: ...Chapter 4 O p e r a t i o n O v e r v i e w...
Page 81: ...Chapter 5 D i s a s s e m b l y...
Page 111: ...FS 1010 5 31 8 Remove the eraser lamp 9 9 5 2 28 Removing the eraser lamp...
Page 113: ...Chapter 6 T r o u b l e s h o o t i n g...
Page 144: ...Appendix A D i a g r a m s...
Page 153: ...Appendix B S t a t u s P a g e...
Page 160: ...Appendix C I n t e r f a c e...