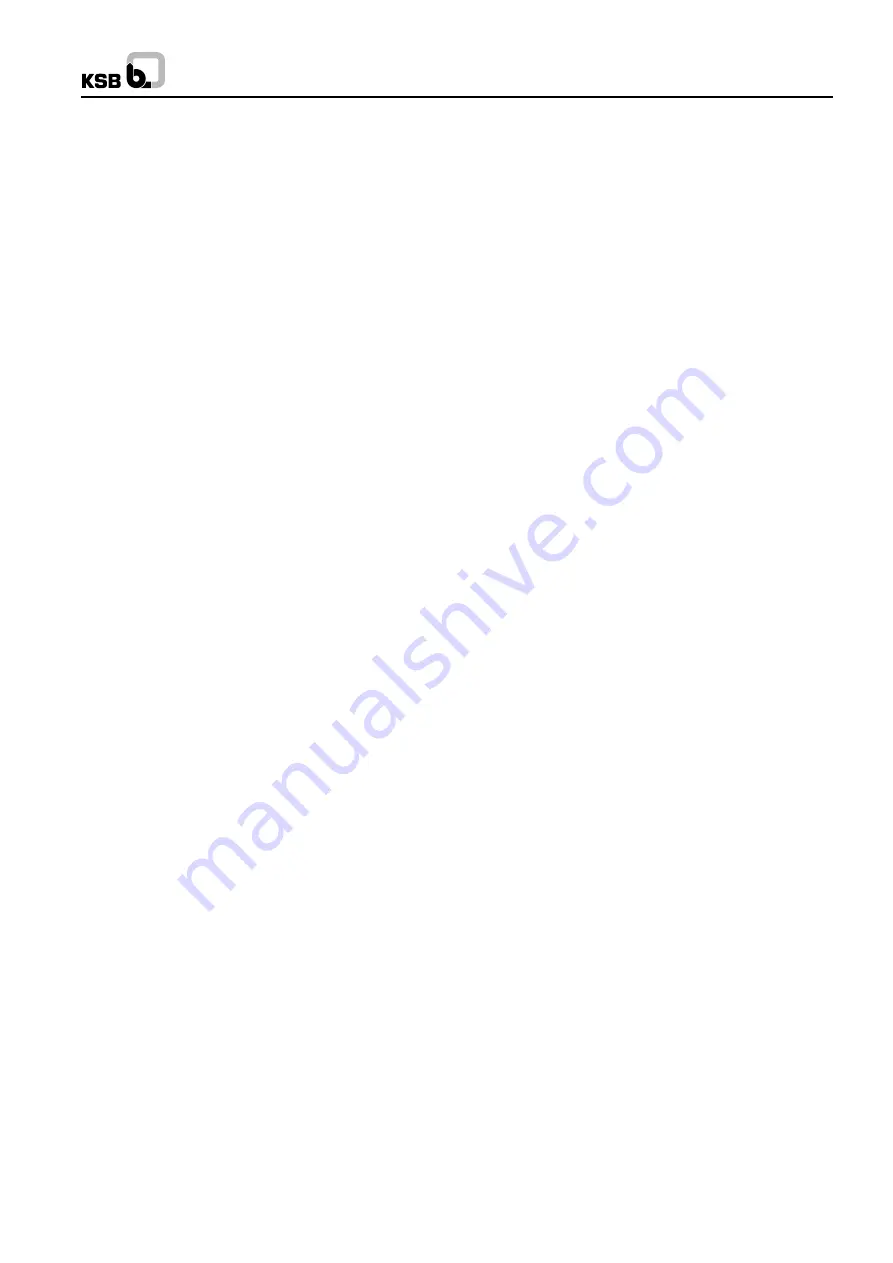
WK
29. Dirt or sand in cooling liquid fed to stuffing box gland
causes scoring of shaft protection sleeve.
30. Excessively high axial thrust.
31. Insufficient quantity of oil in bearing housing, unsuitable
oil quality, dirty oil, water in the oil.
32. Faulty bearing assembly (damage during assembly,
wrong, assembly).
33. Dirt in the bearings.
34. Ingress of water into bearing housing.
35. Rubbing faces of mechanical seal worn or scored. O-rings
damaged.
36. Seal incorrectly assembled. Materials unsuitable.
37. Surface pressure in sealing gap too high, no fluid available
for lubrication and cooling.
