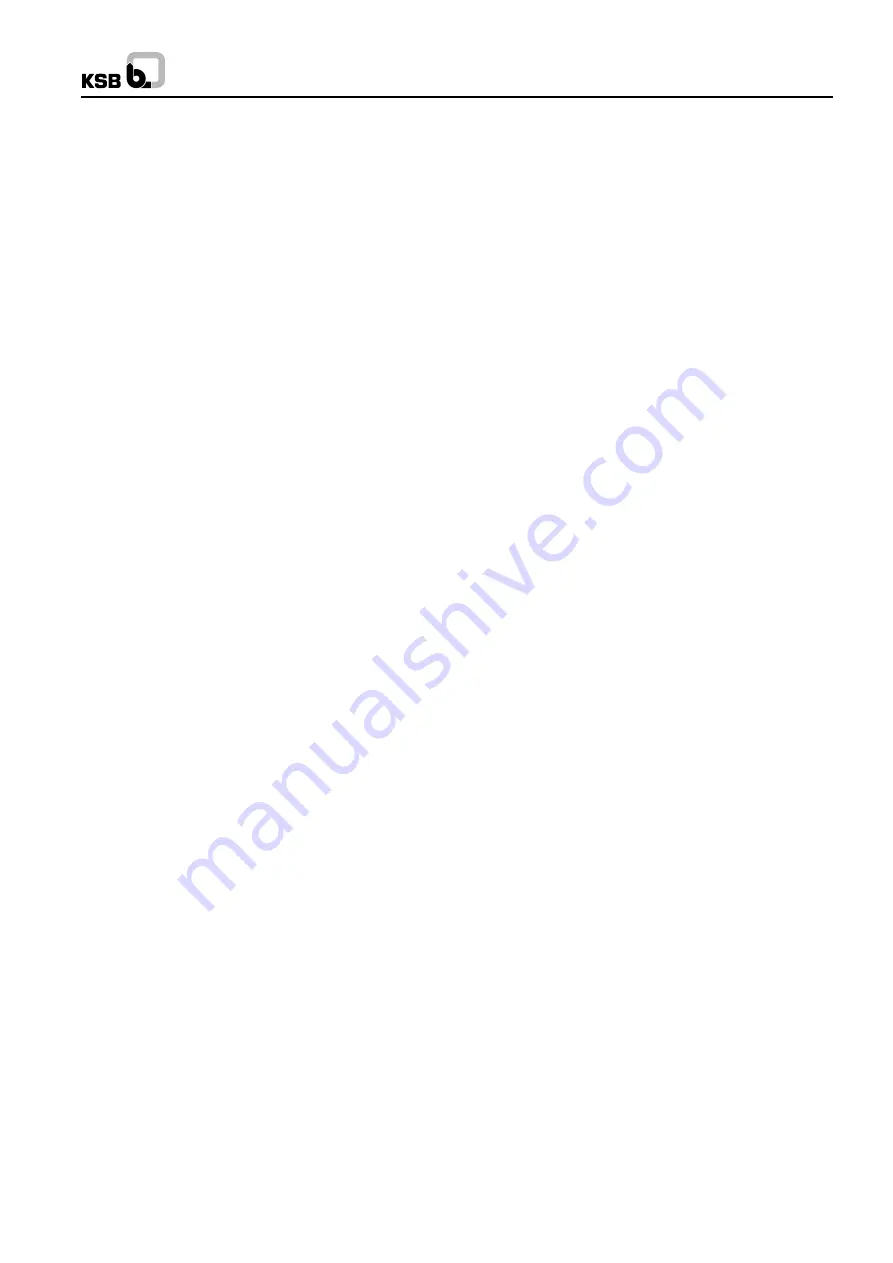
WK
15. Check List
15.1 Pre-requisites for Initial Commissioning
Check direction of rotation of driver with pump disconnected.
Check correct alignment of pumping set with appropriate
alignment jigs and dial micrometers.
Check that the stuffing box gland seats squarely and has
sufficient guidance (with the aid of a feeler gauge, check that
the gap between the shaft protection sleeve and the stuffing
box gland remains the same around the circumference). If
mechanical seals are fitted, check that the circulation lines are
vented at the apex.
Check that the system is primed with the fluid pumped, and
thoroughly vented via the vent valve in the discharge line (if
provided), and via the vent screws of the pressure gauge valve
(suction pressure-discharge pressure).
Check that the valves in the minimum flow line are opened.
Check that the valve in the manually-operated line of the
minimum flow device is opened.
Check that oil has been filled in the bearing bracket and that
the required oil level has been attained (by oil pouring out of
the overflow holes).
Observe the start-up procedure for the driver.
If the operating temperature exceed 150
0
C, check that the main
valve in the cooling liquid supply line is fully open, and that the
fluid flows through freely, also check that the throttling valves
in the cooling liquid lines are fully open.
Check that the isolating valve in the suction head line is fully
open.
Check that the isolating valve in the discharge line is closed.
15.2 Initial Start-up with Cold Water
Switch on driver for a short instant, and switch it off again
immediately. Check that rotor runs down smoothly and evenly
to a standstill.
Switch driver on again. Check quiet running of pump.
Observe the stuffing boxes (they should not run too hot).
Make sure that the pump runs smoothly and quietly, and that
the stuffing boxes function correctly.
On pumps fitted with mechanical seals, keep a check on the
temperature in the circulation lines.
Keep a check on the pressure gauge indications (suction and
discharge pressures).
If the pump is turbine driven, run up turbine to full operating
speed as rapidly as possible, and make sure the pump runs
quietly during this time.
15.3 Priming the Boiler
Crack the isolating valve in the discharge line open slowly
(remember lag of servo-actuated valves). Run the pump within
the confines of the limitation curve of the operating diagram
(see section 10.3 ‘‘Pump Operation and Supervision’’).
15.4 Initial Operation with Hot Fluid
When the nominal temperature of the fluid pumped has been
attained, adjust the flow rate of the cooling liquid supply. This
should be done by throttling the individual valves in the internal
cooling liquid piping system in such a way that a temperature
differential of 10
0
C max. is set up between the cooling liquid
inlet and outlet.
During operation, check the pressure drop across the strainer
in the suction lift or suction head line. When the max.
permissible pressure drop value has been reached, switch off
the pumping set and clean the strainer.
15.5 Supervision of Operations & Maintenance
During operation, the pump should be kept under careful
observation. The following measurement values should be
checked at frequent intervals :
Suction pressure
Suction temperature
Pump discharge pressure
Temperature at pump discharge nozzle
Bearing temperature
Stuffing box leakage
Temperature of mechanical seals
Cooling liquid temperature at cooler outlet (Max. temperature
differential 10
0
C)
Check that the pump runs smoothly and quietly at all times,
and check the pressure drop across the suction head line by
differential pressure measurement.
We recommend keeping a log book on pump operation, to
supervise the pumps more closely; the following data should
be entered in this log book at hourly intervals : rate of flow,
suction pressure, discharge pressure, temperature of fluid
pumped, rotational speed and axial rotor position. The times
of start-up and shutdown should also be recorded, so that the
total number of hours of operation of the feed pump can be
ascertained at any time.
The oil level and oil quality should be checked, respectively
tested, after the first 200 hours of operation. Thereafter, the oil
level and oil quality should be checked at least once a month.
28