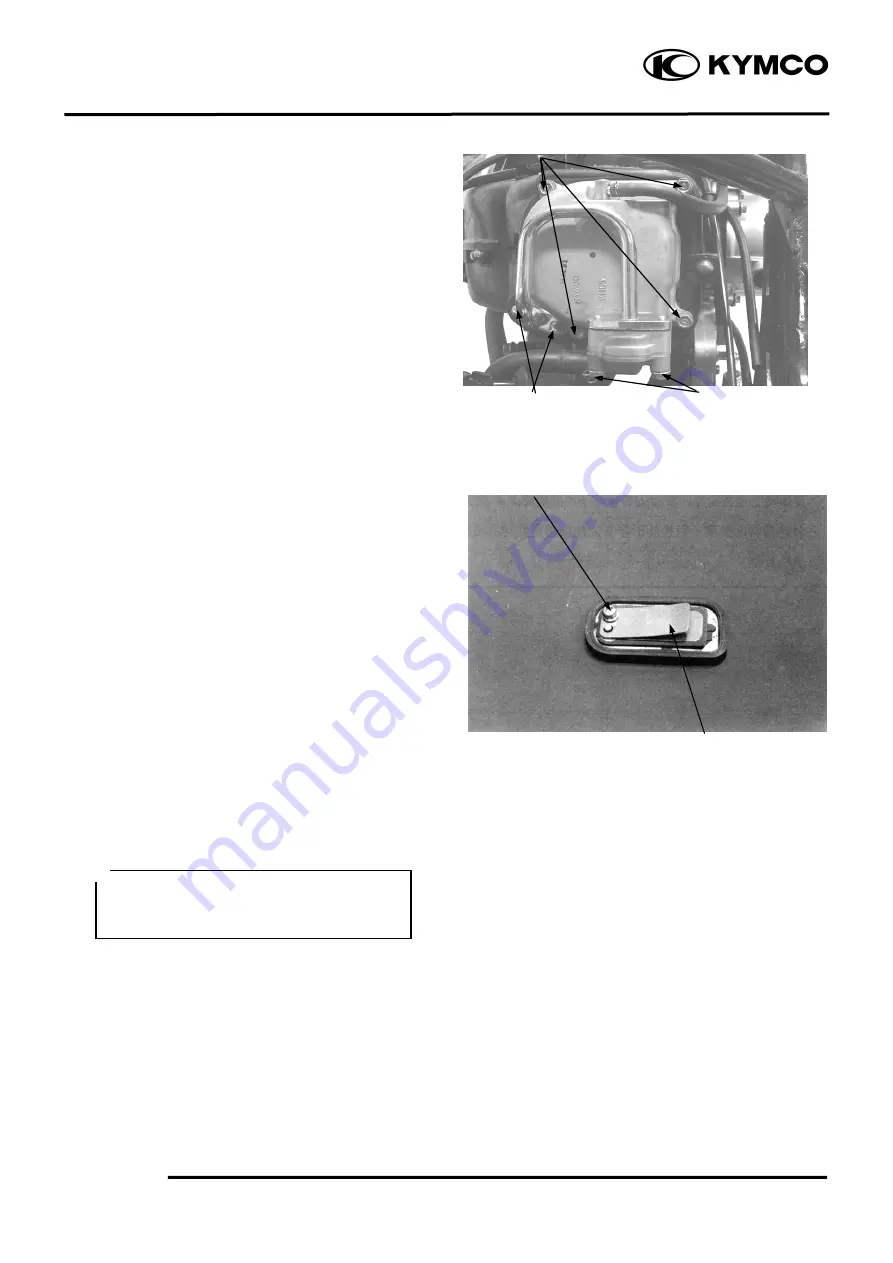
18
. EVAPORATIVE/EXHAUST EMISSION
CONTROL
SYSTEM
18-5
AGILITY 125
REED VALVE
REMOVAL
Remove the met-in box and frame center
cover.
Disconnect the secondary air inlet tube
connector.
Remove the four cylinder head cover bolts
and two secondary air outlet tube bolts.
INSPECTION
Remove the three screws attaching the reed
valve cover and the reed valve.
Check the reed valve for damaged or weak
reeds.
Check the reed valve seat for cracks, damage
or clearance between the seat and reed.
Check the gasket and O-ring for damage or
deterioration and replace if necessary.
Reed valve stopper clearance: 6.6mm
INSTALLATION
Install the reed valve in the reverse order of
removal.
Cylinder Head Cover Bolts
Secondary Air Inlet
Tube Bolt
Reed Valve Cover Bolts
Screws
Reed Stopper
•
When installing, be careful not to
bend or twist the tubes and check for
proper installation.
*