38. Fault in cooling liquid supply system to mechanical seal.
39. Excessively large gap between cooling housing and
spacer sleeve. Temperature in the cooling circuit rises
excessively.
40. Dirt in cooling circuit of mechanical seal leads to scoring
of mechanical seal rubbing faces.
13.3 Suggested Remedies
If, after a breakdown has occurred, one of the cause listed in
section 13.2 has been established as the cause, and the matter
has been put right or the cause of the trouble eliminated, it is
recommended, prior to recommissioning the set, to check the
effortless rotation of the pump rotor by hand, with the driver
disconnected (unless the pump had to be dismantled in any
case, because of the damage). Check that the pump runs
smoothly and quietly after recommissioning.
Cause 1. Open vent valves or pressure gauge vent screws,
open isolating valves in minimum flow device
circuit. Check layout of pipelines to ensure that fluid
flows smoothly.
Cause 2. Prime pumps and piping again, and vent them
thoroughly. Check layout of pipelines.
Cause 3. Check isolating valve and strainers in suction line.
The instrument readings taken must be accurate.
Consult manufacturer.
Cause 4. Check water level in reservoir and examine
possibility of altering it. Raise water level, alter
mouth of suction line. The nozzle should not project
too high inside the reservoir, and it should be
shaped so as to promote favourable flow
characteristics.
Cause 5. Increase speed, if pump it turbine-driven. Refer to
manufacturer, if pump is motor-driven. Check
operation of minimum flow device.
Cause 6. Decrease speed, if pump is turbine-driven. Refer
to manufacturer, if pump is motor driven.
Cause 7. Cross over two phase leads on the motor.
Cause 8. Increase rotational speed. Fit larger diameter
impellers. Increase number of stages. Refer to
manufacturer.
Cause 9. Adjust pressure conditions by means of discharge
valve. Alter rotation speed, alter impeller diameter.
Refer to manufacturer.
Cause 10. Check temperature of fluid pumped, take steps
outlined in 9, above.
Cause 11. Check operation of minimum flow device. Refer to
manufacturer.
Cause 12. Check condition of individual machines. Refer to
manufacturer.
Cause 13. Clean out pump, check condition of suction system
(check suction line and strainers).
Cause 14. Realign pumping set when cold.
Cause 15. Refer to manufacturer.
Cause 16. Fit a new shaft. On no account straighten outt a
bend shaft.
Cause 17. Dismantle pump.
Cause 18. Check quiet running of pumps. Check coupling
alignment (when cold). Check oil quality and
cleanlines.
Cause 19. Fit new casing wearing rings, Check out-of-round
(true running of) rotor. Check presence of foreign
bodies in the pump (see also item 16).
Cause 20. Fit new impeller. Check suction head (cavitation).
Check system for presence of foreign bodies (see
also item 16).
Cause 21. Replace damaged components by new ones.
Cause 22. Replace damaged components by new ones.
Check shaft protection sleeves for true running
(out-of-round). Check suitability of packing material
used. Check that gland is not tightened askew and
observe rate of leakage.
Cause 23. Carefully repack stuffing box. Check suitability of
packing material used.
Cause 24. Realign coupling (when cold). Fit new bearings.
Check rotor for signs of damage.
Cause 25. Check suction pressure (cavitation). Check
coupling alignment. Check pump internals for
presence of foreign bodies.
Cause 26. Repack stuffing box. Tighten gland lightly only.
Alow slightly higher rate of gland leakage. Check
suitability of packing material used.
Cause 27. Check unobstructed flow through cooling liquid
feed line.
Cause 28. Fit an end ring or a new stuffing box gland. Check
condition of shaft protection sleeve.
Cause 29. Use treated cooling liquid. Fit filters in cooling liquid
lines.
Cause 30. Check rotor clearances. Check axial adjustment
(position) of rotor.
Cause 31. Check oil quality and quantity.
Cause 32. Check bearing components for signs of damage
and assemble them correctly.
Cause 33. Throughly clean bearings, bearing housings and
check condition of bearing of seal.
Cause 34. Remove all rust from bearings and bearing
brackets. Change the oil fill.
Cause 35. Replace damaged components by new ones.
Check rotating components for out-of-round. Check
suitability of materials used. Make sure all seal
components seat accurately, and lookout for
leakage.
Cause 36. Carefully insert seal. Check materials for suitability.
Cause 37. Measure the seal anew. Refer to manufacturer.
26