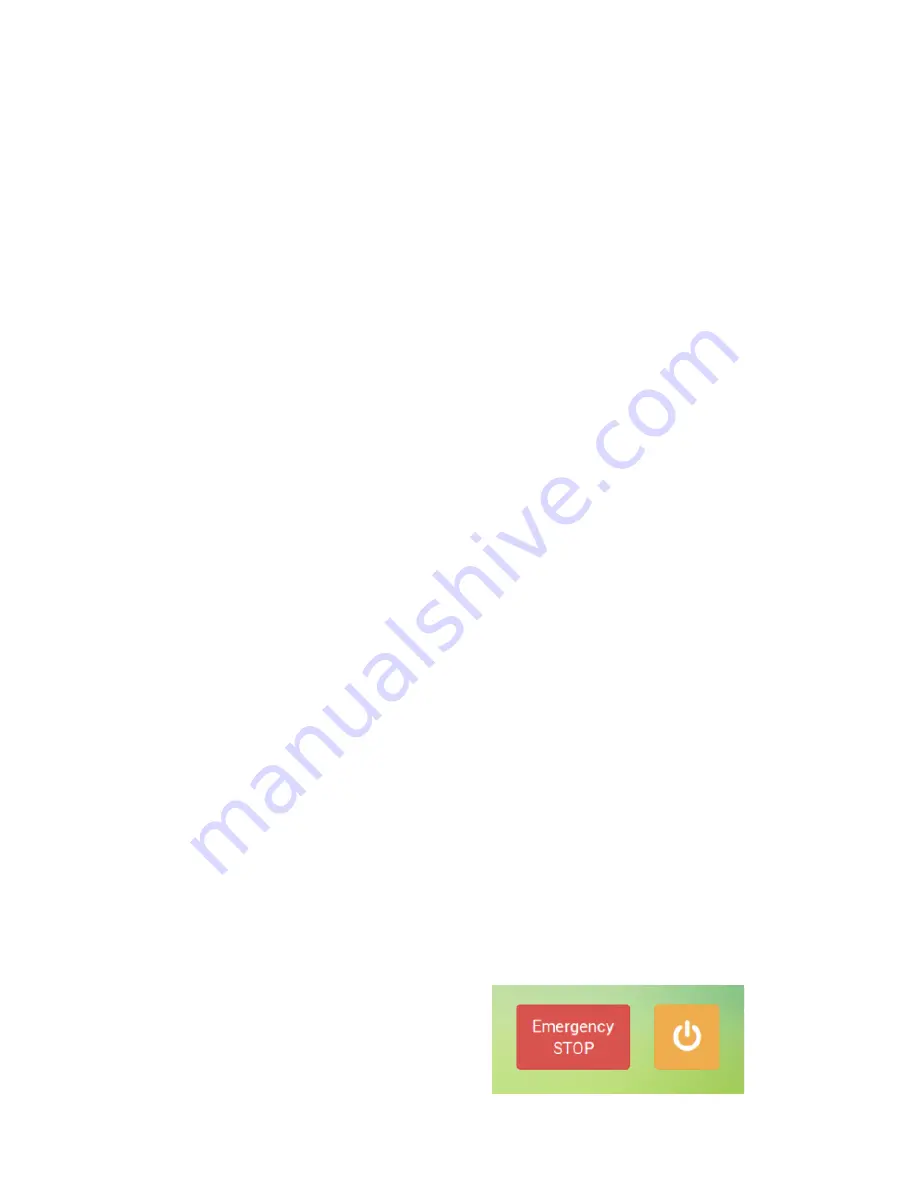
Coolant
For proper operation the HT500 is equipped with a closed loop low-maintenance cooling system that
needs little interference. The circuit is filled with coolant type Innovatek Protect IP ready-to-use.
If it is necessary to perform works on the cooling system, such as refilling coolant or exchanging
defective hoses, avoid direct skin or eye contact. Always wear adequate protective gloves that are
resistant to chemical substances (e.g. PVC, NBR).
Observe the information provided in the
manufacturer's safety data sheet
.
Additional information concerning the cooling system and required maintenance can be found in the
Service Guide
.
Noise
The HT500 3D Printer is build to be operated in a professional environment such as workshops and
laboratories. It is not suited for the operation in an office. During print jobs, it does not exceed
60dB(A), which is considered “unauspicious” for long-term exposure.
Special noise protection equipment is not required.
Fumes
Molten plastics may emit unpleasantly smelling fumes. The HT500 3D Printer is equipped with an
activated charcoal filter element to reduce such fumes. It is mainly to reduce smells and does not
protect from toxic fumes that evaporate from overheated plastics. Such fumes can be perilous.
It is vitally important not to exceed the temperature limits stated for a printed
material
. Overheating
is indicated by discoloration and coking.
Emergency stop
You will find a red Emergency STOP button in the top-right corner of the touchscreen. In case of any
unexpected performance of the 3D Printer, press this button to immediately stop any mechanical
movement in the build chamber and to shut down all heater elements.
NOTICE
The emergency stop function does not provide a cool down sequence. Do not use the emergency stop
button to abort current print jobs, because this may lead to damage of the 3D Printer due to
uncontrolled heat accumulation.
Do not use the main switch as an emergency stop button. You risk loosing or corrupting data.
When the emergency stop is triggered, the
microcontroller board responsible for the stepper
motors, heaters and sensors is reset
immediately and returns to idle state afterwards.
Now it is safe to resolve any problems or defects
in the build chamber.