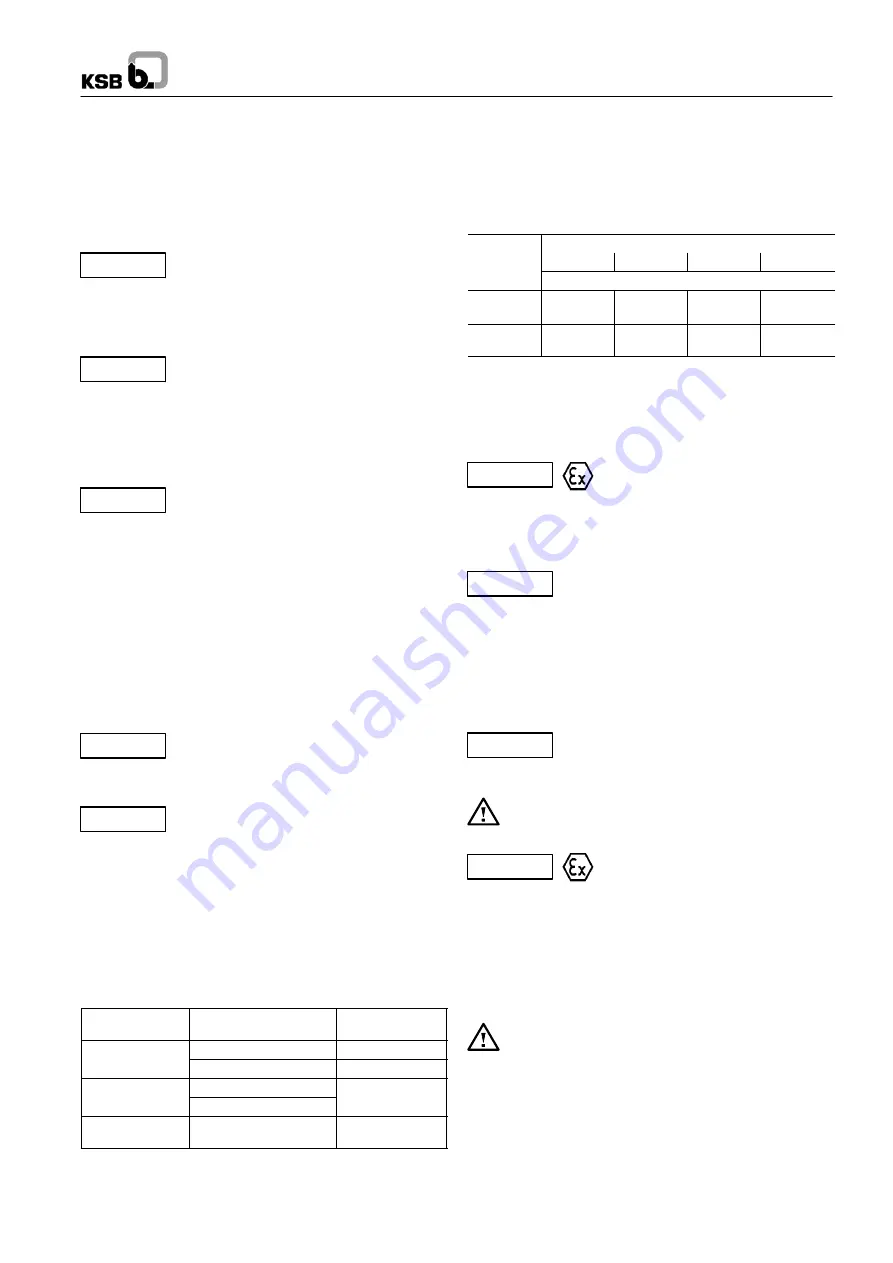
Caution
Caution
Caution
Caution
Caution
Caution
Caution
Caution
Caution
RPH
11
Then fill the reservoir of the constant-level oiler with oil and snap
it back into operating position. Screw vent plug in again. After
a short time check whether the oil level in the reservoir has
dropped. It is important to keep the reservoir properly filled at all
times!
If access to the vent plug is difficult or impossible, e.g. in cases
where the motor is arranged above the pump (piggy-back
arrangement), the oil can be filled in through the connection
elbow of the constant-level oiler.
The oil level shall always be below the level of
the vent opening arranged at the top edge of
the connection elbow.
During pump standstill the oil level can be checked at the oil
level sight glass.
