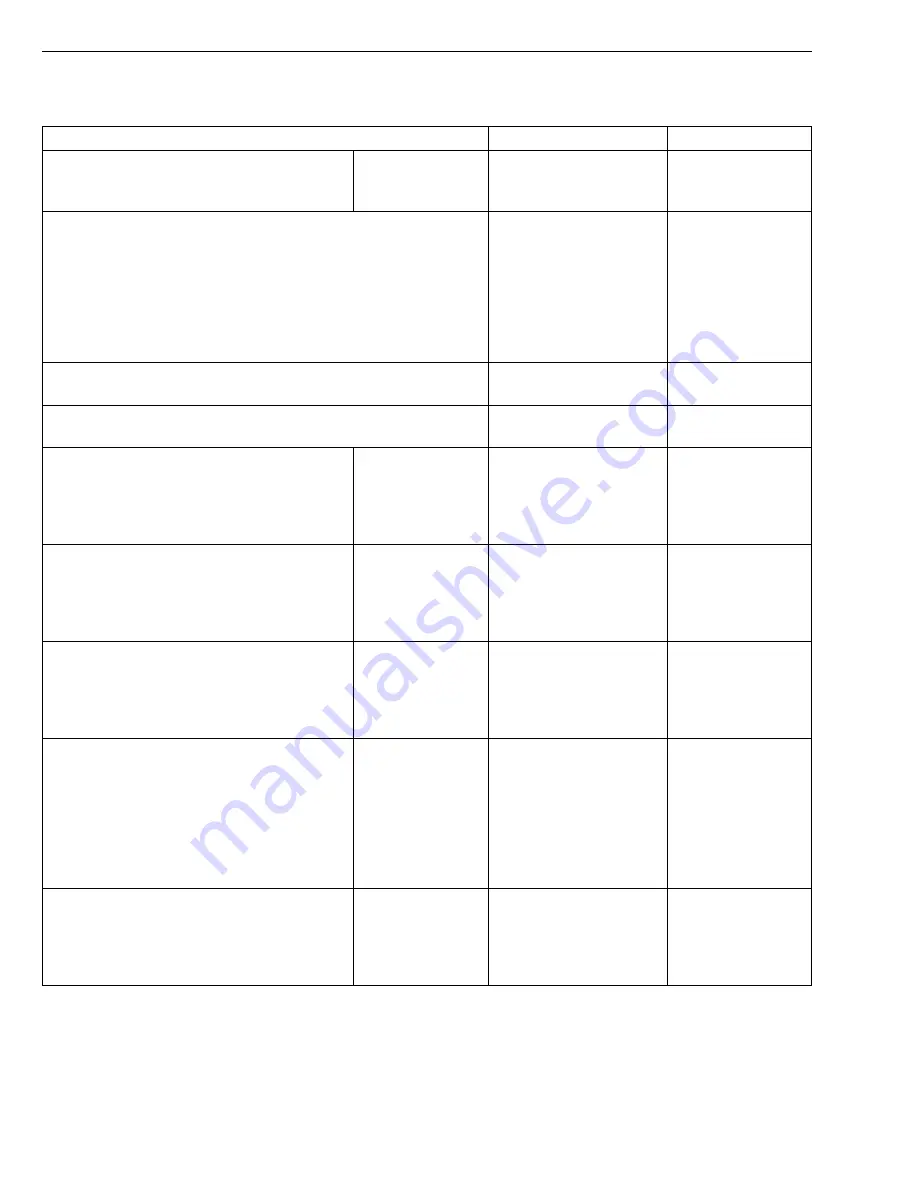
S-8
03-M-DI Series, WSM
DIESEL ENGINE
[5] SERVICING SPECIFICATIONS
ENGINE BODY
W1013874
Item
Factory Specification
Allowable Limit
Cylinder Head Surface
Flatness
–
0.05 mm / 500 mm
0.0020 in. /
19.69 in.
Compression Pressure
(When Cranking with Starting Motor)
Difference among Cylinders
2.94 to 3.24 MPa /
290 min
-1
(rpm)
30 to 33 kgf/cm
2
/
290 min
-1
(rpm)
427 to 469 psi /
290 min
-1
(rpm)
–
2.35 MPa /
290 min
-1
(rpm)
24 kgf/cm
2
/
290 min
-1
(rpm)
341 psi /
290 min
-1
(rpm)
10 % or less
Top Clearance
0.60 to 0.70 mm
0.0236 to 0.0276 in.
–
Valve Clearance (When Cold)
0.18 to 0.22 mm
0.0071 to 0.0087 in.
–
Valve Seat
Width (Intake)
Width (Exhaust)
2.12 mm
0.0835 in.
2.12 mm
0.0835 in.
–
–
Valve Seat
Angle (Intake)
Angle (Exhaust)
1.047 rad
60 °
0.785 rad
45 °
–
–
Valve Face
Angle (Intake)
Angle (Exhaust)
1.047 rad
60 °
0.785 rad
45 °
–
–
Valve Stem to Valve Guide
Valve Stem
Valve Guide
Clearance
O.D.
I.D.
0.040 to 0.070 mm
0.0016 to 0.0028 in.
7.960 to 7.975 mm
0.31339 to 0.31398 in.
8.015 to 8.030 mm
0.31555 to 0.31614 in.
0.1 mm
0.0039 in.
–
–
Valve Recessing
Protrusion
Recessing
0.65 mm
0.026 in.
to
0.85 mm
0.033 in.
–
1.20 mm
0.0472 in.
KiSC issued 10, 2009 A