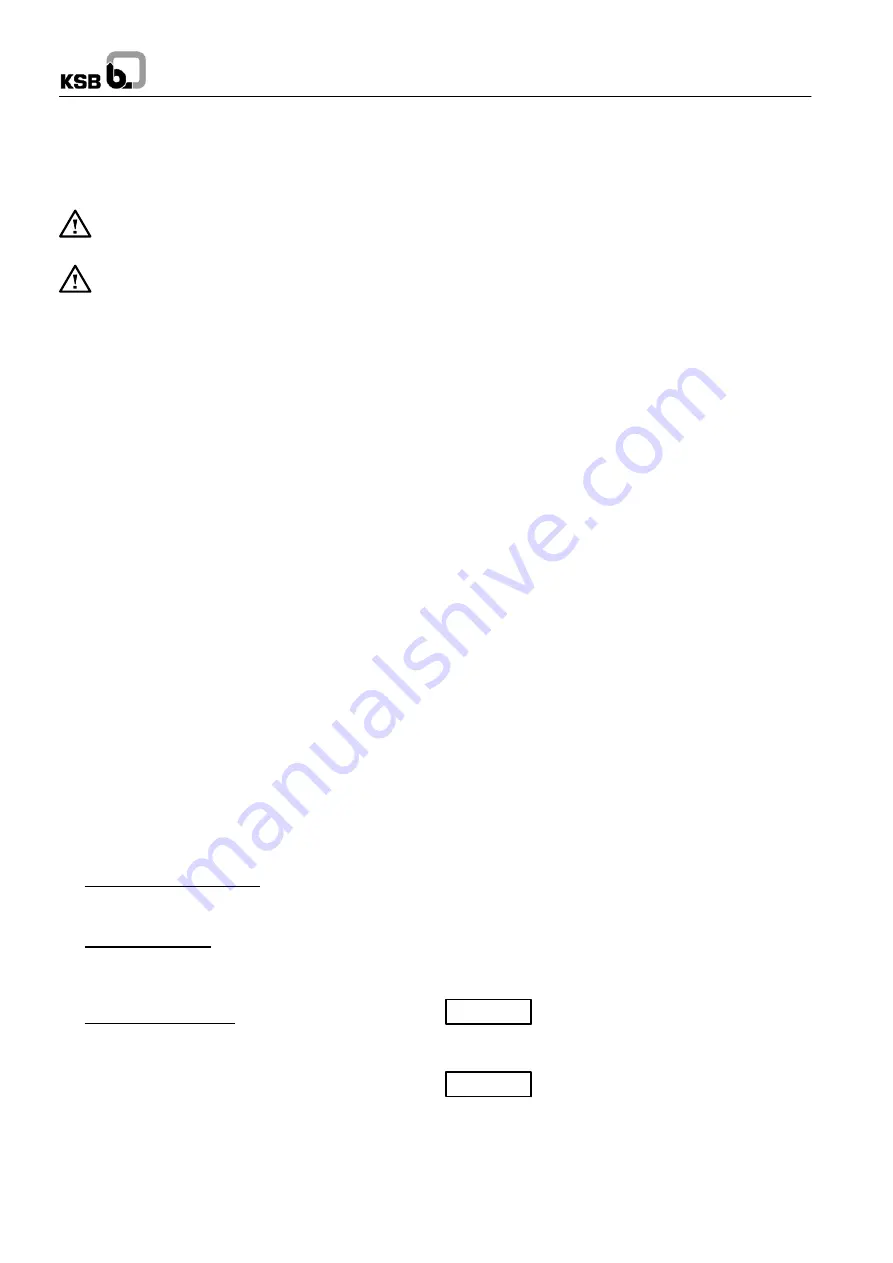
Caution
Caution
RPH
14
Use connections 6B to drain the pump set.
The flushing fluid used and any liquid residues in the pump must
be properly collected and disposed of without posing any risk
to persons or the environment.
7.4
Dismantling
Before dismantling the pump, secure it so as to make
sure it cannot be switched on accidentally. The shut-off
valves in the suction and discharge lines must be closed.
The pump must have cooled down to ambient
temperature, pump pressure must have been
released and the pump must have been drained.
Dismantling and reassembly must always be carried out in
accordance with the relevant sectional drawing.
7.4.1
Fundamental instructions and recommendations
Repair and maintenance work to the pump must only be carried
out by specially trained personnel, using
original spare parts
(see 2.7).
Observe the safety regulations laid down in section 7.1.
Any work on the motor shall be governed by the
specifications and regulations of the respective motor
supplier.
Dismantling and reassembly must always be carried out in
accordance with the relevant general assembly drawing.
The general assembly drawing and other relevant
documents are found in the annex. The dismantling
sequence can be derived from the general assembly
drawing.
In case of damage you can always contact our service
departments.
