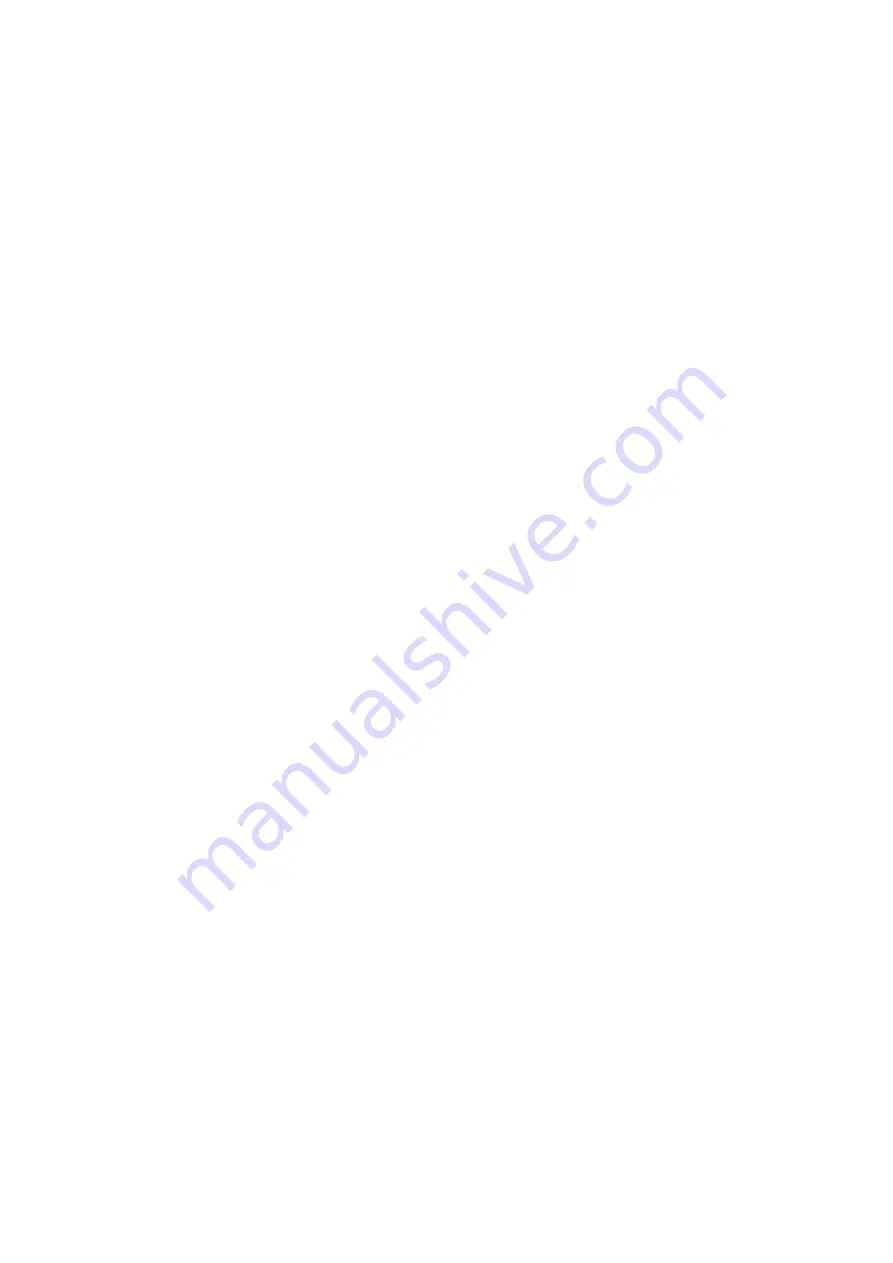
- 37 -
20.0 Interruptions Of The Operation
20.1 Unburned fuel in the ashes.
1. False air, causing the oxygen meter to give incorrect measures.
Check for open dampers or leaks around doors.
2. More air is required for the combustion, set a higher oxygen %
3. Check the settings and adjust, if needed, see section 9.
20.2 The boiler becomes sooty.
1. False air, causing the oxygen meter to give incorrect measures.
Check for open dampers or leaks around doors.
2. Oxygen sensor closed with dirt. Scrape it clean.
3. Check the settings and adjust, if needed, see section 9.
20.3 Black display.
1. No power supply. Check fuses in the fuse box.
2. Electric Protection Fuses for the transport screw is stopped. Press the black button to
restart
3. Maximum heat thermostat disconnected. Re-activate it.
4. A fuse has blown in the control. Call for service.
5. Fuel container lid open. Close the lid.
6. Fuel container lid closed but lid switch defect. Call for service.
20.4 Combustion air fan does not run during plant operation.
1. A fuse has blown in the control.
Call for service.
20.5 The screw does not run
1. A faint wining sound is heard from the control. The Stop
Screw button is activated, re-clunch the screw by pressing the
”Start” button.
2. The motor hums. The screw has stuck, due to a foreign body
or some moist fuel in the screw.
Dismount the screw and clean the screw tube.
20.6 Backfire.
If you have been very unlucky and
the thermal valve has been triggered, it is necessary to clear out the
screw for moist pellets before re-starting the plant.
The easiest way is to dismount the 4 bolts holding the gear motor, and then twist it loose. Ask an assistant
to press the Start button while you hold on to the motor, and the motor will then quietly unscrew from the
screw tube, it may now be cleaned and finally gear-motor and screw can be re-mounted.
By repeated backfires, the pause times should be adjusted, see section 6.4.
Also check if a draught stabilizer has in fact been mounted in the chimney, this is very important with a
view to avoiding a backfire.
20.7 Clinker.
Clinker may build up in the area where the screw tube enters into the burner head, this may contribute to
the problems with the screw getting stuck. The fuel heaps up and is squeezed together so hard that the
screw cannot push it out.
In that case, clean the screw tube in all corners to get rid of any caked clinker in order to make the screw
run freely again.
A too ample formation of clinker by grain combustion may be reduced by adding about 1-2 % of calcium,
as mentioned earlier.
Summary of Contents for KSM-Multistoker 575-50
Page 3: ......
Page 46: ......
Page 47: ......
Page 48: ......
Page 50: ......
Page 51: ......
Page 52: ......
Page 53: ......
Page 61: ... 44 Supplement C ...
Page 62: ... 45 ...
Page 63: ... 46 ...
Page 64: ... 47 ...
Page 66: ......
Page 67: ......
Page 68: ......