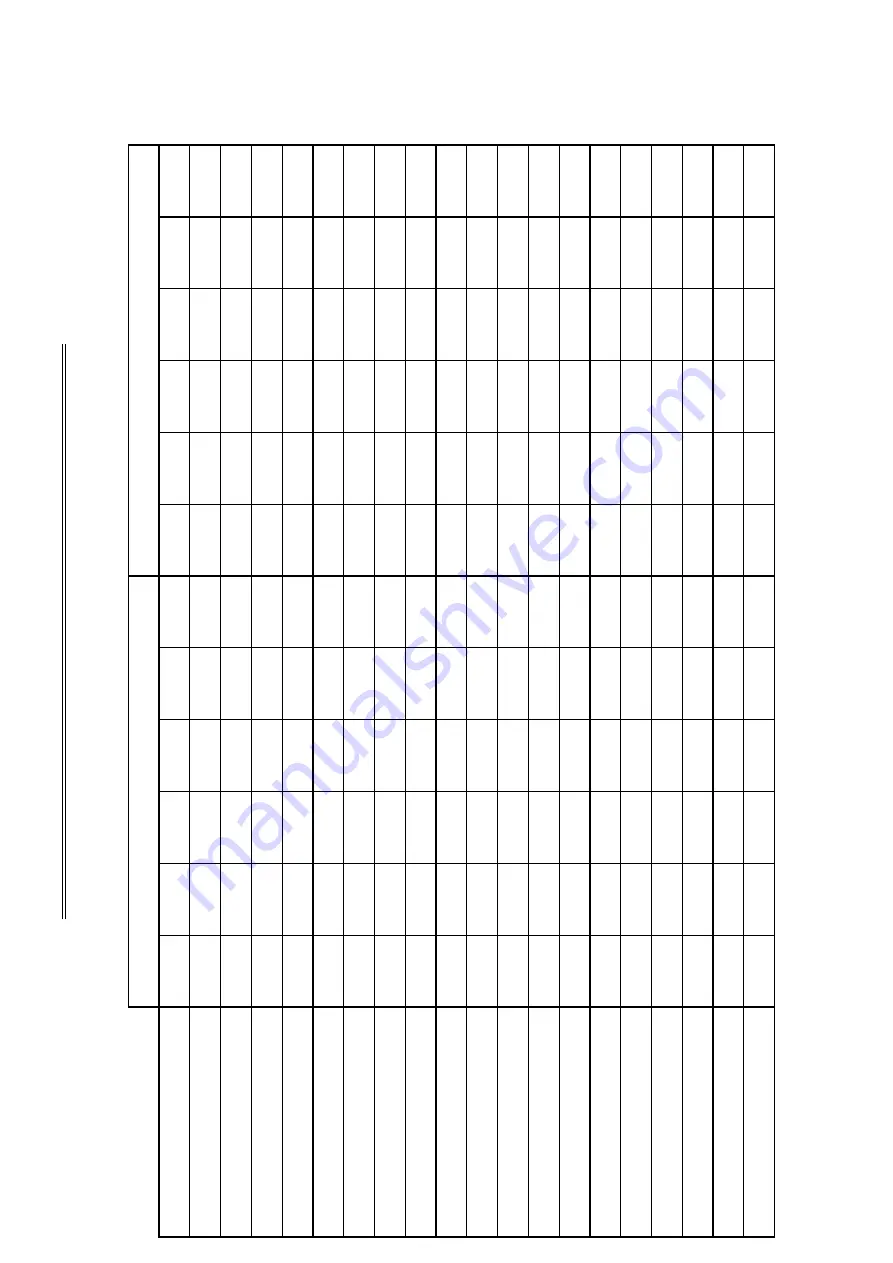
Settings KSM-Multistoker 575-50 with PCT 300
Program
Pgr 1
Pgr 2
Pgr 3
Pgr 1
Pgr 2
Pgr 3
Language
EEEEEE
Fuel type
Pellet
Chip
Div
Pellet
Chip
Div
Boilertemp. °C
75
75
75
75
75
75
Pauseperiod Min.
10
10
10
10
10
10
Wood temp
85
85
85
85
85
85
Man/Aut
000000
Man operation
000000
Aschscrew
35
1
0
35
1
0
Moving floor ON
555555
Moving floor OFF
60
40
20
60
40
20
Transport.sc.on
90
90
90
90
90
90
Transport.sc.off
555555
Screw step 0 sek.
0,40
1,20
0,80
0,16
0,5
0,33
Screw step 1 sek.
0,80
2,40
1,60
0,33
1,00
0,66
Screw step 2 sek.
1,60
4,80
3,20
0,66
2,00
1,30
Screw step 3 sek.
3,20
9
4,80
1,30
4,00
2,60
Fan step 0
555555
Fan step 1
25
25
25
25
25
25
Fan step 2
50
50
50
50
50
50
Automatic and 500 l. silo
F-Automatic
Supplement B-Standard settings
The blanks can be used to introduce your own values.
01/08-2010
Summary of Contents for KSM-Multistoker 575-50
Page 3: ......
Page 46: ......
Page 47: ......
Page 48: ......
Page 50: ......
Page 51: ......
Page 52: ......
Page 53: ......
Page 61: ... 44 Supplement C ...
Page 62: ... 45 ...
Page 63: ... 46 ...
Page 64: ... 47 ...
Page 66: ......
Page 67: ......
Page 68: ......