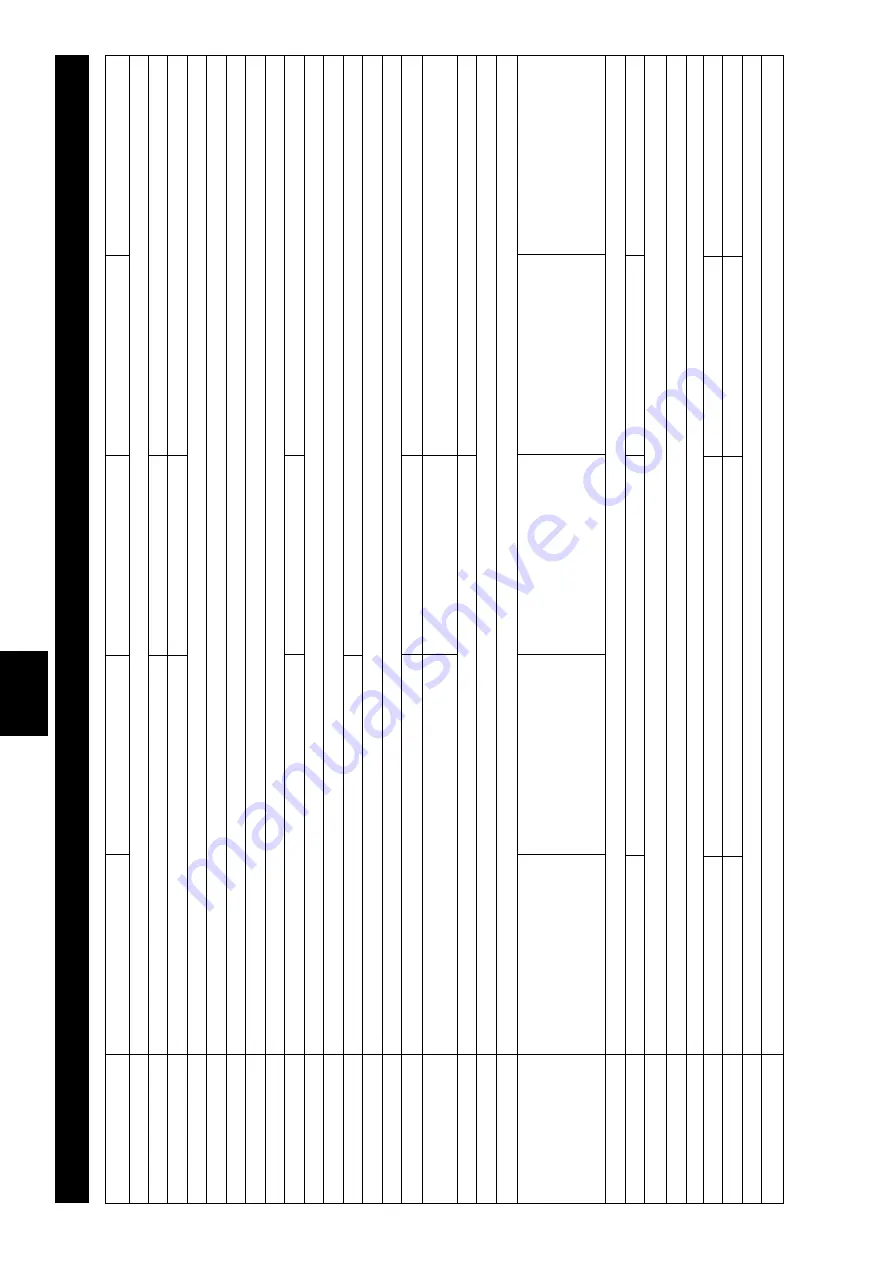
8
Engine
250 SX
250 EXC, M-XC
300 EXC, M-XC
380 SX
380 EXC, M-XC
Design
Liquid-cooled single-cylinder two-stroke engine with
KTM T
win
V
alve
C
ontrol exhaust system and
K
TM
T
orque
C
hamber
Piston displacement
249 ccm
297 ccm
3
68 ccm
Bore / stroke
67.5 / 69.5 mm (2.66 / 2.74 in)
72 / 73 mm (2.84 / 2.88 in)
78 / 77 mm (3 / 2.98 in)
Fuel
SUPER fuel, research octane no 95, mixed with high-grade two stroke oil (Shell Advance Racing X)
Oil / gasolin ratio
1:50 - 1:60 when using high grade two stroke oil. When in doupt, please contact your importer or use 1:40 mi
x ratio to be on the safe side
Crankshaft bearing
1 deep-groove ball bearing / 1 cylinder roller bearing
Connecting rod bearing
needle bearing
Piston pin bearing
needle bearing
Piston
cast piston
forged piston
cast piston
Piston ring
two plain compression rings
Dimension "X"
0 +0.1 mm (0 + 0.004 in)
Ignition timing
1.8 mm (0.07 in) (17 °) BTDC
2.0 mm (0.08 in) (17°) BTDC
2.2 mm (0.09 in) (17 °) BTDC
Spark plug
NGK
BR
8 ECM
Electrode gap
0.6 mm (0.024 in)
Dimension "Z"
48 mm (1.9 in)
46 mm (1.7 in)
50.5 mm (1.99 in)
TVC start open
5400/min
5300/min
5200/min
TVC fully open
7550/min
7750/min
7200/min
Primary drive
straight cut spur gears, primary ratio 25:72
straight cut spur gears, primary ratio 26:72
Clutch
multiple disc clutch in oil bath
T
ransmission
5 speed, claw actuated
Gear ratio
EXC
M-XC
EXC
MXC
1
st
Gear
15:29
15:29
15:29
15:29
15:29
15:29
15:29
2
nd
Gear
17:27
18:26
18:26
18:26
18:26
18:26
18:26
3
rd
Gear
19.25
19:22
19:22
19:24
19:24
19:22
19:24
4
th
Gear
21:23
21:20
21:20
21:23
21:23
21:20
21:23
5
th
Gear
23:21
23:18
23:18
23:21
23:21
23:18
23:21
Gear lubrication
0.8 l engine oil 20W
-40 (Shell Advance VSX4)
Rear wheel ratio
14:50
14:52
14:50
14:52
A
vailable chain sprockets
13t / 14t / 15t for chain
5
/
8
x
1
/
4
"
A
vailable final sprockets
38t / 40t / 42t / 45t / 48t / 50t / 52t for chain
5
/
8
x
1
/
4
"
Coolant
1.3 litres, 40% anti freeze, 60% water
, at least -25 °C (-13 °F)
Ignition system
KOKUSAN 2K-1
KOKUSAN 2K-2
KOKUSAN 2K-1
KOKUSAN 2K-2
Generator output
no generator
12V 40W
no generator
12V 40W
Carburetor
flat-slide carburetor
, carburetor setting see table 3
Air
-filter
wet foam type air filter insert
(upper edge piston - upper edge cylinder)
(height of the control flap)
8.1 TECHNICAL DA
T
A
- ENGINE (only USA)
Summary of Contents for 250 1998
Page 9: ... Notices ...
Page 39: ... Notices ...
Page 43: ... Notices ...
Page 44: ...7 1 7 0 Trouble shooting Cap Component Component unit Page 7 1 Trouble shooting 7 2 ...
Page 47: ... Notices ...
Page 54: ......
Page 55: ......
Page 56: ......
Page 57: ......
Page 58: ......