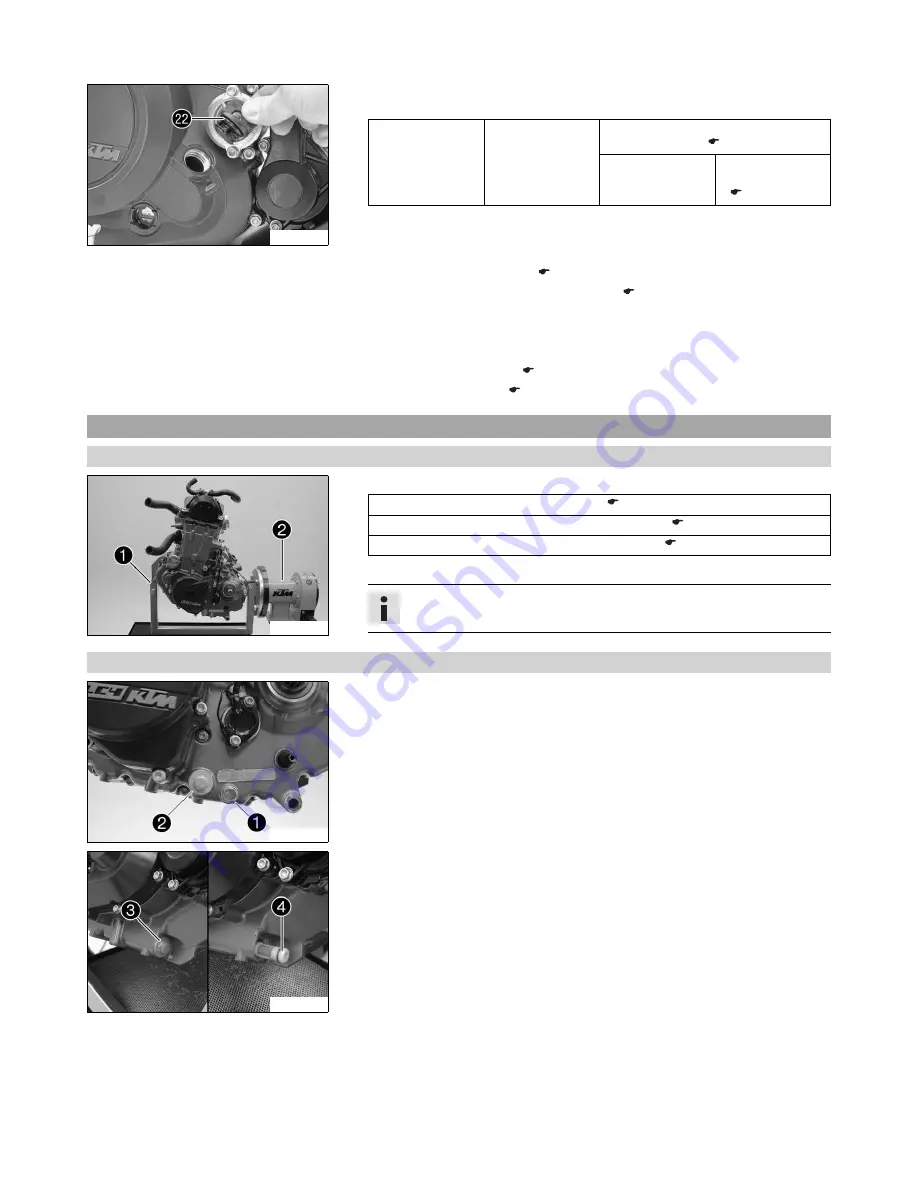
17
ENGINE
110
300802-11
–
Remove the oil filler plug with O-ring
cm
from the clutch cover and fill up with
engine oil.
Engine oil
1.70 l (1.8 qt.)
Engine oil (SAE 10W/60)
(00062010035) (
p. 210)
Alternative engine
oil
Engine oil
(SAE 10W/50)
(
p. 210)
–
Install and tighten the oil filler plug with O-ring
cm
.
Finishing work
–
Fill/bleed the cooling system. (
p. 166)
–
Remove the motorcycle from the work stand. (
p. 11)
–
Take a short test ride.
–
Read out the fault memory using the KTM diagnostics tool.
–
Check the engine for leakage.
–
Check the engine oil level. (
p. 169)
–
Check the coolant level. (
p. 168)
17.3
Engine disassembly
17.3.1
Clamping the engine into the engine assembly stand
300144-10
–
Mount special tool
1
on engine work stand
2
.
Engine assembly stand (61229001000) (
p. 217)
Support for engine assembly stand (75012001060) (
p. 218)
Holder for engine assembly stand (75012001070) (
p. 218)
–
Mount the engine on special tool
1
.
Info
Have an assistant help you or use a crane.
17.3.2
Draining the engine oil
300002-10
–
Remove the oil drain plug
1
with the magnet and seal ring.
–
Remove plug
2
with oil screen and the O-rings.
300161-10
–
Remove plug
3
with oil screen
4
and the O-rings.
–
Completely drain the engine oil.