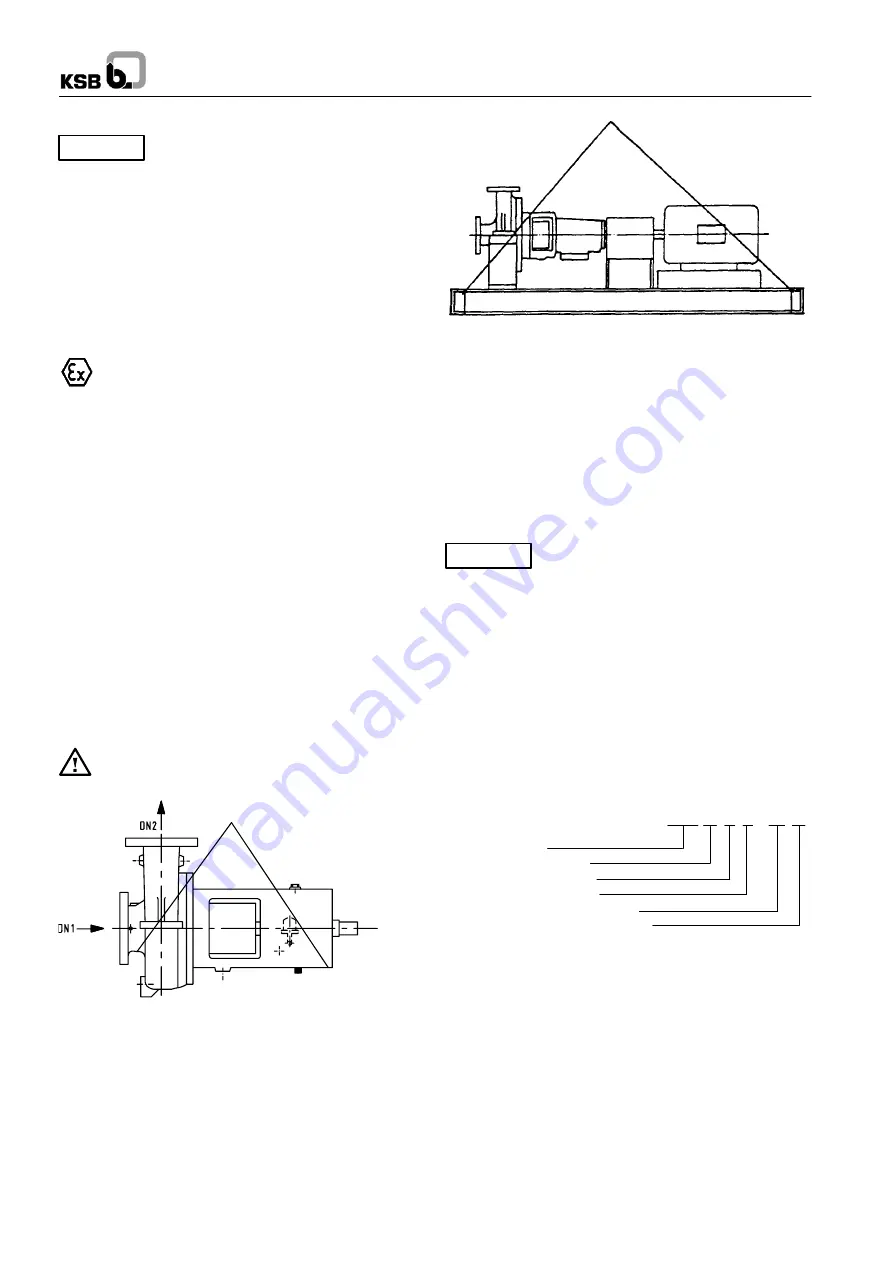
Caution
Caution
RPH
6
Safety note:
The permissible operating temperature of the
pump in question is indicated on the data
sheet. If the pump is to be operated at a higher temperature, the
data sheet is missing or if the pump is part of a pool of pumps,
the maximum permissible operating temperature must be
enquired from the pump manufacturer.
Based on an ambient temperature of 40
°
C and proper
maintenance and operation, compliance with temperature
class T4 is warranted in the area of the rolling element bearings.
A special design is required to comply with temperature class
T6 in the bearing area. In such cases, and if ambient
temperature exceeds 40
°
C, contact the manufacturer.
2.9.6
Maintenance
Only a pump unit which is properly serviced and maintai-
ned in perfect technical condition will give safe and relia-
ble operation.
This also applies to the reliable function of the rolling element
bearings whose actual lifetime largely depends on the opera-
ting mode and operating conditions.
Regular checks of the lubricant and the running noises will pre-
vent the risk of excessive temperatures as a result of bearings
running hot or defective bearing seals (also see section
7.2.2.2).
The correct function of the shaft seal must be checked regularly.
Any auxiliary systems installed must be monitored, if neces-
sary, to make sure they function correctly.
Gland packings must be tightened correctly, to prevent exces-
sive temperatures due to packings running hot.
3
Transport and interim storage
3.1
Transport
Transport of the unit requires proper preparation and handling.
Always make sure that the pump or the unit remains in
horizontal position during transport and cannot slip out of the
transport suspension arrangement. Do not use a lifting sling on
the free shaft end of the pump or on the motor eyebolt.
If the pump / unit slips out of the suspension
arrangement, it may cause personal injury and damage
to property!
D00311
Fig. 1
Transport of the pump
Fig. 2
Transport of the complete unit
3.2
Interim storage (indoors) / Preservation
When the unit is temporarily put into storage, only the wetted
low alloy components (e.g. JL 1040, JS 1030, A 216 Gr. WCB,
etc.) must be preserved. Commercially available preservatives
can be used for this purpose. Please observe the
manufacturer’s instructions for application/removal.
The relevant procedure is described in section 6.3.
The unit / pump should be stored in a dry room where the
atmospheric humidity is as constant as possible.
If stored outdoors, the unit and crates must be covered by
waterproof material to avoid any contact with humidity.
Protect all stored goods against humidity, dirt,
vermin and unauthorized access! All openings
of the assembled unit components are closed and must only be
opened when required during installation.
All blank parts and surfaces of the pump are oiled or greased
(silicone-free oil and grease) to protect them against corrosion.
4
Description of the product and
accessories
4.1
Technical specification
RPH pumps are used for handling the large variety of crude oil
products, mainly in refineries and chemical and petrochemical
plants.
4.2
Designation
Type series
Material variant
Version with inducer
Discharge nozzle DN
Nominal impeller dia. in mm
Special hydraulics (B-hydraulics)
RPH S1 I 80 - 280 B
4.3
Design details
Horizontal, radially split volute casing pumps in back pull-out
design, to API 610, 10th edition and ISO 13709, with radial
impeller, single-flow, single-stage, centreline pump feet.
4.3.1
Pump casing
Radially split, consisting of volute casing with casing wear ring
and casing cover. The volute casing, the casing cover and the
seal cover form the internal pump chamber.
The wall thickness of the casing includes a corrosion allowance
of 3 mm (0.12 in.).
On some pump sizes, pump casings have a double volute, in
order to compensate radial forces.