7.4.2
Dismantling (general)
1. Drain the oil as described in 7.2.2.2.
2. Remove the coupling guard.
3. Remove the coupling spacer, or if not applicable, remove
the drive.
If required, refer to the additional sheet concerning the
coupling!
4. Disconnect and remove all auxiliary pipework. Remove fan
hood 882, fan hub 881 and fan impeller 831.02, if
applicable.
5. Loop a rope tightly around the top stay of bearing bracket
lantern 330.
6. Unscrew hex. nuts 920.01 and pull complete bearing
bracket 330 with shaft 210 and impeller 230 out of volute
casing 102 using forcing screws 901.30. Clean the screw
threads beforehand. Note position of joint ring 411.10.
7. Bearing brackets B02 to B05:
Unscrew impeller nut 922.01 with threaded insert
(right-hand thread) and remove gasket 411.31 (if fitted) and
lockwasher 931.02.
Bearing bracket B06:
Unscrew impeller hub cap 260 (right-hand thread) and
remove joint ring 411.31. Bend back lockwasher 931.02,
remove impeller screw 906 with lockwasher and disc
550.87.
All bearing bracket sizes:
Pull off impeller 230 with a pull-off device and remove key
940.01. If a throttling bush is fitted, undo grub screws
904.38 and remove throttling bush 542.02.
8. Engage assembling jigs, if any, in the groove of shaft
protecting sleeve 524.01 by loosening the hex. head bolts
for fitting the assembling jigs and re-tightening them.
9. Undo hex. nuts 920.15 and separate bearing bracket 330
from the casing cover, using forcing screws 901.31. Shaft
protecting sleeve 524.01 (if fitted) with the complete
mechanical seal assembly will be pulled off the shaft in the
process. Take care not to damage O-rings 412.01/.31 (if
fitted).
10. Undo hex. nut 920.02 and remove seal cover 471.01.
Cooled version: Note position of O-rings 412.01/.31.
Pull seal cartridge out of casing cover 161.
Please observe the mechanical seal drawing!
Proceed in line with this drawing if further dismantling of the
mechanical seal is required. If required, refer to the
supplementary sheet!
11. Undo the hex. socket head cap screw in the coupling hub
and use an extractor to pull the coupling half off the pump
shaft. Remove key 940.02.
12. Undo grub screws 904.41/.42 and remove throwers
507.01/.02. Undo hex. socket head cap screws 914.01 and
take off the pump end bearing cover 360.01 with gasket
400.01. Undo hex. head bolts 901.37 and remove the
motor end bearing cover 360.02. Remove O-ring 412.22,
if required.
13. Carefully drive shaft 210 together with angular contact ball
bearing 320.02 and the inner race of cylindrical roller
bearing 322.01 (on special pump design including oil
thrower 508.01) out of the bearing bracket towards the
drive end.
14. Remove cylindrical roller bearing 322.01 (roller cage) from
the bearing bracket. Heat up the inner race of the cylindrical
roller bearing and pull it off the shaft. If oil thrower 508.01
is fitted, remove grub screw 904.20 and pull the oil thrower
off the shaft.
15. Bend back lockwasher 931.01, unscrew keywayed nut
920.21 (right-hand thread), remove lockwasher.
16. Heat up angular contact ball bearing 320.02 and pull it off
the shaft.
17. Clean all components and inspect them for signs of wear.
Re-work damaged components or replace by new ones.
7.5
Reassembly
7.5.1
General instructions
The pump shall be reassembled in accordance with the valid
rules of engineering practice.
Clean all dismantled components and check them for signs of
wear. Verify the dimensions given in section 7.5.5. Damaged
or worn components are to be replaced by
original spare
parts
. Make sure that the seal faces are clean and that the
sealing elements are properly fitted.
Always use new sealing elements (O-rings/gaskets) whenever
the pump is reassembled. Make sure that new gaskets have the
same thickness as the old ones.
Gaskets made of graphite or other asbestos-free materials
must always be fitted without using lubricants such as copper
grease or graphite paste.
Avoid the use of mounting aids as far as possible. Should a
mounting aid be required after all, use a commercially available
contact adhesive (e.g. ”Pattex”). The adhesive shall only be
applied at selected points (3 to 4 spots) and in thin layers.
Do not use cyanoacrylate adhesives (quick-setting adhesives)!
If in certain cases mounting aids or anti-adhesives other than
described herein are required, please contact the sealing
material manufacturer.
All graphite gaskets must only be used
once!
Never use O-rings that have been glued together from material
sold by the metre.
Do not coat O-rings with graphite or similar
products. Use animal fats or silicone-base or
PTFE-base lubricants instead. O-rings made of ethylene
propylene shall only be coated with silicone grease or soft soap;
never use mineral oils or greases!
The locating surfaces of the individual components must be
coated with graphite or similar before reassembly. The same
applies to screwed connections.