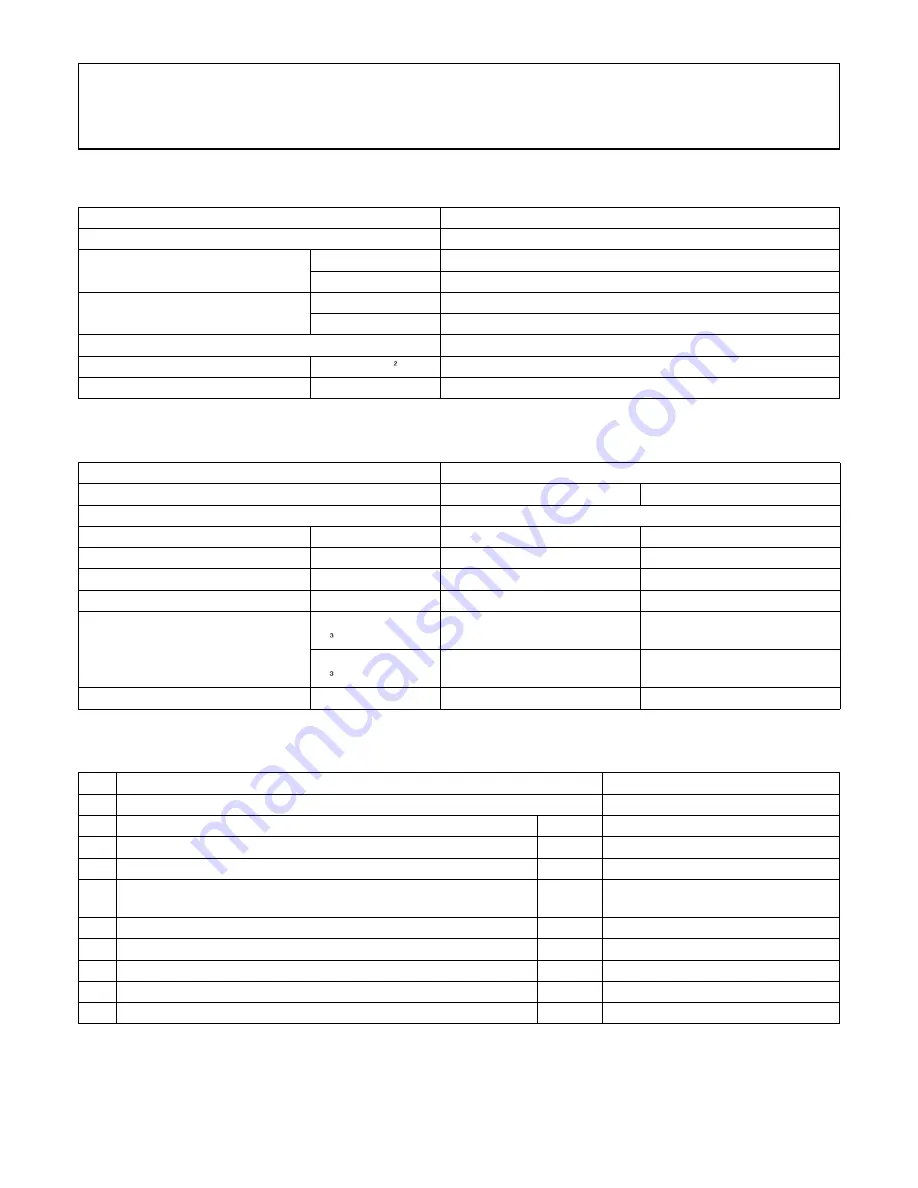
4
SPECIFICATIONS OF THE LOADER
SPECIFICATIONS OF THE LOADER
LOADER SPECIFICATIONS
BUCKET SPECIFICATIONS
DIMENSIONAL SPECIFICATIONS
LOADER MODEL
TL500
TRACTOR MODEL
B26
BOOM CYLINDER
BORE mm (in.)
50 (1.97)
STROKE mm (in.)
399 (15.7)
BUCKET CYLINDER
BORE mm (in.)
55 (2.17)
STROKE mm (in.)
382.5 (15.1)
CONTROL VALVE
1 Detent Float Position, Power Beyond Circuit
MAXIMUM PRESSURE
MPa (kg/cm , psi)
16.6 (169, 2402)
NET WEIGHT (APPROXIMATE)
kg (lbs.)
285 (628)
LOADER MODEL
TL500
MODEL
HD ROUND 60
LM ROUND 66
TYPE
QUICK ATTACH
WIDTH
mm (in.)
1524 (60)
1676 (66)
DEPTH (L)
mm (in.)
453 (17.8)
623 (24.5)
HEIGHT (M)
mm (in.)
584 (23.0)
584 (23.0)
LENGTH (N)
mm (in.)
646 (25.4)
816 (32.1)
CAPACITY
STRUCK
m (CU.FT.)
0.22 (7.8)
0.32 (11.3)
HEAPED
m (CU.FT.)
0.27 (9.5)
0.39 (13.8)
WEIGHT
kg (lbs.)
126 (278)
149 (328)
LOADER MODEL
TL500
TRACTOR MODEL
B26
A
MAX. LIFT HEIGHT (TO BUCKET PIVOT PIN)
mm (in.)
2400 (94.5)
B
MAX. LIFT HEIGHT UNDER LEVEL BUCKET
mm (in.)
2189 (86.2)
C
CLEARANCE WITH BUCKET DUMPED
mm (in.)
1778 (70)
D
REACH AT MAX. LIFT HEIGHT
(DUMPING REACH)
mm (in.)
567 (22.3)
E
MAX. DUMP ANGLE
deg.
45
F
REACH WITH BUCKET ON GROUND
mm (in.)
1561 (61.5)
G
BUCKET ROLL-BACK ANGLE
deg.
46
H
DIGGING DEPTH
mm (in.)
177 (7.0)
J
OVERALL HEIGHT IN CARRYING POSITION
mm (in.)
1258 (49.5)