6.1.2
Shaft seal
The mechanical seal has been fitted prior to
delivery. On variants with quench supply tank,
the tank must be fitted in accordance with the general
arrangement drawing (see also 6.1.3). Quench feed must also
be provided during pump shutdown. On variants with
pressurized dual mechanical seals, apply barrier pressure as
specified in the general arrangement drawing prior to starting
up the pump (see 6.1.3). Barrier pressure must also be provided
during pump shutdown.
For external liquid supply, the quantities and
pressure specified in the data sheet and
general arrangement drawing shall be applied.
6.1.3
Priming the pump and checks to be carried out
Before start-up, the pump, suction line and thermosyphon
vessel, if any, must be vented and primed. The shut-off valve in
the suction line must be fully open.
Fully open all auxiliary lines provided (flushing, barrier, cooling
liquid, etc.) and check the throughflow.
For water cooling, use suitable non-aggressive cooling water
not liable to form deposits and not containing suspended solids.
(Hardness: on average 5dH; (
~
1 mmol/l); pH > 8, or conditioned
and neutral with regard to mechanical corrosion).
Inlet temperature t
E
= 10 to 30
°
C
Outlet temperature t
A
max. 45
°
C
Dry running of the pump will result in
mechanical seal failure and must be
avoided!
6.1.3.1 Cooling
In general, the shaft seal must be cooled if the
vaporization pressure of the fluid handled is
higher than the atmospheric pressure.
Depending on the fluid handled, the system pressure and the
mechanical seal material, the limit may change (example: hot
water).
6.1.3.1.1 Cooling of the pump
The casing cover, the bearing bracket and the casing support
on the baseplate can be cooled.
p
allow.
= 10 bar
p
test
= 15 bar
Cooling liquid quantities:
Fluid temperature [
°
C] Cooling liquid
quantities [m
3
/h]
Casing cover
< 250
0.3
Casing cover
< 400
0.6
Bearing bracket
200
1)
/ 250 bis 315
2)
0 2
Bearing bracket
> 315
3)
0.2
Support on
baseplate
> 250
0.2
1) For n = 3500 1/min and n = 2900 1/min in conjunction with triple bearing
assembly. In all other cases from 250
°
C!
2) Water cooling or fan impeller
3) Water cooling (and optional fan impeller)
The cooling liquid quantities indicated are based on
D
t = max
15
°
C.
6.1.3.1.2 Cooling of heat exchanger
For mechanical seals with product circulation the following
cooling liquid quantities must be provided for the heat
exchanger:
n=1/min
Bearing bracket
B 02
B 03
B 05
B 06
m
3
/h
1750/
1450
0.35
0.5
0.6
0.8
3500/
2900
1.2
1.2
1.8
-
Fig. 10
Cooling liquid quantity
6.1.3.2 Heating
The casing cover can be heated by feeding hot water or steam
(up to t = 150
°
C, p = 10 bar). In this case the casing cover is
sealed off with O-rings made of ethylene propylene.
Observe
permissible
temperature
classes.
6.1.4
Checking the direction of rotation
When the unit has been connected to the electric power supply,
verify the following (local and national regulations have to be
taken into account separately):
For trouble-free operation of the pump, the
correct direction of rotation of the impeller is of
paramount importance. If running in the wrong direction of
rotation, the pump cannot reach its duty point; vibrations and
overheating will be the consequence. The unit or the shaft seal
might be damaged.
Correct direction of rotation:
The direction of rotation must correspond to the direction
indicated by the arrow on the pump. Verify by switching the
motor on and then off again immediately.
On pumps fitted with inducers, the direction of
rotation must only be checked with the
pump/motor coupling removed, otherwise the inducer may
work loose and damage the pump.
Before checking the direction of rotation make sure that
there is no foreign matter in the pump casing.
Never hold your hands or any other objects into the pump!
Do not run the pump without liquid while
checking the direction of rotation! If it is
not possible to fill the pump, the direction of rotation must be
checked with the pump/motor coupling removed.
If the pump runs in the wrong direction of rotation, interchange
two of the three phases in the control cabinet or motor terminal
box.
The safety instructions set forth in section 2.9.3 must be
complied with.
6.1.5
Cleaning the plant piping
The cleaning operation mode and duration for flushing
and pickling service must be matched to the casing and
seal materials used.
6.1.6
Start-up strainer
If a start-up strainer has been fitted to protect the pumps against
dirt and/or to retain contamination from the plant, the strainer’s
contamination level must be monitored by measuring the
differential pressure so as to ensure adequate inlet pressure for
the pump.
For installation and monitoring, see additional instruction sheet.