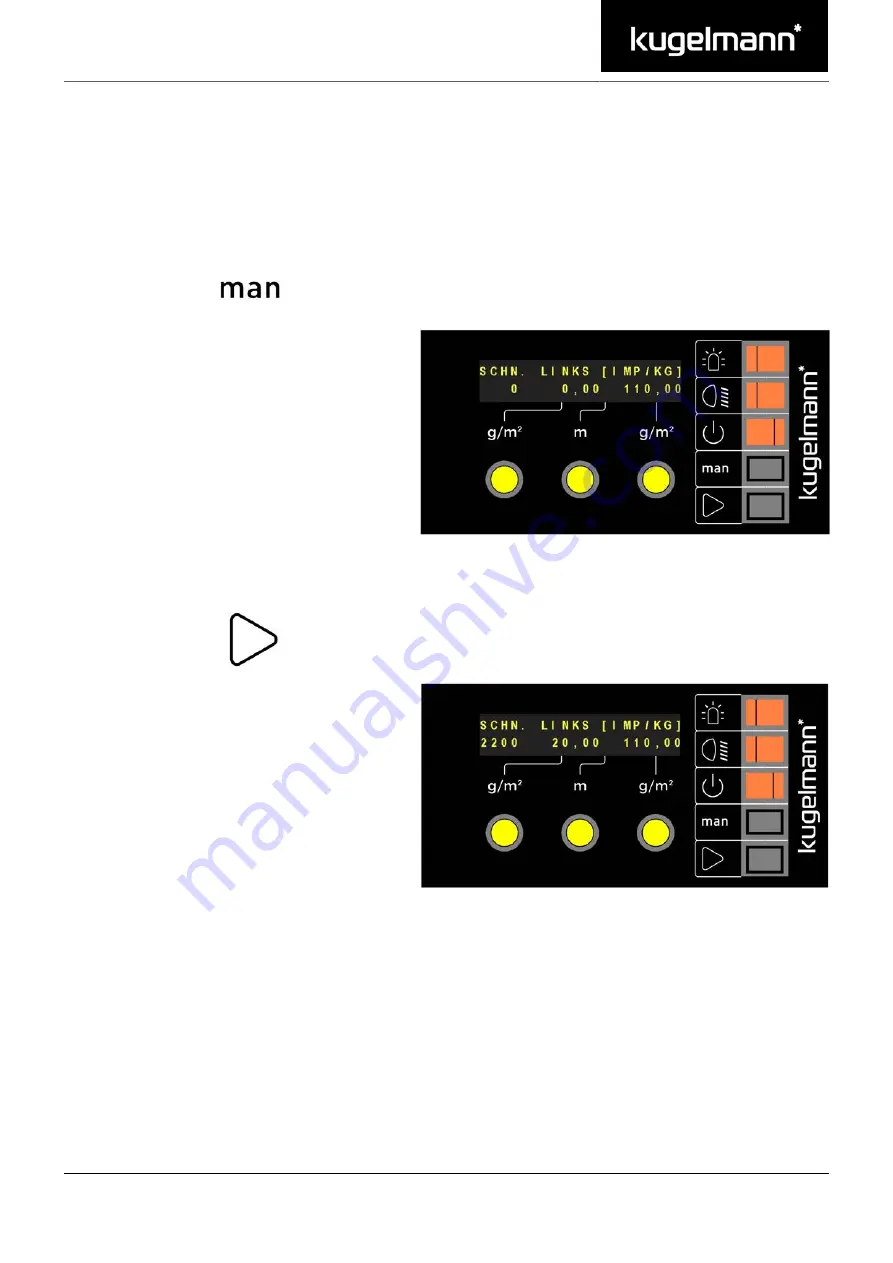
//
ORIGINAL OPERATING INSTRUCTIONS
Commissioning
March 3, 2018
39/55
3
Switch off control system (see Chapter
7.2 "Switch on / off control system",
), empty reservoir and place it under the screw conveyor outlet
again.
4
Call up menu (see Chapter
).
5
Actuate several times.
➯
6
7
Press and hold it pressed.
➯
For a more detailed setting, we recommend to take
out 20 kg.
8
Now, weigh the collected spreading material and compare it with the middle
value (Pos. 30) (here: 20.00 kg).
9
By turning the middle turning knob (Pos. 60), enter the weighted result:
•
Pr turning = 1.0 kg steps.
•
Turning = 0.1 kg steps